库卡工业 - 破解动力电池模组和PACK线自动化组装
【编者按】动力电池模组的自动化程度要求一般都比较高。因为工艺的复杂程度、工作环境的要求等,应用机器人和专用设备的优势显而易见。
在政策和市场的双轮驱动下,2015年电动汽车将延续去年的火爆行情,对动力电池的需求也越来越旺盛。但需注意的是,动力电池生产企业订单增幅明显,可是产能的提升却相当有限。这主要因为当前的工艺流程和人工操作制约了企业的生产节拍和效率,从而无法有效提升产品质量和产能。提高动力电池模组组装的自动化水平迫在眉睫。
动力电池的自动化集成业务一般包含模组和PACK的全自动/ 半自动组装线、自动化设备集成、信息采集与传输(MES)、无人化车间软硬件管理系统。当前此市场的高端设备一般由德国美国和韩日提供,当然随着经验的增加和自动化集成能力的提升,国内的众多新型企业也有望在动力电池的自动化设备集成行业大展拳脚并占据一席之地。
一般而言,不管是软包电池、硬壳电池还是我们常见的18650圆柱电池。模组的自动化组装工艺流程都是从电芯上料开始的,这个来料可以是原供应商提供的包装,也可以是厂家经过检测后统一整理好的专用托盘;上料可以是人工操作,也可以通过传送带自动上料,然后通过机器人经由抓手抓取。
上料的同时会进行电芯的读码(采集单个电芯的身份数据信息)、电芯极性检测(有无放反方向)、电芯分选和电阻值(DCIR)检测,并将不良品剔除。来料通过初检和分选之后,根据模组和工艺要求的不同会分别进行诸如等离子清洁-涂胶-电芯堆叠-电池盒组装-极耳裁切整形-模组壳焊接-模组打码-打螺丝-模组检测-连接片焊接-BMS系统连接-模组终检测-模组下料等工序。
由于目前市场上各家汽车厂商的要求不同,所以几乎没有一家的模组和生产工艺是一样的,这也对自动化产线提出了更多的要求。好的自动化生产线除了满足以上硬件配置和工艺要求以外还需要重点关注兼容性和“整线节拍”。由于模组的不固定,所以来料的电芯、壳体、PCB板、连接片等都可能发生变化。生产线的兼容性就显得尤其重要。
目前比较常见的方式是采用机器人作业,因为6轴机器人的灵活性,更大的工作覆盖面除了提升工作节拍、减少空间以外最大的优势是可以灵活定制的机器人抓手,抓手采用中心定位方式,不管是抓取、真空吸、夹持等方式都比定制的工装板和夹具有了广泛的兼容性。
所谓“整线节拍”是指整条自动线平均到每个工作站的工作时间节拍而非传统意义上见到的流水线。上个工作站完成后传送到下个工作站,总有工作站是在等待的,这样就浪费了节拍和效率。
所以当前完善的模组自动化组装线针对每个工作站节拍的衔接,厂房空间的利用、布线的美观度、减少对物流通道的干涉等都是需要注重的细节,好的自动化生产线最核心的部分就在于整线的逻辑语言。毕竟所有的检测设备都是外购的标准品,很多专用设备也能在市场上买到。而将这些所有不同厂家不同品牌的专用设备集成在一条生产线上并统一做好信号传输和管理就体现了集成商的能力。
至于软硬件的搭配,MES系统的集成可以直接将生产线打造成准无人化的生产车间,人工只需要在线外进行物料的补充即可。提高了安全不说,也减少了人为因素对于产品和生产的干涉。从PACK的构成到模组的构成再到每一道工序的参数、电芯的数据、其他来料的信息等,都可以通过MES系统快速查询并得到信息,从而有效提成生产管理水平。
对于当前的动力电池行业来说,模组的自动化程度要求一般都比较高。因为工艺的复杂程度、工作环境的要求等,应用机器人和专用设备的优势显而易见。而PACK线一般指需要承担两个功能:传送和检测。目前各厂家普遍应用了半自动的PACK组装产线,主要用于PACK的上线、下线、检测、厂内传输和包装。
在这里面AGV小车、助力机械臂、滚筒线、吊臂等都是简单而有效的工具。而柔性的线路串接等工作确实离不开人工的协助,所以半自动的PACK成为了各厂家的主流配置。当然越来越多的客户会要求将PACK和模组的MES系统集成在一起,以便更好的管理和快速的查询,这对于系统集成商来说又是一个小小的挑战。
总之,随着动力电池自动化组装工艺的不断提升和专用设备的普及,动力电池企业对它的认知度也越来越高。去年国内多家企业已经配置了全自动的模组生产线,产能得到了明显的扩充且对生产品质非常满意,笔者相信越来越多的企业已经关注并期待着这样自动化的动力电池生产线。
声明:本网站所收集的部分公开资料来源于互联网,转载的目的在于传递更多信息及用于网络分享,并不代表本站赞同其观点和对其真实性负责,也不构成任何其他建议。本站部分作品是由网友自主投稿和发布、编辑整理上传,对此类作品本站仅提供交流平台,不为其版权负责。如果您发现网站上所用视频、图片、文字如涉及作品版权问题,请第一时间告知,我们将根据您提供的证明材料确认版权并按国家标准支付稿酬或立即删除内容,以保证您的权益!联系电话:010-58612588 或 Email:editor@mmsonline.com.cn。
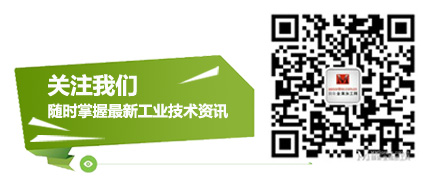
- 暂无反馈