从5mm到0.5mm,突破钛合金翼面蒙皮加工
——国宏工具助力南京航空航天大学工艺优化 化解老大难问题
航空制造企业中流传着这样一句话:“要把一克重量送上天,需要花费一克黄金。”这对占据了飞机80%面积、21%重量的蒙皮零件来说,可谓是“至理名言”。包裹在飞机外壳的蒙皮,为了满足飞机减重、动力提升等需求,零件厚度被“一降再降”,新一代战术制导飞行器的金属蒙皮厚度最薄处甚至仅0.5mm,如同鸡蛋壳般。同时,作为直接承受飞机载荷、对飞机疲劳寿命起决定性作用的零件,蒙皮不仅采用了高强度钛合金等新材料,对加工精度和表面质量都有着极高的要求,其加工技术一直被公认为是行业难题。
南京航空航天大学(以下简称“南航”)作为全国知名高校,以及数次参与我国航空航天重要型号预研、技术攻关、试验任务的专业科研机构,一直致力于多类型航空航天“难加工”零件的工艺优化。针对某军工企业某型号翼面钛合金蒙皮零件易切穿、成品率低的问题,南航特别成立了项目团队,就其零件结构、材料特性、装夹方式、加工工艺等进行了系统性探究,并联合国宏工具系统(无锡)股份有限公司(以下简称“国宏工具”),共同研发了专用的直刃结构整体硬质合金铣刀,成功完成了厚度最小处仅0.5mm、最大处1mm,且带有0.5mm厚度立筋结构的钛合金薄壁蒙皮试验件高效高精加工,为整体薄壁腹板类零件的加工提供了有益借鉴。
钛合金+复杂薄壁结构,加工难度成倍上升
该款翼面蒙皮结构复杂,如图1所示,主体结构为1mm厚的腹板,尺寸接近0.8 X 0.3m,跨度很大;腹板上还带有多边形型腔结构,型腔侧壁的壁厚仅为0.5mm,高度为3.5mm,属于典型的弱刚度结构。蒙皮零件的毛坯为5mm厚钛合金板材,材料去除率高达 92.6%。加之零件整体均由TA15钛合金制成,其材料的室温强度、高温强度以及焊接性能均高于TC4 钛合金等其他材料,更使得零件的加工难度成倍上升。
图1:蒙皮零件的主体结构
南航项目团队在对原加工工艺分析后发现,刀具的“不合适”是频繁产生过切问题的关键。在刀具切入板材时,加工区域的材料会发生塑性变形,同时受到刀具所产生的向上牵引作用发生一定程度的翘曲。随着余量的不断去除,板材刚度逐渐下降,切削力的作用便让实际切深越来越大,从而导致腹板的过切,甚至切穿。
图2:被切穿的腹板
明确方案优化重点后,南航项目团队便开始寻找合适的刀具厂商。国宏工具作为国产硬质合金刀具的领先企业,也是与南航保持着紧密联系的校企合作伙伴,自然成为了团队的第一选择。“国宏工具是国内少数几家拥有刀具全制程自主生产能力的企业,在航空航天难加工材料领域有着深厚的技术和经验积累,更为难得的,是他们拥有高水平的切削实验室,无论是‘硬件’还是‘软实力’都十分契合南航对于技术合作伙伴的需求。”南航项目团队负责人介绍说。
大胆创新,研发钛合金专用直刃铣刀
针对高硬度材料的侧面加工、槽加工,目前行业多采用大螺旋角立铣刀,因为螺旋角越大,工件与刀刃的接触线就越长,施加到单位长度的刀刃上的负荷也就越小,从而有利于延长刀具寿命,也能在一定程度上提升切削稳定性。但国宏工具技术部门在深度探究后发现,针对该款薄壁零件,原本为立铣刀带来性能提升的“螺旋角”正是板材切穿的“罪魁祸首”。
“多次模拟加工后,我们发现,带螺旋角的铣刀由于刀齿沿着螺旋排列,且每个刀齿的切削位置不同,因此切削力被分散到整个刀具上,在加工中便会对腹板产生‘上拉—下压’的上下往复作用,这时一旦板材局部厚度不均匀存在翘曲凸起,就会出现过切。”国宏工具技术总监王必永先生介绍说,“我们大胆提出了研发螺旋角为0°的钛合金专用直刃铣刀的想法,看是否能通过将切削力集中在与工件表面垂直方向的方式,避免过切。”
图3:国宏工具直刃铣刀实物图
随后,国宏工具技术部门快速设计出了对比实验方案:将两款采用了相同硬质合金基体材质与国宏自主研发的AlCrN基涂层材质的螺旋角铣刀和直刃铣刀,通过同款三轴加工中心对目标零件的钛合金毛坯板材进行加工试验。同时,利用压电式仪削力测量系统同步测量作用于工件和刀具上的切削力。
测试结果显示,不同于带螺旋角的铣刀加工时会在轴向产生正负两向交替往复的切削力,直刃铣刀产生的轴向力始终对腹板产生下压作用,因此能够避免腹板被刀具切穿的问题。此外,下压的切削力有助于压紧腹板零件,辅助实现真空吸盘的严密吸附,从而保证切削过程中切深的准确性,提升腹板的加工精度。实验还发现,较之带有螺旋角的铣刀,直刃铣刀在相同切削参数下的切削力更小,因而能够降低切削过程中产生的残余应力,减少低厚度腹板结构的加工变形,如图4所示。
图4:带螺旋角的常规铣刀与直刃铣刀的切削力大小对比
南航项目团队在内部测试后,对国宏工具所研发的直刃铣刀的性能表示了高度认可。“采用直刃铣刀来加工钛合金薄壁零件是一个颠覆传统认知的创新设想,国宏工具团队以高效的执行力和强大的技术力将设想变成了现实,为我们攻坚这一项目带来了突破。”南航团队负责人说道,“此外,国宏工具自主研发的钛合金专用涂层,也是这款刀具能够充分发挥效用,达到理想加工效果的关键。”
加工难点“逐一击破”,实现工艺优化
找到合适的刀具,仅是方案优化的第一步,如何优化设计加工工艺成为了摆在南航项目团队面前的又一难题。根据以往的经验,基于“短板优先”的原则,团队先设计了总体加工工序——首先在板材上加工型腔(图5 a)),从型腔中心位置螺旋下刀,切深达到槽腔深度后刀路逐步向外扩展,完成最薄弱的型腔内腹板的加工(图5 b))。之后再进行槽铣,去除各型腔间的材料(图5 c))。最后对型腔立筋结构的内外圈进行加工(图5 d))。
图5:蒙皮样件的工序设计
而后,便是对单工序加工难点的“逐个击破”了。在完成型腔内部粗加工后,转角部位还残留有较多材料,且这些转角大多十分狭窄,在其内进行粗精加工难度很大。初步的设计方案是采用小直径直刃铣刀,以侧铣方式进行,但很快便出现了小直径刀具难以承受逐渐增大的切削力而折断的问题,而若通过减少切深与进给速度来控制切削时刀具的载荷,又会极大影响加工效率。因此,国宏工具技术团队便提出了采用插铣方式的可能性,并且直刃铣刀也非常适用于插铣工艺。在得到南航项目团队认可后,经过多次加工实验的国宏工具技术团队确定了具体的工艺参数(如表1所示)。
对型腔内外侧壁进行精加工是最后一道工序,在零件刚性最弱时,将侧壁内外两侧余量一次性高效去除,并确保尺寸精度到位的严苛要求,也使其成为了难度最大的一道工序。如何实现?确定切削速度与每齿进给量是关键。“国宏工具在前期对直刃铣刀切削力的测试数据,为我们这一步序的工艺设计提供了很大帮助。” 南航团队负责人介绍说。
国宏工具实验发现,切削速度对直刃铣刀的切削力影响不大,相反,每齿进给量与切宽则对直刃铣刀的切削力产生了显著影响,并且,切宽变化带来的影响更大。基于此数据,南航项目团队提出,在对型腔内外侧壁进行侧铣加工时,可以采用高速切削,配合较小的每齿进给量与切宽,从而在减少切削力的同时获得较高的材料去除率。
表 2:内/外侧壁精加工工艺参数
“经过我们团队成员和各方合作伙伴,尤其是国宏工具技术部门的共同努力,蒙皮样件最终成功通过了验收,不仅将精度、表面质量误差控制在±0.05mm以内,还大幅提升了加工效率,加工耗时较原有工艺减少了约53%,且加工过程稳定。” 南航团队负责人总结道,“我们相信,南航与国宏工具正式成立的‘高性能刀具系统技术联合实验室’,接下来将会带动更多的研究项目落地。”
图 6:完成加工的蒙皮样件
关于国宏工具
国宏工具系统(无锡)股份有限公司成立于2004年,注册资本近3.7亿元,是一家专业从事超高精密数控刀具和集成电路封装楔形劈刀研发、生产、销售和服务的高新技术企业。公司拥有各种先进加工、检测设备达290余台,建有涂层产线,具备刀具全制程生产能力,核心产品包括硬质合金刀具、超硬刀具、陶瓷刀具和集成电路封装楔形劈刀。公司以市场为导向,针对需求旺盛的电子信息、航空航天、汽车、通用机械、模具等领域,推出了多种刀具产品以及提效解决方案,与捷普集团、富士康集团、三星集团、中国航发、中国电科、三一重工、利纳马、博世集团等拥有长期的合作关系。
了解更多公司信息,请查阅 www.wxgh.com.cn或关注国宏工具官方微信:
(国宏工具)
声明:本网站所收集的部分公开资料来源于互联网,转载的目的在于传递更多信息及用于网络分享,并不代表本站赞同其观点和对其真实性负责,也不构成任何其他建议。本站部分作品是由网友自主投稿和发布、编辑整理上传,对此类作品本站仅提供交流平台,不为其版权负责。如果您发现网站上所用视频、图片、文字如涉及作品版权问题,请第一时间告知,我们将根据您提供的证明材料确认版权并按国家标准支付稿酬或立即删除内容,以保证您的权益!联系电话:010-58612588 或 Email:editor@mmsonline.com.cn。
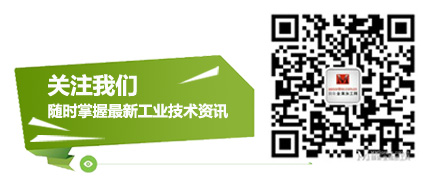
- 暂无反馈