伊斯卡:航空航天—刀具改变工艺
在航空航天零件的加工中,主要的挑战与零件材料相关。钛合金、高温超级合金(HTSA)和耐蠕变钢的切削加工困难,是整个飞机供应链的加工瓶颈。这些材料的机械加工性能差,导致切削速度低,大大降低了生产率,缩短了刀具寿命。而这些因素都与刀具直接相关。事实上,当处理难以加工的典型航空航天材料时,刀具的功能性决定了现有生产力的水平。实际情况是,切削刀具的发展滞后于机床,而这种差距限制了高端机床在制造航空部件时性能的发挥。
现代飞机,特别是无人机(UAV),复合材料的应用比例显著增加。复合材料的高效加工需要特殊刀具,这是航空航天工业技术飞跃的焦点所在。
航空级铝材仍是机身部件广泛使用的材料。铝的加工看似简单,但选择合适的刀具是成功地高效加工铝所需的密钥。
复杂的零件形状是涡轮发动机技术的一大特征。大多数几何形状复杂的航空发动机部件都是在腐蚀性极强的环境下工作,并由难以切削的材料制成,如钛合金和高温超级合金(HTSA),以确保所需的寿命周期。复杂的形状、机械加工性能差和高精度的需求相结合形成了生产制造这些零件的主要困难。先进的多轴加工中心可实现各种去除余量的策略,从而更有效地加工复杂轮廓。但是刀具是直接与零件接触的,对加工的成败有很大的影响。过度的刀具磨损会影响零件表面精度,而不可预测的刀具断裂则可能导致整个零件报废。
先进的多任务加工机床、瑞士型车床和安装动力刀座的车床深刻改变了小型零部件的制造工艺,如飞机上各种液压和气动系统、致动器和附件。因此,航空航天工业需要越来越多针对这些先进机床而设计的特殊刀具,以达成加工效率最大化。
切削工具——制造系统中最小的元素——成为显著提高性能的关键支撑。因此,航空航天零件制造商们和机床制造商们亟需刀具制造商提供技术创新的解决方案,使切屑去除率达到新水平。解决方案的目标很明确:提高生产率和延长刀具寿命。加工具有复杂形状的特殊航空零件和大型机身部件需要一个可预测的刀具寿命周期,以进行可靠的工艺规划,并及时更换失效的刀具或可更换的切削部件(如刀片)。
刀具制造商在寻找理想解决方案方面的选择有限,也许只能从刀具材料、刃口形状和靠谱的鲁棒性设计这些方面考量。尽管选择有限,刀具制造商仍全力以赴提供新一代刀具,以满足航空航天业不断增长的需求。虽然新冠病毒严重阻碍了产业的发展,但这并不意味着产业需求的减少。最新的刀具设计充分证明了刀具制造商对航空零部件生产需求的响应。
冷却射流
在加工钛合金和高温超级合金(HTSA)和耐蠕变钢时,高压冷却(HPC)是提高性能和加工效率的有效工具。精准直达的高压冷却射流(HPC)可以显著降低切削区域的温度,确保形成小的片状切屑。与传统冷却方式相比,这有助于获得更高的切削参数和更长的刀具寿命。精准直达的高压冷却HPC越来越多地应用于难切削材料的加工,是航空航天零部件制造的一个明确趋势。因此,刀具制造商们认为高压冷却HPC刀具是一个重要研发方向。
伊斯卡,刀具制造领域的领军企业之一,拥有丰富多样的高压冷却刀具品种。2020年,伊斯卡通过引入“经典”HELI2000和HELIMILL可转位刀片的新型双刃铣刀扩展了其产品范围。这一步是伊斯卡开发该产品系列的又一里程碑式产品系列。
上世纪九十年代,由伊斯卡首推的可转位铣刀HELIMILL系列,夹持螺旋刃铣刀片。新设计使得刀片装夹于刀体后形成的刀片前角及后角保持恒定,进而使得切削轻快平顺,显著降低机床功率消耗。HELIMILL铣刀的设计理念成为90°主偏角可转位铣刀设计中被大家广为熟知并认可的概念。
通过对HELIMILL铣刀的逐步修正与改进,伊斯卡增添了相同理念下额外的铣削产品系列和具有更多切削刃的刀片。优异的性能及丰富的刀具周边产品使其在机加工行业应用广泛。因此,在经过验证的HELIMILL系列中添加现代高压冷却HPC刀具设计是对客户需求的径直响应,也是下一步需要开发的刀具系列。
在车削方面,伊斯卡大大扩展了其组装模块化刀具产品系列,其中包括带有可转位刀片的刀杆及可换式刀头。通过使用锯齿接触面连接,这些刀具可适用于搭载不同形状刀片的各种刀头,包括螺纹车削和标准ISO车削刀片,针对不同应用均更具灵活性。
伊斯卡提供沿袭传统设计和抗振设计的刀杆,并根据应用进行区别:圆柱柄或多边形锥柄。圆柱头铣刀的一个共同特点是内冷却射流直接输送到所需的刀片切削刃。根据圆柱柄刀具直径的不同,冷却射流最大压力从30bars至70 bars不等。而带有多边形锥柄的刀具可实现300 bars的超高压冷却。通过降低切削区域温度和改善切屑控制及排屑,冷却射流的充分供给提高了刀具寿命。在航空航天业中应大幅增加这一产品系列的应用。
钻孔解决方案
复合材料加工充满了各种陷阱与缺陷。复合材料的高耐磨性加快了刀具磨损,这缩短了刀具寿命,影响了刀具性能。钻孔是复合材料加工中最常见的切削操作,因此即使是钻孔刀具在功能上的微小改进也是至关重要的。
伊斯卡开发了一系列专门针对复合材料加工的新型钻头。为了提高耐磨性,这些钻头的切削刃部分通常都由超硬聚晶金刚石(PCD)或金刚石涂层制成。根据钻头直径的不同,钻尖可以使用整体PCD刀头或PCD焊片,在这两种情况下都可以重新修磨5次。CVD金刚石涂层整体硬质合金钻头另一个独特的设计点是:主切削刃呈折线状。在加工复合材料时,更容易产生加工振动。切削刃的折线形设计大大减少了分层和毛刺,特别是在加工碳纤维增强塑料(CFRP)和碳纤维层压板时。
除复合材料,金刚石涂层钻头也适用于加工其他耐磨的工程材料。如有必要,也可提供带内冷却通孔的选项。
小直径深孔的钻削是制造航空航天零件的一种常见作业。伊斯卡的新型整体硬质合金钻头直径范围为3-10 mm(0.125"-0.391"),专门用于这类作业。该钻头系列结合了钻尖形状、双导向条设计、抛光的排屑槽、复合涂层和内冷却通孔,在难加工的奥氏体不锈钢及耐蠕变钢和铁基合金加工中,可实现一次进刀达成50xD钻深比。
无惧任何复杂加工应用
因空气动力学的定义,航空发动机涡轮、压气机、叶轮和整体叶片转子(IBR)需要具备复杂形状。旨在提高航空发动机效率的新发展又进一步增加了这种复杂性。技术的进步带来了生产成型零件的新方法,特别是3D打印,这大大减少了工件材料的余量。然而,在制造形状复杂的航空航天零件的最终成形方法中,机加工仍然是最常见的方法。五轴加工和CAD/CAM系统的进步丰富了制造商的解决方案,以克服零件生产中的困难。
在具有复杂形状表面航空航天零件的五轴加工中,鼓形铣刀具有良好的应用前景。伊斯卡已开发了一系列直径范围8 – 16mm(.312" - .500")的鼓形铣刀,有两种设计结构:整体硬质合金立铣刀及带有变形金刚螺纹接口的可换头式刀具。将这些刀具应用于加工中可有效优化叶片的生产制造。
可靠的多任务处理
在紧凑型多任务机床和瑞士型车床上进行加工时,能否有效排屑很大程度上取决于刀具的正确选择。为了提高生产率,需要最大限度地保持刀具的刚度和最小化刀具的悬伸以在受限空间加工作业。
最近,伊斯卡推出了NEOCOLLET卡簧夹头,新款刀夹系列,提供了一种替代ER卡簧用于夹紧刀具的方案。该系列适配的典型刀柄之一是锥柄,可直接内置于弹簧夹头刀柄中,确保刚性和可靠的连接,以提高刀具性能。新系列可夹持伊斯卡硬质合金T型可换槽面铣刀头的夹具。
如前所述,采用高压冷却可以极大地改善加工结果,特别是在加工钛、高温超级合金(HTSA)和难加工的不锈钢时,这些材料是飞机液压和气动系统以及小型配件的主要材料。新型车刀系列具有方柄和螺丝夹紧的55°菱形刀片,采用HPC技术,便于在小直径零件上进行纵向车削、端面车削和仿形车削。
所有案例都说明了刀具制造商正试图寻找更为有效的解决方案,以满足航空航天工业的新要求。由于新冠病毒的影响,工业增长放缓,飞机产量减少,但刀具制造商对合作伙伴需求的关注并未减弱。相反,伊斯卡已经开发了新的先进切削刀具,并努力将其成功升级应用于即将恢复的飞机生产中。
(伊斯卡技术经理 Andrei Petrilin)
声明:本网站所收集的部分公开资料来源于互联网,转载的目的在于传递更多信息及用于网络分享,并不代表本站赞同其观点和对其真实性负责,也不构成任何其他建议。本站部分作品是由网友自主投稿和发布、编辑整理上传,对此类作品本站仅提供交流平台,不为其版权负责。如果您发现网站上所用视频、图片、文字如涉及作品版权问题,请第一时间告知,我们将根据您提供的证明材料确认版权并按国家标准支付稿酬或立即删除内容,以保证您的权益!联系电话:010-58612588 或 Email:editor@mmsonline.com.cn。
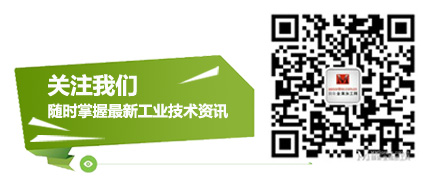
- 暂无反馈