正确的切入方法对耐热超级合金的车削加工至关重要
要想以相对较高的生产效率加工耐热超级合金(hrsa),就必须充分、仔细地准备相应的加工策略。由于车削工序在耐热超级合金加工领域占据主导地位(至少有50%以上的工序为车削加工),因此,正确的应用刀片是确保获得成功关键之一,其基本原则应立足于采用合适的切削刃切入方法。
耐热超级合金(hrsa)具有一些独特的属性,如具有极佳的高温强度、很好的韧性和抗腐蚀性等,使其成为汽轮机、喷气发动机、化工和食品设备、医疗器件等一些零件应用的唯一材料选择。但是,这些属性也意味着其切削加工相当困难--尤其是要求高效加工时更是如此。由于耐热超级合金的可加工性极差,因此要求对整个加工链中的所有环节--从机床到cad,从刀柄到切削刃等,都要很好地进行规划、选择和应用。
刀具的切入具有很大影响车削加工时,切削刃对工件的切入性主要取决于切削刃的主偏角,尤其是在车削耐热超级合金时,将直接影响生产效率的竞争力,因为它会直接影响刀具的进给率--该值在很大程度上决定了所需的切削时间。当主偏角较大时,进给率主要受刀片许用负载的限制,而其中部分由切屑厚度所决定。当主偏角较小时,切屑厚度必须足够大,以使切削刃能通过正常的切削而不是挤擦工件表面而形成切屑。就此而论,在切削深度一定时,切削刃越长,所形成的切屑就越薄(换句话说,较小的主偏角会生成较薄的切屑),此时应该采用更高的进给率以维持正常的切削。
此外,从刀具磨损的角度来看,在车削耐热超级合金时,切削刃的沟槽磨损是主要问题所在。切削刃上沟槽的形成在切削深度附近尤为明显。当切削刃主偏角呈90度,或当切削深度大于切削刃的刀尖圆弧半径时更是如此。在切削区域高温与室温过渡部分产生的氧化磨损是切削刃沟槽磨损的主要机理。使用小主偏角车刀车削耐热超级合金时可获得最佳的加工性能。
这就是车削耐热超级合金时推荐刀片应采用相对较小的主偏角(45度或更小)进行切入的大致背景。
实际方法--选择刀片首先,大多数可转位刀片带有可加强切削刃的刀尖圆弧。如果切削深度小于刀尖圆弧半径,则此时的(等效)主偏角一般都是可以的。因此,圆刀片就特别适合于耐热超级合金车削,因为其刀片半径就是以上所说的刀尖圆弧半径,并且通常切削深度值远低于刀片半径。r型刀片(圆刀片)能在较宽的切削深度范围内都得到小的主偏角。使用圆刀片车削耐热超级合金时,其切削深度应为刀片直径的15%左右,不要超高25%.
如果必须采用超出圆刀片工作范围的较大的切削深度,则以45度主偏角布置的方刀片是很好的选择,它非常适合于耐热超级合金的重载粗车。s型刀片(方刀片)具有坚固的切削刃,非常适合于粗车。如果由于某些原因刀具切入工件受限,或者必须用同一刀具车削外圆和端面,或者精车凹腔,以及工件不够稳定或是薄壁件时,就应选择具有合适的刀尖圆弧半径的菱形刀片。但是在许多情况下,xcel刀片为半粗/精加工工序的最佳选择。此种刀片结合了方刀片小主偏角与切削刃强度的优点与菱形刀片刀具在走刀方向上的灵活性,其优势包括更好的刀具可达性、减缓沟槽磨损的趋势、降低径向切削力以及恒定的切屑厚度。采用xcel刀片粗车台阶面尤为有利。
加工策略的最后阶段包括刀片槽形和材质的选择以及采用正确的切削参数。这些因素的选择必须充分考虑到零件的材料、结构设计和在切削加工的具体条件。至于切削参数,它指的是切削速度、进给量以及不能忽视的切削深度这三要素。在实际应用过程中,刀具走刀路径策略也已变得日渐重要,正确的刀具走刀路径策略可为用户带来巨大的好处。
声明:本网站所收集的部分公开资料来源于互联网,转载的目的在于传递更多信息及用于网络分享,并不代表本站赞同其观点和对其真实性负责,也不构成任何其他建议。本站部分作品是由网友自主投稿和发布、编辑整理上传,对此类作品本站仅提供交流平台,不为其版权负责。如果您发现网站上所用视频、图片、文字如涉及作品版权问题,请第一时间告知,我们将根据您提供的证明材料确认版权并按国家标准支付稿酬或立即删除内容,以保证您的权益!联系电话:010-58612588 或 Email:editor@mmsonline.com.cn。
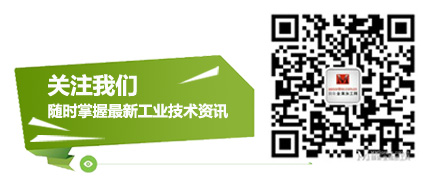
- 暂无反馈