动力涡轮盘榫槽拉刀设计
前言
涡轮盘是整个动力涡轮部分十分重要的零件,它的精度高、机械加工难度大,在整个涡轮机加工中也是一个难点。而在涡轮盘机械加工中,工作量最大、难度最高的是轮盘榫槽加工。
动力涡轮盘材质是GH698,属镍基合金,Ni含量大于70%,加工硬化严重,切削加工性非常差。而且轮盘精度要求高,机械加工难度非常大,对拉刀的结构与材质有非常严格且特殊的要求。
1 拉刀材质的选择
由于轮盘材质是高温合金GH698,加工性差,而且轮盘精度要求高,硬质合金刀具虽然在硬度、耐磨性和切削用量等方面优于高速钢,但其缺点很突出:不能承受较大的冲击力,强度低,只是高速钢的三分之一,热处理困难;整体硬质合金刀具制造困难,可加工性差,型线的铲磨必须用金刚石砂轮。普通高速钢由于在强度、硬度等方面性能指数低,不能采用,而粉末冶金高速钢如CPM-42,虽然韧性、硬度和可磨削性优于其它高速钢,但价格偏高,因此,也不采用。通过比较分析,拉刀材质选用M42(W2Mo9Cr4VCo8)钴高速钢。
M42热处理后硬度是67-69HRC,在加工中当温度提高至600-620℃时具有很高的红硬性,并具有很高的耐磨性,很高的强度及良好的工艺性能,因而榫槽拉刀材质选择M42是准确的。
2 粗拉刀结构的确定
粗拉刀长度的确定
轮槽拉刀是加工轮盘的专用拉刀,由于刀具齿型特殊,拉床、拉夹具等因素综合考虑,采用整体结构成套拉刀。每套9把,8把粗拉刀,1把复合精拉刀,拉刀定位尺寸为40mm×40mm。拉刀的长短则应根据实际情况而定,拉刀太短,数量多,加工繁复,工作量大;太长对于单把拉刀费用昂贵,一旦损坏,损失太大。对于轮盘拉刀,经反复论证,采用1000-1200mm比较合理,最终确定:长度依次是L1,2,4,5=1185mm,L3,9=1200mm,L6=1025mm,L7,8=1145mm。
切削余量的分配
榫槽的成型是根据两种切削图实现的,即非型线部分和型线部分,型线部分的拉刀比非型线部分的拉刀具有更高的加工精度。榫槽非型线部分成型是由N1~N6拉刀实现的,型线部分是由N7~N9实现的。
拉刀切削部分的几何参数
af为齿升量,即切削部前、后刀齿(或组)高度之差;P为齿距,即两相邻刀齿之间的轴向距离;ba1为刃带,用于在制造拉刀时控制刀齿尺寸,也为了增加拉刀校准齿前刀面的可重磨次数,提高拉刀的寿命。有了刃带,还可以提高拉削的稳定性;g0为拉刀前角;a0为拉刀后角。
粗拉刀切削部分几何参数的确定
齿升量af
在一定的拉削余量下,af越大,切去全部余量所需要的刀齿就越少,拉刀的长度也就越短,不仅可以节省刀具材料,拉刀制造容易,而且可以提高拉削生产率;但af过大,拉削力也增大,会导致拉刀折断或机床超载,拉后工件表面也得不到保证。因此齿升量的确定必须考虑到拉刀强度、机床拉力、以及工件表面质量等。根据轮盘的厚度,各把粗刀的拉削部位,分别采用0.05-0.07的齿升量。
齿距P
齿距是拉刀的重要设计要素,P过大,则拉刀过长,不仅制造成本高,而且拉削生产率低。此外,P过大,同时工作齿数太少,拉削过程不平稳,影响拉削表面质量。P过小,容屑空间小,切屑容易堵塞;同时工作齿数会过多,切削力相应增大,可能导致拉刀折断及机床超载;P过小,还会给刃磨带来困难,砂轮切入时有与相邻刀齿碰撞的危险。
齿距P可按下列经验公式计算:
P=(1.25~1.9)L½(L为拉削长度)
涡轮盘所需加工四级轮盘,每级76个槽,槽宽分别是50.55,轴向倾角20°,总切削长度为17m。每个槽的拉削长度是:L1=50/cos20°=53.20,L2=55/cos20°=58.53。
前角g0、后角a0和刃带ba1
对于轮盘来讲,其材质GH698粘性大,硬度高,弹性大,前角可取g0=10°,为减小切削力,减小回弹变形,后角应增大a0=3°,切削齿刃带ba1=0,校准齿刃带ba1=0.1~0.3。
其它切削部分的几何参数
容屑槽:选择为加长齿距型。这种容屑槽底部由两段圆弧和一段直线组成,齿距较大,有足够的容屑空间,便于在很大齿升量下加工复杂型面的榫槽。
分屑槽:针对工件材质的特性,N1~N4粗拉刀齿面宽且齿升量大,为了将切屑分割成一定的宽度,便于卷曲和容纳在容屑槽中,在拉刀切削齿后刀面上交错地磨出深度为hk=1分屑槽。
3 精拉刀切削部分几何参数的确定
由于精拉刀拉削过程是榫槽成型的最终形式,因而要保证榫槽表面的高质量,精拉刀的设计起着关键的作用。在设计上注意以下几点:
复合精拉刀由轮槽外圆平面成型拉刀,轮槽槽底成型拉刀,榫槽轮廓成型拉刀3部分组成。各部分拉刀的齿升af,齿距P各不相同,精拉刀齿升量af要小,在全齿型切削时更要小,对于整把精拉刀而言,齿升量前大后小。
榫槽轮廓成型拉刀校正齿要多,齿距要大,对于动力涡轮盘而言,最后3个齿距大于轮盘在倾斜20°方向上的厚度,形成单齿切削,这样使轮盘有充分的弹性回缩时间,使后一个校正齿再重新光一刀,保证榫槽表面的轮廓质量。
为提高精拉刀的使用寿命,保证型面轮廓的正确,设计时,拉刀轮廓取轮槽轮廓的最小实体状态,这样拉刀实体处于轮槽轮廓的上限。
在全齿型切削时,拉力突然增大,拉刀产生振动,容易崩齿或拉刀折断,不仅工件报废,而且会造成拉刀的损失,为避免这种情况的发生,设计精拉刀时要计算出全齿型切削时的齿数,将这些齿的齿根、齿底开分屑槽,保证可有效地断屑。
4 拉刀的制造
由于轮槽拉刀对刀具材质的各种性能要求非常高,因此对毛坯的锻造,热处理要求十分严格,特别是精拉刀型线部分的齿形加工有很大的难度。
加工时要注意以下几点:
刀齿前面和齿沟槽必须圆滑连接,不要出现尖角,影响排屑。
刀齿后刀面光洁度要好,这样可以减小切削阻力,避免应力集中,减小或避免机床的振动。
刀体与刀柄连接部分要保证整体的直线度、平面度,使之与拉夹具导向槽配合良好。
拉刀制造时要二次探伤,消除裂纹。
5 拉刀的修磨
刃磨条件
拉刀在使用时会逐渐的磨损,当拉刀磨损到一定情况时会影响榫槽的质量和拉刀的寿命,所以有必要对拉刀的刃磨条件和刃磨方法作一阐述。拉刀在拉削过程中判断拉刀刃磨的条件:
拉削成型的表面粗糙度突然下降;
拉力急剧增大;
拉刀切削刃的刃带宽度超过0.01mm;
加工中出现异常情况,如拉刀振动增大等。
拉刀的刃磨
拉刀材质M42,通过比较试磨,CBN(立方氮化硼)砂轮磨拉刀时要仔细观察槽口,注意以下几点:
拉刀磨不要往复磨削过快,否则会将拉刀刀齿烧糊,造成退火,使拉削时崩齿。
对于精拉刀和粗拉刀刀齿槽底圆弧! 不同,要有不同的专用的砂轮,保证圆弧和直线光滑连接。粗拉刀要用粒度为100的CBN砂轮,圆角为R2.5;精拉刀要用粒度为148~180的CBN砂轮,圆角为R1。
在磨校正齿时,要根据已拉削槽数,检测尺寸结果,万方数据进行少量磨削。
精拉刀校正齿后刀面必须用大理石油石修理,加工过程中每拉一个槽,必须对所有拉刀校正齿前刀面进行刮研,去掉积屑瘤(GH698比较粘)。
刃磨过后,每把刀必须消磁。
6 结论
上述方法设计的拉刀进行了拉削实践,拉削出的产品符合涡轮盘榫槽的设计要求,使用方法简单、修磨方便,是拉削涡轮盘榫槽非常好的拉刀结构。
声明:本网站所收集的部分公开资料来源于互联网,转载的目的在于传递更多信息及用于网络分享,并不代表本站赞同其观点和对其真实性负责,也不构成任何其他建议。本站部分作品是由网友自主投稿和发布、编辑整理上传,对此类作品本站仅提供交流平台,不为其版权负责。如果您发现网站上所用视频、图片、文字如涉及作品版权问题,请第一时间告知,我们将根据您提供的证明材料确认版权并按国家标准支付稿酬或立即删除内容,以保证您的权益!联系电话:010-58612588 或 Email:editor@mmsonline.com.cn。
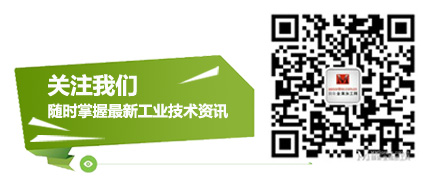
- 暂无反馈