破解高效加工迷思 接轨智能制造时代
【编者按】高效加工是在保证零件精度和质量的前提下,通过对加工过程的优化和提高单位时间材料切除量来提高加工效率和设备利用率、降低生产成本的一种高性能加工技术。
高压冷却液在机加工中的高效应用
据调查显示,机加工的总成本可分为两大部分,79%的固定成本和21%的可变成本。冷却液作为可变成本中的一部分,只占到了0.5%,与刀具相比,形成了1:10的成本差距。由此可见,冷却液的成本在机加工中是微不足道,但它却会影响固定成本(设备、人力等)和可变成本(刀具、材料等)。
首先,冷却液性能会影响刀具寿命和生产率。它会减少刀具磨损及换刀时间,减少铁屑与刀具的接触时间,从而提高切削速度、进给、切深等方面的生产率。因此,选择合适的冷却液,可同时提高刀具寿命和生产率10%以上。在这方面,福斯作为金属加工冷却液的巨头,相比起普通冷却液而言,能缩短加工时间、提高工件表面光洁度、以生产出更高质量的产品,达到更低的生产成本。
同时,福斯在高压冷却方面也颇有心得。采用高压冷却液优势在于改善断屑、排屑性能,提高切削参数,降低刀具磨损,延长刀具寿命,进一步改善工件表面粗糙度。普通的溢流冷却无法有效且准确地到达切削区,在加工区域会因局部加热而形成一道蒸气隔离层,蒸气隔离层会隔离切削区并阻止其散热。高压冷却可以完美地解决溢流冷却所带来的问题,高压冷却产生液压楔,减少碎屑同刀具的接触面积,能够更好地带走加工时产生的热量,这些优势无不体现在车削、铣削、钻孔等加工过程中。
当然,高压对于冷却液而言也不全是正面影响,在高压液体的循环下,冷却液会高速搅动,产生泡沫,这对加工而言是不利的。因此控制泡沫成为了冷却液生产商的一项挑战。目前大多数OEM的做法是避免使用含硅消泡剂,过滤器也会消耗掉一部分消泡剂,乳化液必须保持稳定,经受住压力下降,并保持低泡沫。福斯还认为,有效的高压冷却液需配合合适的机床、刀具,才可发挥其优势。例如在铣削时采用的刀具需是可转位立铣刀或可转位平面铣刀,同时选用合适的喷嘴,如此才能实现高压冷却液的功效。
颠覆传统的高效加工工艺
实现高效加工并非易事,而要在传统基础上颠覆创新,更是一项高难度的突破。在这一点上,号恩(Horn)刀具可谓是业界的佼佼者。其三大高效加工系列:高效率铰刀DR系列、插削系列、以刮代磨-刮削系列均从很大程度上改变了传统的高效加工工艺,实现了现代高效加工艺术。
我们在接收订单前,会先考虑客户对铰削的要求是什么?答案不外乎是对孔本身的要求(孔的公差、表面粗糙度、位置精度、直线度/圆柱度、同心度、平行度等等),或是延长刀具的寿命,或是实现较低的单件成本,又或是缩短加工中的停机时间。这些要求看似复杂多变,难以实现,但在高效率铰刀DR系列的配合下,一切都迎刃而解了。
高效率铰刀DR系列彻底颠覆了原来铰刀低转速,低进给的一贯形象,可以在高转速及高进给的状态下稳定的切削,通过高速切削提高加工效率,降低加工成本。其进给速度可高达7500 mm/min,是由可换式的刀片与独特的快换式机械装置连接而成的。同时,DR系列采用内冷设计,冷却液可通过刀杆内部喷射到刀片上,对刀头充分冷却,从而保证刀片有极佳的寿命。尽管刀具在机械加工中本身的价值并不高,但所起到的作用很重要,因为刀具是切削加工中最具有活力的因素。
除此之外,DR系列与其他刀具相比的一个显著区别在于DR系列并非焊接形式,而是纯硬质合金刀片式,刀片与刀体通过与类似于HSK刀柄的过定位形式紧紧连接在一起,然后用螺钉锁住,装夹显得简单且可靠。这种连接方式能确保刀片的重复定位精度控制在0.003mm以内,与此同时,因为是刀片与刀体是整个面接触,极大地提高了刚度,保证了扭矩的完美输出,确保刀具切削时非常稳定。由于高效率铰刀DR系列的整个系统是模块化的拼接,因此客户定制化的生产也不再是难事。目前DR系列已在很多领域被广泛应用,如连杆上的大小头孔,差速器壳体上的贯穿孔,摇臂轴孔等。
另外值得一提的是号恩产品中的以刮代磨-刮削系列。其创新点在于将传统车削刀具以点接触加工方式改变为面与面的接触式机加工新工艺。如此一来,加工时工件表面将没有任何刀痕,满足了特殊的表面要求,同时无需投入额外的磨床和设备,减少加工流程和操作强度,从而提高了生产效率。
高效成型技术在汽车零部件上的应用
近年来,汽车产业界最重要的一个课题是致力于减少环境的负担。但同时对安全性的要求也持续提高。最主要的对策之一是汽车轻量化,致使高强度钢的采用比率急速增加。其中一项主要的解决案例便是车辆骨骼部品的高张力材料化。虽然钢铁不是当今世界上最强壮的材料、但是从设计的多样化、成本的效率性、制造过程的低排放性、可回收二次利用性等特性来看,钢铁还是目前最好的汽车用材料。
而协易在对高强度钢等主要汽车用材料的加工上,可称得上是业界的行家。协易的技术主要针对两大方向,一是大型车身外钣件、高强度内钣件的加工(冲床及接口设备整合、金属成型TOTAL SOLUTION方案),二是动力总成关键零件的生产(液力变矩器、变速器齿型毂件、机油热交换器、同步器齿环等等)。
在钣金加工过程中,“生产效率”和“成形性”成为人们最关注的两大问题。研究发现,在常见的冲床设备中,曲轴冲床、连杆冲床这类冲床能对“生产效率”起到很大作用,但在成形性上有所欠缺;油压冲床则能更好成形,生产效率却不足。对此,伺服冲床取其之长,补其之短,在生产效率和成形性上完成了双管齐下。协易的伺服压力机采用了适应性很强的伺服驱动技术,将液压机的灵活性与机械压力机的高效率优点有效地结合起来,可以为用户提供大、小批量的不同冲压件。伺服压力机的转速变化及控制经过了合理的优化设计,因此有可能在冲压过程中实现冲压运动和冲裁力的无级调节。同时还使压力机的工作曲线与各种不同的应用要求相匹配。
现代化的冲压科技要求冲头(滑块)必须是能在任意位置停止、上升、下降、加速、减速等,才能成就最佳的成型工艺与生产目的。协易历经十多年的研发,并经严格的市场应用测试, 推出了高扭力低转速的直驱式(Direct Drive)伺服冲床。其原理是配备了低转速高扭拒的专用伺服马达和控制系统,转速仅有300 SPM,但扭拒可达到15,000 N-m(以200吨为例)。
随着生产规模化、车型批量小、品种变化快、多车型共线生产等特点的延伸普及,冲压技术与设备被要求不断向柔性化和自动化方向发展。协易在此基础上研发出了一套完整的柔性冲压自动线。一条柔性冲压自动线大多由一台多连杆拉伸压力机和3-4台压力机组成,生产大型车身覆盖件,从毛坯的上料到冲压件下线全部自动完成,整条冲压线长60-80m左右,生产节拍高达10件/min或更多。不仅如此,压力机的所有控制功均做到智能化,实现了高安全性和冲压质量。
典型缘条类零件的加工方法
结构整体化是新一代大型客机的发展趋势,已经成为现代先进大型飞机设计制造领域的一个重要标志,对研发周期、生产效率和制造成本等具有非常重要的影响。采用整体结构件的优势在于可以大幅降低连接装配工作量,减少零件数量,实现10-30%的减重,提高密封性能。目前,大型客机的带筋整体壁板、整体框和梁缘条等复杂形状结构件的加工均采用高速加工技术。
大型客机梁缘条类零件是典型的大型航空铝合金结构件,是飞机机翼、水平尾翼、垂直尾翼上的重要零件类型。其零件特点是:长度尺寸大,机翼缘条可达20m;具有明显的薄壁特征,壁厚与壁高比可达1:30;零件截面形状变化大,存在复杂曲面特征。
这些特点导致毛坯工件的材料去除量增大、余量不均匀、易在加工后产生零件变形,为制造工艺带来了巨大挑战。
对此,我们对装夹方式、加工变形控制及切削路径这三方面作出了优化和调整。
在装夹方式方面经过对比发现,立式装夹比卧式装夹在工装系统装卸效率、难易程度、柔性上更胜一筹。同时对加工路径具有更好的可控性,避免不必要的加工振动。仅仅是在毛坯材料的去除上效率略低于卧式装夹。
在加工变形控制策略上,我们采用加热成形代替冷成形,控制毛坯原始残余应力,合理引入负变形。
在切削路径优化上,对于缘条类零件,其主要加工特征为侧壁加工,径向切削力对加工变形的影响最大,刀具和工件的径向刚度对加工变形影响大,可采取的控制策略主要有:
1、采用分层环切的刀具路径,可以使零件在加工过程中局部保持高刚度。
2、合理选用加工方式。根据加工情况不同,采用逆铣方式可以避免让刀造成的加工误差;采用顺铣方式可以避免由于刀具和工件相互靠近造成的过切。在梁缘条加工过程中,粗加工过程主要混合使用两种加工方式,可以省去机床来回的空载时间,提高效率。精加工过程,当不影响变形时,使用顺铣进行加工,这样可以提高表面质量。
3、合理选择刀具参数。刀具圆角对切削力的分配具有重要的影响,在侧壁加工过程中,选用带有一定圆角的刀具,可以使加工过程中的径向力向轴向力转换。
对于第三点中的刀具参数,我们也作出了详细的分析。刀具材料、切削方式确定后,刀具切削部分的几何参数就成为影响刀具性能的主要因素,对切削变形、切削力、切削温度和刀具磨损等有着重要的影响。在铣削加工中刀具重要的几何参数有:刀具的前角、后角、螺旋角等。
析薄壁铝合金零件铣削加工变形控制
铝合金材料凭借其良好的机械性能,被广泛应用于航空领域。在民用航空领域,更是大量使用整体铣削铝合金件,代替钣金铆接零件,从而提高零件的比强度。这些零件具有薄壁、材料去除率大、造型复杂、曲面多、配合精度要求高等一系列特点。铝合金整体铣削薄壁零件的变形控制成了民航客机零件制造的主要难点。因此我们针对薄壁结构铝合金件的加工变形的原因和变形控制的方法进行了初步的探讨。
首先来分析一下零件变形的原因,主要受到切削力、切削热、夹具、残余应力这四大方面的影响。
切削力影响中,我们对侧面加工和底面加工进行了解析。通过计算分析,在加工侧壁过程中采用摆角补偿和刀具路径补偿可以较好减少由于让刀变形导致的零件筋板尺寸厚薄变化,但在实际操作中,结构的复杂导致计算异常困难,所以不推荐使用。因此需要考虑不同高度厚度比薄壁的加工策略。当高度厚度比值相对较大时,宜采取径向优先的轴向分层方法。如果比值很大,而筋板厚度又很小的时候,宜采用对称切削的方法或者台阶切削的方法,保留基部厚度来增强整个结构的加工刚性。同时,顺逆铣对侧壁加工也产生了一定影响。根据铣刀的旋转方向和切削进给方向之间的关系,可以分为顺铣和逆铣两种。当铣刀的旋转方向和工件进给方向相同时称之为顺铣,反之则为逆铣。顺铣时,切削厚度由大到小,切向力与零件进给方向相同,径向力为压力,加工效率高,刀具磨损小,零件表面的光洁度好。逆铣时,切削厚度由小到大,切向力与零件进给方向相反,有助于抵消丝杠间隙,径向力为拉力,会导致薄壁结构被拉动而造成尺寸偏小,在刀齿切削前,先在零件表面摩擦一段距离,造成表面光洁度差,刀具磨损严重。CNC机床的精密度较高,不考虑丝杠间隙问题,因此推荐使用顺铣。逆铣仅在粗加工或半精加工中为避免来回空刀而采用。
而对于底面加工,合理安排走刀路径及选择合适的工装显得至关重要。底面加工常常采取单向铣削和来回铣削两种走刀方式。来回铣削节省刀路,加工效率较高,但由于顺逆铣变化等等原因,常常在刀路与刀路之间存在着较大的差异,有时甚至会产生台阶差。单向铣削比较容易保证表面的光洁度,因此推荐粗加工时采用来回方法,而在精加工的时候使用单向铣削。对于某些薄壁的腹板结构,在加工时需采用真空平台吸附。值得注意的是在真空平台边缘区域易出现吸附力不够的情况,加工过程中零件底面振动或是被拉起,产生明显刀纹台阶甚至尺寸偏小的情况,在边缘区域应当增加抽气槽以加大吸附力。对于某些没有相应真空平台的薄壁零件,在加工时可以使用填充物来补充强度,此处需要注意的是填充物的膨胀和收缩也会导致零件的变形,因此若采用此类方法进行加工的时候应该注意时效。
声明:本网站所收集的部分公开资料来源于互联网,转载的目的在于传递更多信息及用于网络分享,并不代表本站赞同其观点和对其真实性负责,也不构成任何其他建议。本站部分作品是由网友自主投稿和发布、编辑整理上传,对此类作品本站仅提供交流平台,不为其版权负责。如果您发现网站上所用视频、图片、文字如涉及作品版权问题,请第一时间告知,我们将根据您提供的证明材料确认版权并按国家标准支付稿酬或立即删除内容,以保证您的权益!联系电话:010-58612588 或 Email:editor@mmsonline.com.cn。
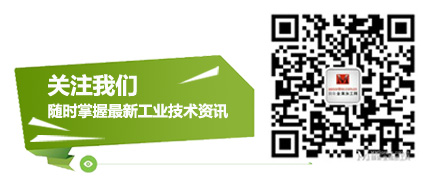
- 暂无反馈