重型切削车刀工具系统先进技术的应用
新型可调刀瘤切削(SWC)重型车削加工不仅是为了提高加工重型零件的生产率及设备利用率,还要求降低能耗并进行干切削。结合我国现代切削加工实际情况,设计新型可调刀瘤切削重型车削刀具时,应综合考虑刀具材料、刀具涂层和刀具几何形状之间的相互兼顾的优化关系,与解决不同切削条件下精粗加工工艺的集成以及对干式切削与绿色切削的新技术要求的实现程度问题,其相关技术和管理手段应服务并能优化整个加工过程的高效要求。 因而,新型可调刀瘤切削重型切削车刀工具系统先进技术的推广与应用对提高重车削效益有其重要的意义。
重型车削是指切削速度Vc≥38m/min,背吃刀量ap≥10mm,进给量f≥0.5mm/r的车削加工,在我国由于工艺条件所限,生产现场的重型车刀一般背吃刀量ap=25mm,进给量f≥1.0mm/r,切削速度度Vc≥40~60m/min,与普通加工相比,切削深度大、切削速度低、进给速度慢。加之切削过程中工件平衡较差、加工余量分布不均匀、机床的某些部件不平衡等因素引起的振动,使加工的动态不平衡过程要消耗很多的机动时间和辅助时间。与普通车刀相比较,重型加工切削用量较大、工作条件与刀具加固方式也有很大不同,刀具的设计具有自身的显著特点。所以,刀瘤切削重型车削加工不能仅表现在一道工序或一台设备上,应服务于整条生产线效益的提高,包括刀具结构、几何形状、刀体材料、切削刃材料、刀具涂层等多个方面综合的整体性能应服务于整个系统,刀瘤切削重型车削加工技术与便于操作与管理的工具系统的应用工程问题必须及时解决。
1.刀瘤切削重型加工刀具材料与刃口几何参数优化选择的系统性
1.1重型车削的刀瘤切削机理
重型切削深度一般可达30~50mm,且余量不均,工件表面的硬化层使粗加工阶段的刀具磨损以磨粒磨损为主。切削速度一般为15~20m/min,刃口处于积屑瘤发生的区与时段,因而在充分发挥刀具先进材质强度的基础上,改善与优化刀具结构和几何形状,能有效利用积屑瘤生成与消除规律进行刀瘤切削,也能从增大切削层厚度和进刀量入手,充分利用修光刃进行大进给的“Wiper”技术(即用一个短的直线或短的大半径圆弧来联结刀尖圆角和副切削刃,从而能降低已加工表面的粗糙度的技术),提高加工表面的光洁度,达到降低切削力、减小摩擦力,进行干式与绿色切削的高效加工目的。
1.2刀瘤切削重型车削刀具的高效材料特性与结构变化的系统性
刀瘤切削重型刀具刀片材质与型号的选用要符合加工系统条件的高效要求,否则就产生负面影响。因而,必须考虑刀具材料的耐磨损、抗冲击性能。弯强度低,冲击韧性差的陶瓷类刀具,不适应余量不均的重型车削,CBN也存在同样的问题。硬质合金的摩擦系数较低,刀具高温耐用度强,适于高硬度材料和重载车削粗加工,但要有具体的工艺措施。例如:
在加工钢料时,K类硬质合金重型车削时工件塑性变形大,摩擦剧烈,切削温度高,因此在重型车削中很少用,如采用热管式刀具,刃口有效持续冷却,适应性将会加强。P类硬质合金有高硬度、高耐磨性以及高耐热、抗粘结扩散能力和抗氧化的性能,是重型车削常用的刀具材料,适于加工钢料。但在低速车削且切削过程不平稳时,YT类合金的韧性较差,会产生崩刃,尤其是加工一些高强度合金材料时,YT类硬质合金耐用度下降快,无法满足使用要求。为进一步提高加工效益,刀具材料的应选用M类刀具或细晶粒、超细晶粒合金刀具(如643等)。与P类硬质合金相比,其在重磨前寿命的增加远远超过重磨后的寿命损失,因为它的另一个优点是刃口锋利,即在加工条件恶劣的场合也可替代高速刀具,应用范围比较广泛。加之细晶粒合金的耐磨性好,更适用于加工冷硬铸铁类产品,效率较YW类刀具可提高1倍以上。一般以上加工条件不能充分具备,所以重切削刀具结构必须考虑并适应因加工条件不足或变更,调换不同类型刀具材质,也即适应调换同类与不同类刀片和调整刃口几何参数的需要,刀具结构的相应变化应利于操作与管理的具体要求。
1.3刀瘤切削重型车削刀具可转位刀片尺寸的高效特点与调换的系统性能
重型车加工可转位刀片尺寸的具体要求为:正方形刀片的最小边长为19mm;三角形刀片的最小边长为19mm;五边形刀以提高生产率来说是一种经济的方法,刀片的最小边长为13mm;菱形要考虑刀片的最小边长为16mm。其刀片毛坯主要几何参数允差与平面度偏差应符合YS/T553-2006相关规定。为提高可调刀具工具系统高效管理与使用的简便可靠与标准化以及工艺过程集成的质量水平,刀片的精度等级应为A级或F级。为便于调整前后角的需要,后角相对刃口初始前角应在15°、20°、25°(代号为D、E、F)之间选取,从而具有7~15°左右的调整量。如主偏角调整变化的幅度较大,刀片形状应应在S、C、M型号之间选择。因而,为调换刀片的需要,刀具切削部分应在刃口背吃刀量的矢量线上留有调整刀片退量的尺寸。基于绿色切削的基本要求,刀槽主偏角应在45°~60°变化,这样刃口主偏角的变化,在不增大进给量的情况下,能增大切削厚度减小切削力,还能不同程度储存一部分机床功率以提高生产率。
刀片刃口几何参数的变化应具有以下特点:前角γo=15~30°、后角αo=5~8°、主偏角κr=45~75°、刃倾角λs=3~6°、过渡刃主偏角κrε=30~15°、副偏角κ'r=15~30°、修光刃偏角κr1=0°、修光刃刃倾角λs1=0~10°、主切削刃负倒棱宽度必须小于切削厚度ap(=f·sinκr)、bγ1=(3/4~1/2)f,刀尖圆角半径rε=0.3~1.0mm,修光刃长度为背吃刀量的1.5倍,刃倾角为+15°,起到刮削作用,刃口棱面负前角似=-30°由倒棱获得,效率将有所提高。刀槽初相角参数κcγ=60°∪45°、αco=(25°∪20°∪15°)、λcs=6°、副偏角κco=-30°。刀片角度为γpo=15°∪20°∪25°αpr=20°∪15°、刃倾角λps=0°。在κr<90°的情况下,主、副刃倾角均由前角调整15°左右获得。这样结合刀片的调换性能,能使刃口刀具几何参数与切削用量参数进行优化。
1.4涂层
为使刀具具有高可靠性,刀具涂层是不可缺少的,由于刀具涂层有类似于冷却液的功能,能产生一层保护层,把刀具与切削热隔离开来,使热量很少传到刀具,从而能在较长的时间内保持刀尖的坚硬和锋利。而表面光滑的涂层还可以减少摩擦来降低切削热,保持刀具材料不受化学反应的作用。重切削刀瘤切削刀片应选用TiAlN涂层和Mo2软涂层的多涂层刀具刀片,以有硬度高、耐磨性好的特性,又有摩擦系数小、切屑易流出的替代冷却液的功能。在干切削技术中,刀具涂层发挥着非常重要的作,用现已解决了涂层与基体材料结合强度低的技术难题应尽快应用于重车削的。
2.断屑可控性的降低与可调断屑宽度的刀片压板技术
一般,不可调刀具由于结构功能的缺陷,刃口前角参数的优化不理想,因而在重型车床上用大切深、大进给量车削钢件进时,切屑又宽又厚发紫,动力消耗既大,形成的C形屑更容易损伤切削刃或飞溅伤人。而刀瘤切削重型车削刀具刃口实际工作前角大(由积屑瘤形成的实际前脚可在50°左右),动力消耗减少1/3左右,切屑颜色由白转黄,且由于有过渡刃和负刃的作用,断屑槽的槽底圆弧半径加大(宽度一般为10mm),能使切屑向上卷曲,卷成螺旋线型发条状切屑,并能在加工表面上碰撞折断,或靠其自重坠落,可控性较强。不会使刀片切削刃不受冲击而破碎,生产效率能较大幅度提高。但未能很好解决它的刃口角度的调整与重磨问题,工作与冷却条件的变化以及档屑机理的不完善,断屑的可控性也会降低,因而可调断屑宽度的刀片压板技术问题应及时解决。
针对重型加工车削工作条件的变化情况,刀片可调整断屑宽度的压板前部卷屑的工作部分焊有厚3~5mm的硬质合金片。前端下部压住硬质合金刀片,而后端则与挡板球形内弧面紧密配合,并靠压板下部的有限往返直线运动调整位移量,以适应调换内接圆半径在一定范围变化的不同型号刀片与刀片重磨后调整夹紧的需要。上部压板能在下部压板的接触面上能作有限往返运动,且能靠压板螺栓有效紧固,强度较高。上部压板调整量为正负1~2mm,能使切屑成螺旋状卷出。断屑宽度调整量应依据切屑剖面的大小而定。不应使切屑猛烈冲击压板前端,否则会造成车刀的切削部分破裂,也要及时更换磨钝的或破裂的刀片,把切屑渣从压板上清理净。刀瘤切削在加工过程对档屑器的冲击不是很大,这种重型车刀的可调整断屑宽度的多功能压板结构效应较好。
该类可转位刀片应与刀垫、刀槽形成变界面组合梁,其伸出刀垫与刀槽前端边沿的长度不应超过2mm,以便于刀片的修磨与调整主偏角。刀片有单斜面与矩形截面两种。刀垫与刀片接合面有装配误差时,要及时修正以保证装配精度。压紧螺栓位于压板上方,为浮动压境装置,不容易被切屑损坏。比较适合重型切削,要求各部件配合良好,接触性能高,否则会产生较大振动,不利于生产效率和加工质量的提高。
3.刀具结构与工具系统
刀瘤切削重型车加工系统,要求刀具结构能在最小范围内适应加工系统中相关的调整、调换与变化要求,所以不仅要求切削部分与加持部分的构件的参数要在相近范围内有效变化,而求要求配合精度要符合刀具结构的动静刚度要求,因而不同类型刀槽参数要有相应的初相角,刀头切削部分不仅能做平面直线有限往返与圆弧的有限运动纵向,而且能做相应刀片定位销与刀片可调压板以及圆弧球面可调压板以及刀杆构件配合精度与连接强度高的配合精度与结合强度要高,并具有良好的平衡性能,刚性优异,不致发生异常振动,也能在承受较大切削力时有过载脱落装置,因而方形加持套与刀杆应通过计算采用热装结构。也可用国家发明专利车床类可调式刀具简式工具系统(专利号:200810017571.0)所配合进行组装,技术要求、性能与效益均能达到重切削的相应要求。材料可用用45#钢或4OCrMo锻造、车削成型,热处理硬度为45~48HRC,弹性变形量应满足刀具的结构性能的动态动、静刚度要求,才能作为机床功能的补充,满足加工系统的高效需要。
实践证明采用重型可调式车刀简式工具系统,具有很强的适应能力,初步实现了集约化与绿色化切削,有效提高工艺措施的经济性,从一般车床到最现代化的CNC车床都可适用,换刀时间只有一般车床刀具的1/20~1/10,且重复定位精度高,又有很好的加工尺寸稳定性,是模块式重型车刀技术的拓展,有较大发展前途。粗加工阶段以去除余量为主要加工目的,应加大切削深度,效率可提高5倍以上。重型切削时由于切削深度大,所以切削力大,相应的选择较低的切削速度,一般为10~15m/min,进给量为1~2mm/r。
4.切削用量的选择
在大型机床上(切削功率Pm在40kW以上),加工大型中碳钢、铸钢、及锻钢工件时,建议选用切削用量:
V=70m/min,f=1.2~1.5mm/r,ap=33mm,
在切削功率Pm=25kW的机床上,加工中型工件时:
V=5Om/min,f=3.15mm/r,ap=11mm;
将大型综合车刀改造为S.W.C可调式刀具,可使加工的综合效益提高到80%强。
5.结论
近年来,国外开发了许多大前角车削刀片和带正前角的螺旋形刀刃铣削刀片(这种刀片沿切削刃几乎有恒定不变的前角,背前角或侧前角可由负变正或由小变大),旨在减少机床的驱动功率,并通过减小切削力,降低切削温度来满足干切削时对刀具的要求。但未形成可调的工具系统,通用优化率不高,因而,由调整而综合形成的工具系统带来的S.W.C刀瘤切削切削加工效益就相对较高。面向加工系统与刃口几何参数在相近范围变化的具体特点,合理选择系统刀具角度初相角,优化构件与机构的调整性能,包括与CAPTO工具系统功能相似的刀具加持系统,并集成热管式刀具的特点,既能有效进行绿色干切削,又能形成便于操作与管理的系统功能,因而技术含量较高,与普通大进给车刀相比较,可明显看出其优越性,值得进一步研究探讨并推广运用。
声明:本网站所收集的部分公开资料来源于互联网,转载的目的在于传递更多信息及用于网络分享,并不代表本站赞同其观点和对其真实性负责,也不构成任何其他建议。本站部分作品是由网友自主投稿和发布、编辑整理上传,对此类作品本站仅提供交流平台,不为其版权负责。如果您发现网站上所用视频、图片、文字如涉及作品版权问题,请第一时间告知,我们将根据您提供的证明材料确认版权并按国家标准支付稿酬或立即删除内容,以保证您的权益!联系电话:010-58612588 或 Email:editor@mmsonline.com.cn。
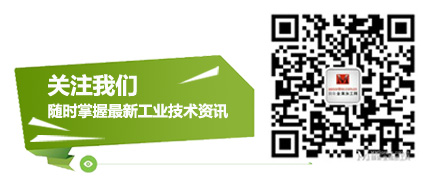
- 暂无反馈