刀具涂层提升加工效率
由于难切削材料所占比例越来越高,因此刀具磨损程度也日益严重,其使用寿命也逐步缩短. 材料科技领域中的大量技术创新可以不断带来满足部件应用与特性要求的新型材料和复合材料;对于机加工来说,诸如钛、镍合金和颗粒状铝质复合材料等难切削材料的比例在不断加大。在此类材料的加工上,特定几何外形刀片的加工工艺仍占据主要地位。其原因是,采用这种工艺可以达到良好的生产效率(切削量大)和很高的工件质量(表面质量稳定、形位公差小)以及很好的能源效益(切削厚度大和单位切削效率高)。
难切削材料加剧刀具磨损程度
高效和工艺稳定的加工作业也会存在不少问题,例如刀具磨损较严重,刀具使用寿命较短和刀具成本高等。
在这种状况下,就需要对刀具技术工艺进行新的研发。结合考虑所需的切削数据,目前的技术解决方案主要集中在刀片部位。
为了降低硬质耐磨损或软质非耐磨损的刀具材料的对立性,对新型切削材料合金进行了开发。硬质金属材料对切削加工意义重大。通过变动材料的颗粒大小、合金成分和粘合剂的比例与方式,可以有针对性地获得诸如硬度、抗压强度、E模数等方面的特定特性。
碳化钨(WC)的最大重要性在于它是一种硬质载体,通过在硬金属刀具中加入钴粘合剂,可以提高其抗弯曲强度,但是同时也会降低金属的硬度。为了阻止这种现象,使用了一种更细的(Hall-Petch比例为)0.7μm直径一下的碳化钨颗粒物。通过研发细颗粒(颗粒直径在0.7μm以下)、微颗粒(颗粒直径在0.5μm以下)和纳米颗粒(颗粒直径在0.1μm以下)技术,可以提高材料的硬度。在结合使用不同颗粒大小和不同粘合剂时,即可获得比标准硬金属更佳的材料特性。在相同条件下采用WC-10Co细颗粒硬金属立铣刀对不锈钢(X10CrNiMoTi 18 10)材料进行铣削时,可以达到双倍于K10普通颗粒硬金属的39m行程。
涂层技术可以延长刀具使用寿命
自从CVD和PVD刀具涂层技术问世以来,有90%以上的转位刀具采用涂层。涂层的目的一方面是通过降低摩擦来提高刀具和使用寿命并保护刀具免受高温的影响,另一方面则通过光学反差来更好判断刀具的磨损状况。通过采用诸如TiAlN对CBN转位刀片进行涂层,CBN转位刀片的使用寿命可以比未涂层的转位刀片提高30%~40%。在加工长材而遭遇刀具断裂的情况是CBN和PKD刀具所面临的一种挑战。通过采用激光烧蚀和电火花工艺,CBN和PKD转位刀片上的切屑排放等级和断屑几何外形均可被显现出来,由此可以提高工艺安全性和生产效率。除了宏观几何外形之外,微观几何外形也具备改进的潜力。例如通过采取特定的硬金属钻具刀片边缘磨圆措施,即使切削力较大,也可以实现较低的磨损量。
面对前面所述的各种挑战,由欧洲一家社会基金会和萨克森建设银行资助的Mittweida大学青年科研团队也在积极探索着各种解决途径。在数学、自然科学、信息学和机器制造等学科和学系的共同协作下,该高校有六名毕业生在对各种不同课题进行研究。
机器制造系负责研究“经四面体非晶碳(ta-C)、纳米晶体金刚石(n-D)和立方氮化硼(CBN)涂层、加工外形优化和可选择微结构化的刀具的应用”课题。科研小组对用于车削、钻削和铣削工艺的切削刀具涂层和此类刀具的微结构化表面的特性进行了研究。这种刀具应该能够提高切削加工的效率。当然,此项工作的主要目标则是要提高刀具的使用寿命、工艺流程的安全性和能源利用效率。
ta-C涂层钻刀的进给力减弱
首次钻孔试验在Si含量12%的AlSi铸铁合金材料上进行。所使用的刀具是直径为8mm的K10硬金属钻刀。在切削速度为126m/min、进给量为0.25mm和采用KSS乳化液的条件下,生成200多个钻孔。在使用ta-C涂层的刀具时,进给力减弱了大约20%,进给力的动态比例也随之降低。其中一个主要原因便是摩擦状况得到了改善。图4所示未涂层K10钻刀上的刀瘤生成状况。从图5中即可以看出,在涂有2μm厚ta-C涂层的K10钻刀上,刀瘤生成状况就显得无关紧要了。
声明:本网站所收集的部分公开资料来源于互联网,转载的目的在于传递更多信息及用于网络分享,并不代表本站赞同其观点和对其真实性负责,也不构成任何其他建议。本站部分作品是由网友自主投稿和发布、编辑整理上传,对此类作品本站仅提供交流平台,不为其版权负责。如果您发现网站上所用视频、图片、文字如涉及作品版权问题,请第一时间告知,我们将根据您提供的证明材料确认版权并按国家标准支付稿酬或立即删除内容,以保证您的权益!联系电话:010-58612588 或 Email:editor@mmsonline.com.cn。
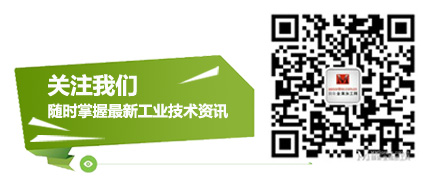
- 暂无反馈