切削加工技术是制造技术中应用最广泛的关键共性技术
切削加工技术是制造技术中应用最广泛的关键共性技术。全世界每年消耗于切削加工的费用约为1000亿美金,约10%的金属被切成切屑。通过正确地发展和应用加工技术,节约20%的加工费用是完全可能的。
毛坯精密成形+高效切(磨)削是提高切削加工水平的最有效途径
目前,机械加工发展趋势是高效率、高精度、高柔性、绿色化。切削加工的发展方向是高速、高性能(大进给)、硬切削、干(准干)切削和复合切削。
在发达国家,高速切削已成为切削加工的主流。发达国家金属材料的切削速度水平为:铝合金:2000~5000m/min,最高达7500m/min;铸铁:800~1500m/min,最高达2200m/min;钢:350~700m/min;钛合金:100~400m/min;镍基合金:60~150m/min。进给量水平为:车削4mm/r,铣削4mm/z。国外涂层刀具所占比例达到60%~70%。
我国有的汽车、航空、模具企业,也采用了高速加工技术,目前达到的切削速度水平为:铝合金:1000~2000m/min;铸铁:500~1000m/min;钢:300~500m/min;硬切削淬硬钢(50~65HRC):100~200m/min。涂层刀具所占比例为15%左右。
但是,目前我国切削主流仍然是以普通硬质合金、YG、YT和高速钢为主的传统切削加工。切削速度水平:铸铁和钢件:80~250m/min;钻孔:20~50m/min;攻丝:6~10m/min;滚齿:25~50m/min。数控机床和加工中心使用效率普遍较低。加工中心常作为一般数控机床使用,不用刀库,人工换刀。加工中心的开动率较低,平均约58.7%,而国外为70%~80%以上。
国内工具生产企业只有少部分从只生产标准刀具发展到以适应不同要求的专业刀具为主的现代企业,包括超细硬质合金、陶瓷、立方氮化硼刀具材料、刀具、刀体、刀柄、涂层等,而且建立了研究开发和实验中心。但大多数主要是生产普通的标准硬质合金刀片和高速钢复合刀具。国内高速、高效刀具的市场占有量仅约10%左右,其余主要依靠进口(国外有名的刀具厂家几乎在国内都设有工厂或代理商)。
坚持自主创新,走自我发展道路
我国切削加工行业应彻底转变只重视先进设备,不重视先进工艺和高效加工技术应用的观念,大力发展和推广先进高效加工制造技术。应重视和加强现代化刀具企业的建设,研究开发先进刀具(包括刀具材料、刀具、刀柄系统、涂层技术等),按行业要求,提供整套工艺和刀具服务。应大力发展和推进高效加工技术和相关辅助技术,缩短切削时间和非切削时间,大大提高加工效率和质量。
声明:本网站所收集的部分公开资料来源于互联网,转载的目的在于传递更多信息及用于网络分享,并不代表本站赞同其观点和对其真实性负责,也不构成任何其他建议。本站部分作品是由网友自主投稿和发布、编辑整理上传,对此类作品本站仅提供交流平台,不为其版权负责。如果您发现网站上所用视频、图片、文字如涉及作品版权问题,请第一时间告知,我们将根据您提供的证明材料确认版权并按国家标准支付稿酬或立即删除内容,以保证您的权益!联系电话:010-58612588 或 Email:editor@mmsonline.com.cn。
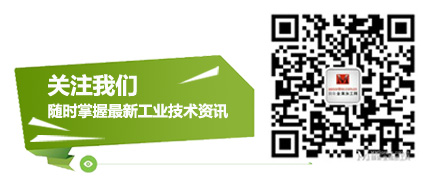
- 暂无反馈