浅谈外圆车削的常见问题及解决方法
在机械制造业中,外圆车削(外圆车刀)是最基本,最普通的一种加工形式。无论是手动操作或自动进给方法,必须严格保持加工零件与车刀之间的运动关系:主轴每转一转,刀具应均匀移动给一个进给量。主轴带着工件一起转动,主轴的运动经挂轮传递给进给箱,经过进给箱变速后(主要为获得所需的进给量)传递给光杠,并由光杠和溜板箱中齿轮装置传递给齿条,带动大拖板作给予一定进给量的均匀直线运动,使刀架上的刀具与加工工件作相对匀速切削运动,使加工零件获得一定的尺寸公差要求,型位公差要求和表面粗糙度的要求。在实际操作中,由于各种原因可能使主轴到刀具之间,刀具与加工工件表面切削状态等环节出现问题,引起车削外圆发生故障,影响产品的质量,影响正常的生产。以下将对各种情况一一列举,并说明解决方法。
一、尺寸精度达不到要求
产生的原因:
1.看错图样或刻度盘使用不当
2.没有进行试切削
3.量具有误差或测量不正确
4.由于切削热影响,使工件尺寸发生变化
5.机动进给没及时关闭使车刀进给超过台阶长度
6.车槽时车槽刀主切削刃太宽或太狭使槽宽不正确
7.尺寸计算错误,使槽深度不正确
预防方法:
必须看清图纸尺寸要求,正确使用刻度盘,看清刻度值。根据加工余量算出背吃刀量,进行试切削,然后修正背吃刀量。量具使用前,必须检查和调整零位,正确掌握测量方法。不能在工件温度高时测量,如测量应掌握工件的收缩情况,或浇注切削液,降低工件温度。
注意及时关闭机动进给或提前关闭机动进给用手动到长度尺寸。根据槽宽刃磨车槽刀主切削刃宽度。
二、产生锥度:
产生的原因:
1.用一顶一夹或两顶尖装卡工件时,由于后顶尖轴线不在主轴线上
2.用小滑板车外圆时产生锥度是由于小滑板的位置不正确
3.用卡盘装卡工件纵向进给车削时产生锥度是由于车床床身导轨跟主轴轴线不平行
4.工件装卡时伸出较长,车削时因切削力影响使前端让开,产生锥度 5.车刀中途逐渐磨损
预防方法:
车削时必须找正锥度、必须事先检查小滑板的刻线是否与中滑板刻线的“0”线对准。
调整车床主轴与床身导轨的平行度。尽量减少工件的伸出长度,或另一端用顶尖支顶,增加装卡刚性。选用合适的刀具材料,或适当降低切削速度。
三、圆度超差:
产生的原因:
1.车床主轴间隙太大
2.毛坯余量不均匀,切削过程中背吃刀量发生变化
3.工件用两顶尖装卡时,中心孔接触不良,或后顶尖顶的不紧,或产生径向圆跳动
预防方法:
车削前检查主轴间隙,并调整合适,如因主轴轴承磨损太多,则需更换轴承。要分粗精车。工件用两顶尖装卡必须松紧适当,若回转顶尖产生径向跳动,需及时修理或更换。
四、产生波纹的原因及处理方法
外圆表面按一定规律均匀产生的波纹,轻微时肉眼不易发现,如涂上红丹粉用砂布背面打磨或用细油石轻轻推磨即清晰可辨。严重时,手摸有明显不平感。如波纹的间距过大,恰与纵向进给机构齿条的周节相等,原因在于进给系统故障,齿条与小齿轮啮合不良,导致溜板在纵向移动中定期的间歇性窜动。若波纹间距于床身长丝杠的螺距相等且倾斜,原因可能是丝杠、齿条与小齿轮啮合出现下列三种情况之一:
1.丝杠于对合螺母相摩擦;
2.丝杠与溜板箱体孔相摩擦;
3.齿条与小齿轮两齿面在一端啮合。
波纹的间距较小,恰与光杠每转一周的溜板一端距离相等,而且此种波纹常表现为越靠近明显,这说明出现波纹的原因是光杠或同光杠保持相等传到关系的进给处齿轮,传动轴或有关零件有一定程度的损伤。可能是下列四种情况之一:
1.光杠走刀箱轴接间隙大,有松动;
2.光杠走刀箱转动轴套、轴承有损伤;
3.走刀传动齿轮磨损,销、轴窜动;
4.光杠、丝杠、操纵杠与溜板箱组装精度差。
波纹消除方法与预防措施:
1.当齿条与小齿轮啮合不在同一直线上时,应调整溜板的安装位置,用涂色法检验接触精度,使齿条与小齿轮两侧均匀啮合,即可消除波纹。
2.当齿条与小齿轮的齿顶与齿根为线接触时,往往是齿条与小齿轮的制造精度低造成,应设法更换齿条齿轮,即可消除波纹。
3.当齿条与小齿轮在一端啮合而出现斜向波纹时,要清除齿面杂物,检验接触精度,刮大溜板与溜板箱的接触面,调整齿条与小齿轮齿向啮合间隙,使接触状况改善,即可消除波纹。
4.当长丝杠与溜板箱孔或对合螺母摩擦而产生斜波纹时,要检验丝杠,恢复丝杠回转中心与对合螺母的同轴度以及与床面导轨的等距性,修复或更换磨损的丝杠托架或衬套。
5.当光杠与溜板箱进给机构传递不平稳时,应检验光杠,修复或更换箱内的进给传动件。
6.当光杠与走刀箱进给系统传递不平稳时,应消除光杠联接套齿轮轴套等端面不垂直度和销、键等联接件的松动,并以手驱动光杠传动系统来判断且排除回转的松紧不匀现象。
7.当光杠与床面导轨不等距时,要检验修复光杠回转中心线与床面导轨的等距性,检验并排除床面导轨扭曲不直度,恢复溜板与床面导轨的接触精度。
此外,如车头箱主轴轴承间隙过大,轴承刚性不足,主轴系各联接件、传动件传动不平稳,也可导致工件表面产生波纹。
五、车削工件时大时小的原因及处理方法
车削工件时大时小的原因。
A:工件装夹松动。
B:车刀磨损,车刀用钝,刀刃上出现缺口。
C:车削长轴时,顶尖松紧不适,顶尖磨损。跟刀架,中心架的支撑爪磨损或松紧调整不当。
解决方法:停车检查工件的装夹是否牢固,车具磨损,用钝,必须卸下车刀,重新在砂轮上刃磨或更换新刀,顶尖调整松紧,顶尖磨损更新,跟刀架中心架支撑爪的松紧要调整适宜,注意润滑和冷却,减少磨损。
六、出现表面拉毛表面粗糙度低劣
车削外圆时出现表面拉毛表面粗糙度低劣现象,产生原因。
A:车削时,切削用量配合使用不当(工件转速√,吃刀深度t,进给量S)
B:车具刀刃在不合理的车削过程中产生切削力过大发热,强度,硬度发生变化。车刀产生损坏或不锋利。在不当的切削用量下车削零件尤其在精车时(通常为最后一刀)工件表面粗糙留有明显刀痕,达不到表面粗糙度的要求。
C:表面出现拉毛现象。主要原因,刀刃不锋利。排屑不畅,铁屑排出成丝状或带状,缠绕工件表面,造成工件表面被带状铁屑严重拉毛影响零件的质量。
七、车削外圆小结
总之,车削外圆时产生的故障形式多种多样,既有设备原因也有工件材质问题,刀具问题,以及操作者等原因,在排除故障时要具体情况具体分析。通过各种分析和诊断找出具体影响因素,采取有效的解决方法,最主要的归纳以下几点:(1)认真,负责,保养调整机床,使机床达到一定的完好状态(精度)。(2)正确理解切削基本原理,合理掌握运用切削用量。(3)工件的装夹牢固,采用辅助手段使工件切削时减少工件的几何变形。(4)正确的使用各种牌号刀具,刃磨合理角度的刀具,使刀具在切削过程中,排屑流畅。(5)注意正确使用冷却液和润滑液,延长刀具使用寿命,提高生产率。
声明:本网站所收集的部分公开资料来源于互联网,转载的目的在于传递更多信息及用于网络分享,并不代表本站赞同其观点和对其真实性负责,也不构成任何其他建议。本站部分作品是由网友自主投稿和发布、编辑整理上传,对此类作品本站仅提供交流平台,不为其版权负责。如果您发现网站上所用视频、图片、文字如涉及作品版权问题,请第一时间告知,我们将根据您提供的证明材料确认版权并按国家标准支付稿酬或立即删除内容,以保证您的权益!联系电话:010-58612588 或 Email:editor@mmsonline.com.cn。
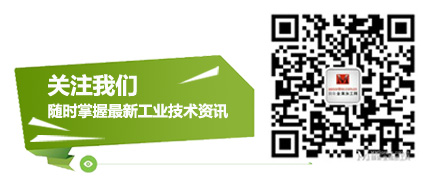
- 暂无反馈