深孔铰刀的改进
采用标准铰刀加工L/D>5的深孔时,操作比较困难,经常出现铰刀折断现象,且孔的表面质量不易达到加工要求,其主要原因是深孔排屑困难,堵塞在孔内的切屑容易刮伤已加工表面,并挤坏铰刀刀刃;此外,由于冷却液不易到达切削区,难以对铰刀进行有效冷却,从而加剧铰刀磨损甚至使铰刀折断。为解决这一问题,我们对标准铰刀的结构进行了改进。
1 铰刀结构及特点
在工具磨床上将标准铰刀的切削部分每隔一齿磨去一段,使切削齿减少一半。这样虽然加大了刀齿的平均切削负荷,但由于增大了容屑空间,使刀具排屑性能大为改善,避免了加工中切屑挤坏刀齿。此外,刀齿减少后,冷却液可顺利流入切削区,使刀具在加工过程中得到充分冷却,避免刀齿因切削温度过高而卷刃。改进后的铰刀加工寿命大大提高。据统计,一把Ø8mm 标准铰刀只能加工30余个工件即发生折断,而改进后的铰刀加工700多个工件后仍未损坏。
为避免铰刀齿数减少后对加工质量的不利影响,在磨齿时,铰刀校正部分约t/4(t为刀刃全长)处的一段刀刃仍保留原齿数。同时,在每个刀齿的切削部分磨出负刃倾角(l=-10°~-15°),以提高铰孔表面质量及铰刀寿命。
铰刀结构改进后,可提高切削速度并适当加大走刀量,使加工效率显著提高。用经改进的Ø8mm铰刀加工防爆电机机壳上92mm深孔时,铰削余量为0.3mm,机床主轴转速n=100r/min,走刀量s=0.43mm/r,冷却液为30%菜籽油+70%皂液。加工后的深孔精度可达二级,加工表面粗糙度可达Ra3.2µm。
2 铰削加工要点
1.切削速度
切削速度过高或过低均易产生卷屑,影响加工表面粗糙度。加工钢件时,适当的切削速度为v=4~5m/min;加工铸铁件时,适当的切削速度为v=4.5~5.5m/min。
2.铰孔余量
铰孔余量对铰削加工质量影响很大(对于深孔铰削尤其如此)。如铰孔余量过大,加工时铰刀易折断;如铰孔余量过小,则不能完全铰除前道工序留下的加工痕迹,影响孔的尺寸精度和表面粗糙度。根据加工经验,在钻床上进行铰削加工时,当被铰孔直径分别为3~4mm、5~10mm、12~16mm和18~30mm时,对应的铰孔余量可分别选取0.1mm、0.2mm、1mm和2mm。在车床上进行铰削加工时,铰孔余量可选取0.08~0.12mm。
3.进给量
根据工件材料的不同,在钻床上铰孔时,进给量可在0.17~1.5mm/r的范围内选取;在车床上铰孔时,进给量可在0.1~0.13mm/r的范围内选取。铰孔前应仔细检查机床套筒的偏摆不得过大。
4.冷却液
铰削加工不同材料的工件时,应采用不同类型的冷却液,如加工45钢、40Cr钢时,可采用30%菜籽油+70%皂液;加工铸铁时,只加少许煤油即可。铰孔时,冷却液的供应要充分,不能间断。
声明:本网站所收集的部分公开资料来源于互联网,转载的目的在于传递更多信息及用于网络分享,并不代表本站赞同其观点和对其真实性负责,也不构成任何其他建议。本站部分作品是由网友自主投稿和发布、编辑整理上传,对此类作品本站仅提供交流平台,不为其版权负责。如果您发现网站上所用视频、图片、文字如涉及作品版权问题,请第一时间告知,我们将根据您提供的证明材料确认版权并按国家标准支付稿酬或立即删除内容,以保证您的权益!联系电话:010-58612588 或 Email:editor@mmsonline.com.cn。
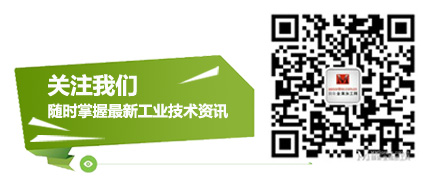
- 暂无反馈