2015年机器人行业七大国际巨头备战中国
2012年全球工业机器人本体市场容量约为530亿元,本体加集成市场容量按本体大约3倍算,估计约1600亿元。在全球工业机器人本体市场,机器人四大龙头企业:ABB、发那科(FANUC)、安川(YASKAWA)和库卡(KUKA)2012年收入占比超过50%,是这一领域的绝对强者。在工业机器人系统集成方面,除了机器人本体企业的集成业务,知名独立系统集成商还包括杜尔(DURR)、柯马(Comau)、徕斯(REIS)等。这些行业巨头的机器人相关业务收入都在百亿元以上。
2012年,全球服务机器人市场容量约为281亿元,其中个人(或家庭)用服务机器人市场容量约为73亿元,公共服务机器人市场容量约为208亿元。近年来,随着服务机器人产业化趋势显现,在服务机器人领域也有一系列企业涌现出来。这些企业包括研制达芬奇机器人的直觉外科机器人公司(INTUITIVE SURGICAL INC)、生产吸尘器机器人的IROBOT以及兼并重组多家机器人公司的谷歌(GOOGLE)。
机器人巨头们的前世今生
国外重点工业机器人企业最初起源于机器人产业链上下游相关企业,如下游应用的焊接设备、上游的数控系统生产等。
ABB:电气化时代的开拓者,涉足机器人领域具备电气技术优势。
ABB的前身是瑞典的ASEA公司,它是瑞典一家电气设备领域的设备供应商,1961年,ASEA建立了电子事业部,标志着公司从强电设备制造商转型为电气和电子公司,强电、弱电得到了平衡发展。1974年,阿西亚发明并推出工业机器人,1980年巴内维克出任ASEA执行董事兼CEO,在他的带领下,公司注重向高技术拓展,在机器人和电子工业领域加大投入,尽管机器人开发成本高昂,以至于影响了公司整体利润,但巴内维克坚定看好机器人的发展前景,1988年ASEA与瑞士BBC合并成立ABB,机器人业务仍得到重点发展,造就了今天公司在机器人领域强大地位。1974年,ABB推出第一台全电动机器人IRB6。如今,ABB已在全球范围内安装了20多万台工业机器人,拥有近30种型号的机器人,可广泛满足各行各业的生产需求,并具有强大的系统集成能力及遍布53个国家的全球销售服务网络提供全方位支持,帮助客户提高生产效率、改善产品质量、提升安全水平。
库卡:从焊机系统提供商延伸到机器人领域
1905年,早期的库卡从照明领域扩展到焊接设备领域,1956年为冰箱以及洗衣机生产开发制造了第一台自动化焊接机,同时向大众汽车股份公司供应了第一台多点焊接线,1971年首次交付用于奔驰汽车生产的机器人焊接传输系统;1973年,第一台库卡机器人“Famulus”问世使库卡成功进入机器人生产领域,这是世界首个电机驱动的六轴机器人;现今库卡专注于向工业生产过程提供先进的自动化解决方案。
发那科:以机器人控制系统,驱动系统为切入点
发那科于1956年从富士通数控部门独立出来,起初专注于机床加工控制系统的研发和生产。上世纪70年代,发那科成为全球最大专业数控系统生产厂家,占据了全球70%的市场份额。此外,公司在驱动方面也很有建树,1959年研制成功电液步进电机,后引进美国Gette公司直流伺服电机制造技术,提升驱动开发能力。基于伺服、数控基础,1974年发那科首台工业机器人问世,1976年投放市场。此后公司一直致力于机器人技术上的领先与创新,是世界上唯一由机器人来做机器人的公司,是世界上唯一提供集成视觉系统的机器人企业,是世界上唯一既提供智能机器人又提供智能机器的公司。截至2013年,累计出厂的台数已突破28万台,位居全球首位。
安川电机:伺服、变频器起家,奠定工业机器人制造基础
安川电机是以伺服、变频器起家,其运动控制技术在业内领先,公司自1915年成立以来,一直致力于以马达技术为核心的产业用电机产品的制造与开发,1958年,安川电机开发出的Minertia电机改写了电机的历史,开拓了超高速、超精密的运动控制领域。1977年,安川运用独自的运动控制技术开发出日本首台全电气式产业用机器人“MOTOMAN”,之后相继开发了焊接、装配、喷涂、搬运等各种各样的自动化作业机器人。
杜尔公司:汽车领域发展起来的成套设备提供商
1895年,保罗杜尔在斯图加特建立了第一个专门为屋顶防雨的金属商店。1978年杜尔进入了自动输入系统领域,这是杜尔成为系统供应商的重要一步。1999年杜尔引入Ecopaint涂装机器人。同年,杜尔收购了法国的竞争对手阿尔斯通自动化。2000年,杜尔集团收购了测量系统集团申克。随着申克的加入,杜尔使自己成为机车最终装配更为全面的设备供应商,并且在平衡和诊断设备方面保持世界领先地位。
谷歌:令人瞩目的机器人“新贵”
谷歌近期收购了在人工智能、机器人、机械手臂、设计等领域有所专长的八家机器人公司。谷歌此次收购更注重机器人的软件方面,因为谷歌认为机器人项目还需要在软件和传感器等方面取得突破,而硬件层面的问题,比如机动性、手和脚的动作,都已经获得解决。
在完成对一系列机器人公司的收购后,谷歌斥资32亿美元收购NEST和约4亿美元收购了人工智能公司DeepMind。根据谷歌的发展战略,机器人技术将在谷歌下个十年的发展中扮演重要的角色,它们将在空间探索、地图数据收集、制造业等多个方面发挥巨大的作用。未来谷歌计划在家庭自动化、制造业自动化以及商业物流自动化等方面实现重大突破。
直觉外科公司(ISRG):医疗机器人的成功典范
直觉外科公司于1995年成立,2000年上市,2004年开始盈利。ISRG与IBM、麻省理工学院和Heartport公司联手开发的外科手术机器人——达芬奇机器人(由三部分组成:外科医生控制台、床旁机械臂系统、成像系统),让医生坐在类似于电子游戏机的控制台前,通过四个机器手来操纵病人体内的观察仪和手术工具,进行微创手术。
ISRG在机器人手术领域拥有近乎垄断的地位,业务是基于“剃须刀与刀片”商业模式,一半以上的营收来自经常性的配件销售和服务合同。截至2013年9月30日,全球范围内共安装2871台达芬奇手术机器人系统。
在工业机器人领域,最终上规模的企业大都以本体业务为核心,还有做集成业务甚至也做核心零部件业务的综合型机器人企业。工业机器人巨头大都在上世纪70年代进入机器人领域,经过40年的发展,有些成为纯粹的机器人企业,有些则以机器人作为集团公司的业务之一。从业务角度看,全球四大机器人企业不但拥有机器人本体业务,同时也涉及集成、关键零部件业务,更关键的是都具备底层软件设计能力。当然也有专注于集成业务的大企业,它们一般都与汽车大厂商有深度合作。
机器人巨擘的竞争优势
从1954年美国人德沃尔制造出世界上第一台可编程的机器人算起,世界机器人发展历史已经60年了。对全球机器人技术的发展影响最大的是欧美和日本,以库卡、发那科、ABB、安川电机等为代表的行业巨头们在工业机器人技术的综合研究水平上处于领先地位。这些国外企业由于起步早,产业已形成规模化优势,在研发设计、核心零部件等领域形成了标准化流程,具有较强的领先优势。相比较而言,我国机器人产业的发展历史短得多,虽然曾在上世纪80年代掀起过一次机器人发展高潮,国家设立了专项予以支持,技术上取得了不少成绩,由于当时发展环境、市场需求等原因,没有实现真正意义上的产业化,与发达国家相比,我国机器人领域的技术仍处于落后的状态。
分析机器人巨头们的发展历史,不难发现,巨头们在竞争中占据了很大优势:
品牌优势。国外机器人巨头在机器人领域一般都拥有三十多年的发展历史,在长期运营的过程中,在用户中建立了产品的权威性、专业性和优越性。如谈到汽车涂装生产线集成,大家首先想到的必是杜尔;说到工厂自动化、机器人制造机器人的话题,发那科不可能被忽视;大众汽车会用哪家的机器人,库卡定是首选。
应用层功能的积累。国外机器人巨头在数十年的发展中,在各自的专业领域里积累了详尽的行业应用经验。通过与客户长期合作,他们对于用户行业制造过程的工艺有很深刻的理解,甚至于该工艺的标准流程和规范都由他们来制定。他们在此基础上开发出专业的机器人工艺模块。
成本优势。机器人巨头的机器人本体的年产量一般都在5000台以上,有的甚至在10000台以上。他们在关键零部件采购上具有很强的议价能力,从而使得机器人本体也具有很强的成本优势。发那科、安川电机等企业自己开发应用控制器、伺服电机等关键零部件,其机器人本体的价格优势更为明显。
本体的可靠性。以平均无故障时间(MTBF)计算,国内机器人产品平均在8000小时,而国外同类产品可达数万小时。可靠的稳定性成企业选择国外品牌的主要原因。
在机器人众巨头中,ABB最为突出的优势是集团优势,拥有强大的系统集成能力。ABB可以凭借在电气、自动化和系统领域的技术优势提供完整的解决方案。同时,遍布全球的销售和服务网络,为ABB带来了更多的潜在客户。
如果说智能机器(包括小型加工中心、电火花线切割机、全自动注塑机)、机器人、CNC数控系统是自动化工厂的三个标志性要素,那么能够同时提供三者的发那科公司毋庸置疑就是自动化工厂的最佳诠释者和全部解决方案的供应商。其自主研发的CNC(数控部分及马达)产品是发那科最大的优势。
安川电机是典型的综合型机器人企业,其业务优势是各个业务部门之间可以相互配合。安川电机的MOTOMAN工业机器人是世界上使用最广泛的工业机器人之一。
库卡是世界领先的德国机器人制造商,在2007年进行了业务重组,重组后库卡的业务部分为机器人部和系统集成部,是“最纯粹”的机器人企业。
杜尔是专业的系统集成企业,机器人本体数量很少,在涂装生产线集成方面具有明显的优势。
国外机器人厂商抢滩中国市场
中国市场是未来全球最大的机器人市场,近年来增长迅猛。国际机器人巨头纷纷抢滩中国市场,以ABB、库卡、安川电机、发那科四大家族为代表的国外机器人企业占据了中国机器人市场90%以上的市场份额。
在90%的机器人市场份额中,ABB、发那科、安川机电、库卡四大家族共占57.5%。其后的三大厂商OTC、松下和川崎重工共占16%。而国内机器人生产企业市场份额相对较小,2012年本土品牌机器人市场占有率8%,企业普遍存在规模较小、创新能力薄弱等问题。
这种竞争格局和国内机器人大部分用于汽车行业有关,而国外机器人厂商通常与大的汽车企业绑定。例如,大众只用库卡的,经常一家新工厂购买库卡1000-2000台机器人,通用主要用发那科的,欧系汽车品牌则更多考虑ABB。国内汽车企业也各有偏好,比如长城用安川的莫托曼,江淮汽车用ABB的。国内机器人企业在汽车行业竞争不过国外产品,国外机器人企业在汽车行业的优势源于国外仍保留的汽车制造业,尽管其他制造业产能大都转移到了中国。
机器人本体最好的还是欧洲的产品,以库卡最为顶级,ABB机器人国产化之后,质量有所下降。日本的安川、发那科、松下等,与欧美产品相比较,属于质优价廉型,更加符合中国客户需求。韩国现代机器人,主要用于现代集团内部的现代重工和现代汽车,外销相对少一些。
安川和发那科等日本机器人企业对中国市场非常重视。以安川为例,最开始和首钢合作机器人本体,近期又与杭州凯尔达合作机器人本体。而且这几年安川在国内市场布局做得非常好,几乎每个重要市场都有办事处。如果未来国内没有企业能做好本体,估计国内机器人市场主要由日本企业占据大部分份额。
机器人四大家族都非常重视中国市场,纷纷在中国投资建厂,但是真正意义上研发和生产都实现本土化的只有ABB。国外机器人企业在抢占中国市场的同时,为国内机器人行业培养了人才,建立了较为完善的供应商体系。
ABB机器人业务于1994年进入中国。2005年,ABB将一条机器人生产线从欧洲转移到中国上海,开始了机器人的本地化生产。2006年,ABB全球机器人业务总部从美国底特律迁至上海。2009年,投资1.5亿美元的ABB机器人总部新址落户上海康桥工业园区。2011年,ABB携手厦门思尔特机器人系统有限公司在成都共同建成西部第一个机器人系统集成基地。ABB成为国内唯一真正实现工业机器人在研发、生产、销售、工程和服务全价值链上本土化的跨国企业。2013年9月,ABB在国内生产的第2万台机器人下线。
1992年,北京发那科机电有限公司成立,由北京机床研究所与日本FANUC公司共同组建,主要负责CNC产品在中国市场的业务。1997年,上海电气实业公司与日本FANUC株式会社联合组建上海发那科机器人有限公司,这是最早进入中国推广机器人技术的跨国公司。2010年,发那科上海宝山顾村工业园新工厂落成,不但有全新的机器人系统工厂、各类实验室、培训教育设施和技术服务机构,还将成立机器人应用技术研究所,全面提升服务能力。2012年,上海发那科启动了位于上海宝山区的二期工程,用来增加系统集成能力。
1996年,中国首钢总公司和日本株式会社安川电机共同投资成立安川首钢机器人有限公司,专业从事工业机器人及其自动化生产线设计、制造、安装、调试及销售。1999年,在上海成立安川电机(中国)有限公司,主要经营安川品牌的变频器、伺服电机、控制器、机器人、各类系统工程设备、附件等机电一体化产品。2011年,安川在中国上海嘉定区设立机器人系统的新工厂,进行机器人组装生产,主要向周边汽车生产企业供货。2013年6月,安川电机在中国江苏省常州市建设的大型机器人生产工厂开业。为了防止技术流出,技术含量较高的医疗等行业的机器人的研发、生产将继续在北九州市开展。
1986年,库卡机器人进入中国。当时,库卡公司将一台机器人产品赠送给了一汽卡车作为试用品,这台机器人也成为了中国汽车工业应用的第一台工业机器人。1994年之后,库卡机器人开始大批量进入中国市场。2000年,库卡机器人(上海)有限公司成立。2014年3月,库卡机器人在上海松江举行新厂开幕典礼,成为德国库卡集团全球第二个总部。新厂每年可生产5000台机器人。在立足高端市场的前提下,库卡不断提高机器人产品在中国市场的占有率和品牌知名度。在一般工业应用领域,库卡有意逐渐淡化作为后来者和高端供应商的定位,并正在得到越来越多中国客户的认可。
中国企业的追赶之道
我国机器人产业应用范围广、市场空间大。从需求结构来看,目前我国汽车、电子产业对机器人需求占制造业市场需求的一半左右。随着我国工业机器人技术的发展与成熟,配合我国经济结构的调整,应用领域将逐步由汽车、电子产业向化工、食品、医药、家电、物流等领域扩展与深入。我国工业机器人应用将在改造劳动密集型产业、替代简单重复劳动、促进产业转型升级等领域出现爆发性增长。例如某机器人公司针对我国日产量30万块标砖的企业需求,开发了搬砖机器人,替代工人简单重复但是费力的搬运、码垛工作,使企业实现生产自动化,提高生产效率,仅此种机器人的年销量就达几百台。因此,我国机器人市场不仅需要应用于汽车、电子等领域的六轴高档机器人,还需要大量三轴、四轴中低档机器人,代替人做大量简单重复、高强度、基于恶劣环境的工作,此类机器人在我国同样具有广阔的市场空间。
工业和信息化部2014年初发布的《关于推进工业机器人产业发展的指导意见》提出,我国工业机器人产业的发展目标是:开发满足用户需求的工业机器人系统集成技术、主机设计技术及关键零部件制造技术,突破一批核心技术和关键零部件,提升量大面广主流产品的可靠性和稳定性指标,在重要工业制造领域推进工业机器人的规模化示范应用。由此,首先要围绕市场需求,突破核心技术。选择汽车、电子、船舶、民爆、国防军工等重点领域,根据用户需求,开展机器人系统集成、设计、制造、试验检测等核心技术研究,攻克伺服电机、精密减速器、伺服驱动器、末端执行器、传感器等关键零部件技术并形成生产力。与此同时,我们还应该把握发展机遇,在家电、陶瓷,石化、食品、饲料、医药等传统行业寻找更多机会,发掘并创造客户需求,先在低端产品方面突破,以此推动规模化应用,积累经验后再向高端市场发力。
当前,我国机器人产业正处于起步发展阶段、产业基础低、市场大,未来的产业化进程可借鉴国外的成功经验,较可行的是由系统集成模式,向分工合作模式发展。
第一,从集成入手,寻求突破。由于受核心技术限制等多方面因素影响,我国工业机器人产业目前获得突破的主要为系统集成领域。国内一些领先企业从集成应用开始,主要借助对国内市场需求、服务等优势,逐渐脱颖而出,取得了不错的市场成绩。优先发展系统集成领域,是国内机器人产业在现实情况下的被动选择。
第二,发展经济型机器人本体。现阶段国内机器人厂商在高端领域不能直接与国外企业竞争,国内机器人的成功之道在于打通上下游产业链,生产经济型机器人本体,尤其要突破减速机等关键零部件。经济型本体是国产机器人本体现阶段发展方向,国内企业应侧重开发应用于汽车产业以外一般制造业的经济型机器人,包括低成本的六轴通用机器人和三、四轴专用机器人。
第三,着力产业化能力提升。促进功能部件的标准化和模块组合化是机器人产业化发展的一大趋势,一方面可以降低机器人成本并推动其产业化发展;另一方面可促进机器人关键技术发展与产品成熟,提高产品可靠性。
第四,据世界机器人联合会的估算,软件集成、周边设备、系统工程等系统集成业务的收入约为单机的3倍。虽然在单机制造上成本优势不明显,但由于拥有一批成本相对较低的本土工程师针对不同项目需求进行非标设计、后期维护成本和周边设备采购成本也相对较低,本土机器人品牌承接机器人系统集成的综合成本优势显著(较外资约低30%)。通过承接系统集成项目突破高端客户、最终实现全系列产品渗透是本土品牌切实可行的策略。
第五,立足国内劳动密集型产业,挺进技术密集型产业。对于高端汽车、电子、生物等技术密集型产业,国内本土机器人生产企业面对国际品牌厂商咄咄逼人的竞争态势,在关键零部件受制于人的背景下,短期形成较大的价格竞争优势比较困难。相反,在国际品牌企业关注度稍弱的部分传统劳动密集型制造业中寻求规模突破的机会反而更大。针对客户需求开发机器人化的生产系统至关重要(产品的标准化和批量化取得较好平衡的领域,在机器人的选择上非六维度也是可以考虑重点)。利用国内广大劳动密集型企业面临调整、升级的时机,发现、挖掘机器人生产线改造机遇,集中做好工程、设计工作,引导需求加快释放节奏。在此基础上,部分本土机器人生产商由专业领域逐步进入通用机器人领域,具备更强的规模效应基础。
声明:本网站所收集的部分公开资料来源于互联网,转载的目的在于传递更多信息及用于网络分享,并不代表本站赞同其观点和对其真实性负责,也不构成任何其他建议。本站部分作品是由网友自主投稿和发布、编辑整理上传,对此类作品本站仅提供交流平台,不为其版权负责。如果您发现网站上所用视频、图片、文字如涉及作品版权问题,请第一时间告知,我们将根据您提供的证明材料确认版权并按国家标准支付稿酬或立即删除内容,以保证您的权益!联系电话:010-58612588 或 Email:editor@mmsonline.com.cn。
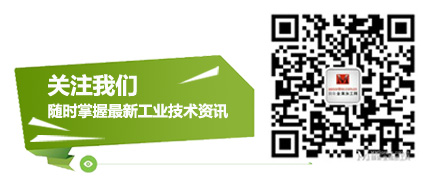
- 暂无反馈