创新刀具驱动制造业升级:工艺优化的技术革命
近年来,随着全球制造业向高精度、高效率、智能化方向加速转型,切削加工作为核心制造工艺正面临前所未有的技术挑战。在航空航天、新能源汽车、精密模具等高端制造领域,传统切削刀具已难以满足复杂工况下的加工需求。在此背景下,以材料科学突破、智能技术融合、结构设计创新为核心的切削刀具技术革命,正在重构现代加工工艺的底层逻辑,推动制造业实现从"经验驱动"向"数据驱动"的跨越式发展。
一、材料创新:超硬复合材料的突破性应用
刀具材料的演进史本质上是人类突破物理极限的探索史。当前,以金刚石(PCD)、立方氮化硼(PCBN)为代表的超硬材料,通过纳米复合技术实现了性能的阶跃式提升。山特维克推出的第三代PCBN刀具,通过梯度结构设计使抗冲击韧性提高40%,在淬硬钢加工中刀具寿命突破1000分钟。国内企业如株洲钻石研发的纳米晶金刚石涂层刀具,将基体硬度提升至95GPa的同时,通过晶界工程将摩擦系数降至0.05,成功应用于航空发动机叶盘加工。
在复合材料加工领域,金刚石涂层刀具与多层梯度涂层的协同创新解决了碳纤维增强塑料(CFRP)的分层难题。日本三菱开发的DLC(类金刚石)涂层刀具,通过精准控制sp³键比例,使切削温度降低200℃,加工表面粗糙度达到Ra0.2μm。这种材料-涂层系统化创新,使得铝合金/碳纤维叠层构件的一次装夹加工成为可能,显著提升新能源汽车电池箱体加工效率。
二、智能感知:切削系统的数字化蜕变
物联网技术与切削刀具的深度融合,催生出具有自感知、自决策能力的智能刀具系统。肯纳金属开发的iQC系列智能刀柄,集成振动、温度、应力多模态传感器,通过边缘计算实时优化切削参数。在西门子成都数字化工厂的应用数据显示,该系统使钛合金零件加工颤振降低70%,工艺优化响应时间缩短至50ms。这种"感知-分析-执行"的闭环控制,标志着切削加工从被动适应向主动调控的范式转变。
数字孪生技术的引入进一步拓展了工艺优化的维度。山高刀具建立的刀具全生命周期数字模型,通过机器学习算法对10万+加工案例进行特征提取,可在虚拟环境中完成刀具选型、路径规划、磨损预测的协同优化。在某航空结构件加工项目中,该技术使工艺验证周期从14天压缩至36小时,材料去除率提升3.2倍。
三、结构创新:仿生学与拓扑优化的协同进化
在极端加工条件下,刀具结构设计正经历从经验设计向仿生学、拓扑优化的科学化转型。伊斯卡研发的仿鲨鱼皮微织构刀具,通过在刀-屑接触区构建微米级凹坑阵列,使切削力降低18%,切屑卷曲半径可控精度达±0.05mm。这种生物仿生设计在高温合金加工中展现出显著优势,镍基合金车削时的积屑瘤生成率下降60%。
模块化刀具系统通过拓扑优化实现性能突破。瓦尔特推出的Tiger·tec® Gold模块化铣刀,采用非对称齿距设计和三维复杂槽型,使每齿进给量提升至0.3mm的同时保持加工稳定性。在风电齿轮箱加工中,该刀具系统通过快速组合实现粗精加工一体化,工序缩减率达40%,单个工件加工成本降低28%。
四、绿色制造:可持续性技术的前沿探索
在"双碳"目标驱动下,干式切削与微量润滑(MQL)技术取得突破性进展。住友电工开发的纳米粒子增强MQL系统,通过粒径控制在50nm的Al₂O₃粒子实现润滑膜自修复功能,在铸铁加工中刀具寿命延长3倍,冷却液用量减少95%。国内华中科技大学研发的激光辅助车削技术,通过精准能量输入使难加工材料切削温度降低400℃,为实现完全干式切削提供了新路径。
增材制造技术为刀具绿色再造开辟新赛道。Sandvik采用激光熔覆技术制造的3D打印铣刀,通过内部晶格结构设计实现质量减轻30%,冷却通道传热效率提升5倍。这种"设计-制造-再制造"的循环模式,使刀具材料利用率从传统工艺的45%提升至82%,碳足迹降低60%。
五、未来展望:跨学科融合的技术图景
随着量子计算、超材料、柔性电子等前沿技术的渗透,切削刀具正朝着功能集成化、性能自适应方向发展。德国弗劳恩霍夫研究所正在研发的"活性刀具",通过压电材料实现切削刃微米级动态调整,可实时补偿加工变形。这种具有"机械智能"特征的刀具,或将彻底改变五轴加工中的误差补偿模式。
在制造范式层面,切削刀具创新正在推动形成"工艺-装备-材料"的协同进化生态。刀具制造商与机床企业、软件开发商共建的数字工艺链,通过工艺知识图谱构建和加工参数云端共享,使制造系统具备自主进化能力。这种生态化创新模式,将加速制造业向"零缺陷、零浪费、零延误"的智能制造目标迈进。
结语:
切削刀具的技术革新已超越单纯的工具改进范畴,成为驱动制造业转型升级的核心要素。在材料基因组计划、工业互联网、人工智能等战略技术的赋能下,切削加工正突破物理边界,向着更高效率、更优质量、更低能耗的方向演进。这场始于刀具创新的技术革命,终将重塑整个制造价值链的竞争格局。
声明:本网站所收集的部分公开资料来源于互联网,转载的目的在于传递更多信息及用于网络分享,并不代表本站赞同其观点和对其真实性负责,也不构成任何其他建议。本站部分作品是由网友自主投稿和发布、编辑整理上传,对此类作品本站仅提供交流平台,不为其版权负责。如果您发现网站上所用视频、图片、文字如涉及作品版权问题,请第一时间告知,我们将根据您提供的证明材料确认版权并按国家标准支付稿酬或立即删除内容,以保证您的权益!联系电话:010-58612588 或 Email:editor@mmsonline.com.cn。
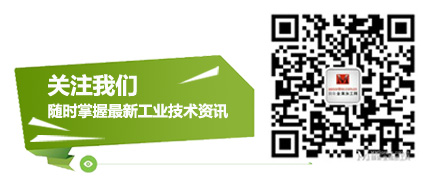
- 暂无反馈