机匣内间断形深孔机械加工研究
某新型发动机结构新颖,主机匣分左右安装,其内部关键件凸轮轴的安装孔属于一种特殊深孔形式,通过优化方案自主设计了一套用于深孔加工的刀具方案,通过试制完成了首件的加工,为系列化研制该类机型积累了加工经验。
前言
某型发动机是我国水平对置式发动机的首次研制类型,比早期的发动机更容易实现系列化、标准化发展,有极大的市场前景。该发动机的左、右机匣是发动机的主体,由铝合金铸造后经机加而成。
机匣结构复杂,外形为非规则的壳体件,拥有特殊的散热片,难以按回转件的方式实现高精度内孔加工,尤其多个安装孔的长径比都大于20,属于深孔加工,用以往的镗削加工无法达到要求,是机型试制中亟待解决加工问题。
1 零件的工艺特点及难点分析
该机型研制周期短,机匣中凸轮轴安装孔的尺寸位置精度高,若采用外购刀具其采购周期约为三个月,研制周期太长,成本也偏高。试制中必须结合工厂自身的刀具制造能力自行拟定工艺方案和刀具设计,完成关键工序的加工。
1.1 机匣件的结构特点
发动机凸轮轴安装孔结构如图1 所示,型面分为4 段,深度最大处574 毫米,各间段上的孔尺寸精度相同均为φ26.2+0.038+0.01 毫米,孔的圆柱度不大于0.025mm,相对于三个基准要素的的位置度要求为φ0.05 毫米。零件材料为ZL105,为可热处理强化的铝-硅-铜-镁系铸造合金,具有良好的铸造工艺性能和较高的气密性,属中等热强铝合金,其高温力学性能和切削加工性能均优于ZL101、ZL104等铸造合金。
1.2 工艺分析
在航空发动机零件制造中深孔钻削被广泛使用,为得到稳定的加工质量,工厂已配备有多种深孔机床和刀具实现枪钻、BAT 深孔钻、喷射钻等等工艺方法,但凸轮轴的安装孔直径大小和零件结构的非封闭不便于厂内专用深孔钻床上采用带内或外排屑的钻、镗工艺,同时零件结构的间断性使刀具的切削要形成多次切入和切出,常规深孔刀具的加工过程不稳定,各种精度难以保证。因此决定在镗床或加工中心上另行制定一套切实可行的加工方案,由夹具对零件进行精确定位,刀具旋转进给完成加工。
最后选定的设备为DIXI 公司的DHP80 数控卧式四轴加工中心,水平工作台尺寸 800×800mm,线性轴X/Y/Z 的工作行程分别为200mm/1100mm/1100mm,X、Y、Z 轴的定位精度≤0.005mm,主轴转速可达12000rpm,主轴锥孔采用ISO50标准,冷却液流量50L/ min,最大刀具长度大于600 min,完全可满足该零件的加工。
左、右机匣最终是通过定位销和螺纹实现对半联结,两边机匣的凸轮轴安装孔都是不完整的孔,在完成组合加工孔后,左、右机匣还要拆开进行其他工序加工。在进行孔加工前可以不再依循传统的孔粗加工方法,试制中以精密螺栓安装孔和曲轴支靠面为定位基准,分别对左、右机匣凸轮轴安装孔进行两道铣削加工,底孔的直线度、位置度比钻削更好,有利于精加工刀具的最终加工质量。
1.3 刀具方案分析
汽车变速箱排挡孔的结构有类似该机匣之处,变速箱为非完全封闭箱体,虽然内孔也存在间断,各型面孔之间仍然能安排刀具的引导装置,减少刀具的振动,这样可以弥补扩孔、铰孔对前工序位置度校正能力弱的缺点。但左、右机匣在粗加工后再次用定位销和螺纹组合一起,各段孔型面之间无法安置刀具引导,在这种情况下刀具的多次切入切出、刀具外径的跳动都会破坏零件孔的精度,如何有效的去除扩孔余量、保证刀具的刚性实现精加工是保证工艺要求的关键,专用刀具是保证该工艺方案的主要手段。
2 工艺加工方案选择及刀具设计
2.1整体解决方案
结合以往各种加工方法的优点采取镗削和铰削相结合的方法加工左、右机匣,由于左、右机匣之间有定位误差、加工精度和组合精度的影响,粗加工孔后留下的余量有不均匀情况,必须安排一道镗削工序来校正被加工孔的位置度,为铰削留下均匀的余量。凸轮轴安装孔尺寸精度为IT7,表面粗糙度为Ra0.8微米,铰削完全可以满足加工要求。
具体工艺安排如下,首先用进口的通用精密微调镗刀加工第一段的型面孔,调整加工孔的尺寸到设置值,精确地保证孔径的精度和较细的表面粗糙度。然后用专用镗刀镗余下的三段型面孔,最后由专用铰刀完成凸轮轴孔的精加工。精加工时,为提高刀具安装的准确性,我们要求刀具每次加工前进行跳动检查;为消除切削过程中的振动,我们将孔壁端面有缺口或交叉的部位补齐,使镗孔时受力平衡。
2.2镗刀的结构设计
2.2.1 主切削刃
依据ZL105的切削加工经验,刀片材质选择YG8硬质合金进行焊接,主切削刃的前角沿刀具的径向,在切削过程中切削力主要是轴向力,径向分力较小,这样可以有效的减小刀具的挠度。前角可以使切削轻松,大小值根据工件材料和加工要求取12°。后角根据加工材料和进给量的大小选择,取12o,如图二。
内孔镗刀对断屑的要求较高,必须成“C”状切屑或扇形切屑,以减少容屑系数,便于排屑,根据试验数据可以确定断屑台的尺寸。镗刀刀头部分尺寸选取为直径25.9毫米,制造公差为+0.01毫米。
2.2.2 副切削刃
副切削刃对被加工孔有修光作用,所以直接影响加工质量。该零件加工时,副切削刃配合导向块对零件孔壁有挤光作用,为避免震动引起的刀痕,给副后刀面留有圆柱刃和0.02:1 的倒锥。
2.2.3 引导部分的结构
由于深孔长径比大于20,在刀头部分设置了导向块,主要作用是引导、支撑、挤压和防止由于悬臂过长产生震动,但现有资料一致认为,在图二右边所示受F2 力的导向块为主导向块,主要起承受切削力的作用;而受F1 力的导向块为副导向块,主要是决定孔径尺寸精度。应特别注意,绝不允许导向块参加切削,导向块要比刀尖在镗刀轴向方向低0.5~1 毫米。
2.2.4 柄部结构
卧式加工中心的刀柄、转接座都有自身的标准模块,若使用通用刀座进行转接刀具,镗刀的制造工艺性好,但刀具安装在机床上刀尖跳动很难控制在0.01~0.02 以内。所以采用刀身与刀柄用圆柱定位的螺纹联结,整体精磨制造,减小转接引起的误差。刀柄选择和机床主轴直接配合的ISO50 柄,由于刀具截面变化过大,刀具毛坯采用了锻造工艺。镗刀的整体设计和加工状态见图三。
2.3.铰刀的结构设计
2.3.1 刃口几何角度
在铰刀切削部分每个刀齿上具有负刃倾角,迫使切屑从孔前方排出,不致擦伤孔的已加工表面。铰刀刀齿具有双重后角的后面与带负刃倾角的前刀面相交而形成主切削刃。铰刀磨钝后,仅需刃磨刀齿的刃倾角前面,而不会影响铰刀的直径尺寸和圆柱刃带的宽度。铰刀修磨简便,重磨次数多,使用寿命长。为该零件设计的专用铰刀选择了10°的左旋刃倾角。
2.3.2 外径公差带的确定
铰刀完成最后的精加工,刀头直径尺寸取φ26.2+0.028
+0.02 毫米,由于刃倾角铰刀自然形成较小的切削锥角,所以加工时很平稳,另外铰刀的圆柱刃带较大,对孔壁有碾平和挤压作用,使孔壁产生弹性变形,铰刀走过后,孔壁具有恢复现象,所以开有刃倾角的铰刀最大极限尺寸较普通铰刀尽量大些。但该工序的已加工孔要与刀具的后引导配合,零件材料为轻合金,所以将铰刀最大极限尺寸确定在零件公差的三分之二处。铰刀公差取零件公差的百分之三十。
2.3.3 引导部分与柄部
由于刀具悬臂过长,成为影响孔加工质量的主要因素,设计专用铰刀时整体引导就非常必要。测得刀头的实际尺寸之后,减少0.005~0.008 毫米,在杆部铣削出四个螺旋状平面减小与零件孔的接触面,并形成引导面。
整个刀杆的中心部分是切削液的流道,使切削液能够到达切削区域,保证在间断结构的孔加工中前端切削部位有充足的冷却润滑,并使得导向部分与工件孔壁间产生润滑,防止干摩擦。
铰刀柄部采用与上述镗刀一致的结构,在满足刀具要求的同时制造精度也较容易达到,铰刀整体设计图五。
3 结束语
根据原有深孔加工刀具的设计经验,再结合自身成熟的刀具制造能力,融汇在该刀具的设计方案中,丰富了设计经验。加工中刀具切削轻快,零件的实测尺寸、孔壁粗糙度达到工艺要求,使该机型的试制工作顺利完成,为今后的系列设计提供了实践支持。
声明:本网站所收集的部分公开资料来源于互联网,转载的目的在于传递更多信息及用于网络分享,并不代表本站赞同其观点和对其真实性负责,也不构成任何其他建议。本站部分作品是由网友自主投稿和发布、编辑整理上传,对此类作品本站仅提供交流平台,不为其版权负责。如果您发现网站上所用视频、图片、文字如涉及作品版权问题,请第一时间告知,我们将根据您提供的证明材料确认版权并按国家标准支付稿酬或立即删除内容,以保证您的权益!联系电话:010-58612588 或 Email:editor@mmsonline.com.cn。
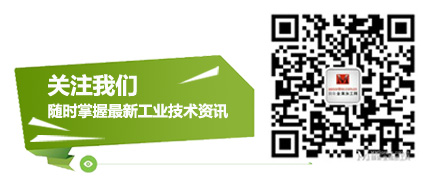
- 暂无反馈