精密刀具夹套优化轮胎模具生产
【编者按】轮胎模具可以与许多航空航天工业的高端元件一样复杂。工程师们正在不断地开发和创新各种复杂多变和不同类型的轮胎花纹图形,特别是轮胎侧壁周围的那些图形,它向Northeast Tire Mold公司这样的模具加工车间发起了强有力的加工挑战。坐落在俄亥俄州Akron镇的轮胎模具加工车间,采用直接加工的方法对其原材料实心模块进行加工,而不是通过铸件进行生产。每套模具都由几个直接加工的独立扇形模块组成,通常由8个扇形模块组成,然后将它们组合在一起,构成一整套圆形的模具。
所面临的挑战
其所面临的加工挑战是:每个扇形模块围绕着一套模具的整个圆周形状并按照一定的节距排列,最高可有12个不同的节距。如果花纹图形不够复杂,那么必须采用同样的节距对它们进行加工,一个模块与下一个模块之间必须相互匹配,并需将它们之间的热膨胀因素考虑在内,因为在模压成型过程中会发生热膨胀的情况。此外,在一套直接加工的模具中,基本上并不存在真正的平面,为了解决这个问题,Northeast Tire Mold公司必须保持严格的加工公差尺寸,使其模具所生产的轮胎整体指示误差(TIR)不超过0.005in(1in=25.4mm,下同),这意味着该车间必须使其单独加工的模块公差保持在±0.001in,从而使整套模具的公差尺寸保持在0.003in以下。
刀具夹紧解决方案
早在20世纪60年代,就开始采用直接加工工艺来生产模具,但这种工艺很费时,而且生产成本很高。然而,在采用先进的5轴加工方法和开发相关的软件之后,其加工速度和成本效益大幅度提高。现在,轮胎模具的直接加工必须采用具有高速5轴联动加工能力的机床和相应的配套软件。然而,Northeast Tire Mold公司发现,轮胎模具的5轴直接加工还需要采用具有良好刚性、可靠性和高精度的刀具夹套,以便使该车间的两台5轴加工机床能够以全速和全部进给能力运行,优化模具的生产。
在购置其第一台5轴加工机床前,Northeast Tire Mold公司选用了来自REGO-FIX公司的powRgrip刀具夹紧系统。现在,该车间已拥有一套powRgrip刀具夹紧系统、一套REGO-FIX公司的刀具平衡系统以及约200个powRgrip刀具夹套,其中包括夹头和圆柱形刀柄,它可使刀具延伸长度达11.8in(图1)。
图1 Northeast Tire Mold公司的REGO-FIX powRgrip刀具夹套系统、刀具平衡系统和大约200个powRgrip刀具夹套,对该车间轮胎模具的直接加工是非常关键的
不像其他的夹紧系统那样,通常采用热膨胀或液压方法来扩张材料,powRgrip夹紧系统采用夹套材料的机械性能,生成巨大的夹紧力,使刀具的跳动误差小于0.0001in。该系统的设计易于操作和使用,可以让Northeast Tire Mold公司在不到10s的时间内完成在夹套上的刀具装卸。由于其不涉及到刀具的加热问题,因此刀具更换后可立即使用。
刀具夹套为Northeast Tire Mold公司提供了强大、精确和平衡的刀具夹紧力,刀具的跳动误差很低,同时提高了刀具的使用寿命和产品的表面光洁度。此外,从其5轴加工操作考虑,按照Northeast Tire Mold公司副总裁Mike Christie先生的说法,采用powRgrip刀具夹套要比该车间以前曾一度使用过的热套型刀具夹套具有更多的优点。
“powRgrip夹头和刀具夹套可延续使用更长的时间。6年来,我们一直在使用我们的REGO-FIX夹头,现在看起来仍然像全新的。在同一段时间中,如果我们还仍然在使用热套型夹套的话,那么我们早已不得不更换刀具夹套了。”Christie先生说,“与热套型刀具夹套相比,采用powRgrip刀具夹套系统的刀具更换速度更快。此外,与热套型刀具夹套相比,该系统可容纳更小尺寸的刀具,从而减少了我们的刀具库存量,因为一个刀具夹套可以适用于一系列不同尺寸的刀具,相反,采用热套型夹套时,每一种尺寸的刀具都需要采用一个刀具夹套。”
对于轮胎模具的加工,Christie先生说,由powRgrip夹套提供的极低TIR整体指示误差是非常重要的,因为该车间使用了非常小的刀具,其长度相当于刀具直径的15倍(图2)。举例来说,直径为0.027in的双排屑槽立铣刀经常被用于加工铝制轮胎模具,其加工深度达0.190in,而该立铣刀的长度相当于其直径的15倍。对于这样的一种操作,刀具的跳动误差很低,这意味着其加工更为精确,但最重要的是,可延长刀具的使用寿命,按照Christie先生的说法,在这种情况下,刀具的使用寿命约达1400min,如果采用以前的热套型刀具夹套,刀具的使用寿命只能延续几百分钟的时间。
图2 REGO-FIX powRgrip刀具夹套为Northeast Tire Mold公司提供了极低的TIR整体指示误差,这对该车间使用极小的刀具是非常重要的,这种刀具的长度相当于刀具直径的15倍
实际使用中的刀具夹套
Northeast Tire Mold公司每年约制造250套模具,用于直径6ft(1ft=0.305m)以下各种规格的轮胎生产,其中包括ATV车辆和摩托车到轿车和轻型卡车的轮胎。大多数模具由1020号工具钢或6061号铝合金制成,每一个模具块的加工时间3~16h不等,根据花纹图案的复杂程度而定。
该车间内的两台Alzmetall 5轴机床按照24/7工作制日夜运行,有一名编程员负责编程,使用Openmind软件。每台机床配有一套可储存60把刀具的刀库,每一个工件的加工,平均使用40把刀具。其中一些刀具是备用刀具,因为该车间知道某些刀具究竟能使用多长时间,以满足刀具更换所需,使机床保持连续运行的工作状态。
其所使用的全部硬质合金刀具都安装在EGO-FIX刀具夹套之中,这两台5轴加工机床每台主轴驱动功率为30马力,在切削加工模具块时,主轴转速为24000r/min,进给速度高达315in/min(图3)。每次加工一个模块,只在两台机床上调试装卡,首先加工模块的后面,然后零件自动翻转,再加工模块的前面。
图3 Northeast Tire Mold公司采用直接加工法生产铝制轮胎模块,加工时的主轴转速为24000r/min,进给速度高达315in/min,所使用的刀具直径小至0.027in,夹持于REGO-FIX精密刀具夹套之中
Northeast Tire Mold公司的钢制模块采用干式加工法,而铝制模块采用REGO-FIX供给冷却液夹头的湿式加工法。Christie先生指出,很多车间内的小型刀具并非通过冷却液加工,而REGO-FIX夹头带有三条沟槽,冷却液直接从刀具上通过,用于润滑刀具和清除可能引起刀具断裂的切屑。
该车间的模具加工策略是:在粗加工走刀过程中,尽快和尽可能多地切除工件裕量,然后进行精加工操作。Northeast Tire Mold公司采用高端加工机床和REGO-FIX刀具,使其产品的表面光洁度达到非常高的水平,以至于极大程度地减少了二次钳工操作,在某些情况下甚至不需要二次加工操作,除了最后的喷砂抛光处理之外。单是一个模块,加工车间常常需要花费40h进行钳工打磨作业,而Northeast Tire Mold公司在加工同一类模块时,已将这一时间减少到8h。
“当您考虑到我们车间的人数与机床数量时,我们正在以2:1的比例超越我们的竞争对手。”Northeast Tire Mold公司总裁Chris Sipe先生解释说,“他们需要多达4台的独立机床,而我们只需要两台机床。之所以能够达到这样的生产水平,关键在于我们拥有技术熟练的编程员和机械师、先进的机床、软件和精密刀具,但最关键的是我们拥有自己的模具制造工艺和生产流程。”
“我们可以在8个星期或更短的时间内完成全套轮胎模具的交货任务,对于一些实验性的模具,我们可以在10天内交货。”Chris Sipe先生说,“此外,我们的模具都非常的精确,客户只要选择其中的一个更换用模块,就知道其完全能够与现有的其他模块配套使用。我们是第一家有能力为客户提供这种模具的公司。”
声明:本网站所收集的部分公开资料来源于互联网,转载的目的在于传递更多信息及用于网络分享,并不代表本站赞同其观点和对其真实性负责,也不构成任何其他建议。本站部分作品是由网友自主投稿和发布、编辑整理上传,对此类作品本站仅提供交流平台,不为其版权负责。如果您发现网站上所用视频、图片、文字如涉及作品版权问题,请第一时间告知,我们将根据您提供的证明材料确认版权并按国家标准支付稿酬或立即删除内容,以保证您的权益!联系电话:010-58612588 或 Email:editor@mmsonline.com.cn。
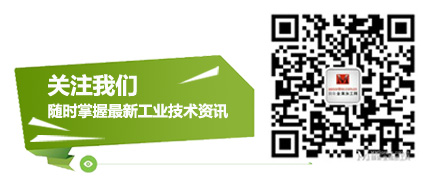
- 暂无反馈