切削温度测量方法综述
1.引言
在机械制造业中,虽然已发展出各种不同的零件成型工艺,但目前仍有90%以上的机械零件是通过切削加工制成。在切削过程中,机床作功转换为等量的切削热,这些切削热除少量逸散到周围介质中以外,其余均传入刀具、切屑和工件中,刀具、工件和机床温升将加速刀具磨损,引起工件热变形,严重时甚至引起机床热变形。因此,在进行切削理论研究、刀具切削性能试验及被加工材料加工性能试验等研究时,对切削温度的测量非常重要。测量切削温度时,既可测定切削区域的平均温度,也可测量出切屑、刀具和工件中的温度分布。常用的切削温度测量方法主要有热电偶法、光辐射法、热辐射法、金相结构法等。
2.切削温度测量方法
2.1 热电偶法
当两种不同材质组成的材料副(如切削加工中的刀具—工件)接近并受热时,会因表层电子溢出而产生溢出电动势,并在材料副的接触界面间形成电位差(即热电势)。由于特定材料副在一定温升条件下形成的热电势是一定的,因此可根据热电势的大小来测定材料副(即热电偶)的受热状态及温度变化情况。采用热电偶法的测温装置结构简单,测量方便,是目前较成熟也较常用的切削温度测量方法。
根据不同的测量原理和用途,热电偶法又可细分为以下几种:
(1)自然热电偶法
自然热电偶法主要用于测定切削区域的平均温度。采用自然热电偶法的测温装置是利用刀具和工件分别作为自然热电偶的两极,组成闭合电路测量切削温度。刀具引出端用导线接入毫伏计的一极,工件引出端的导线通过起电刷作用的铜顶尖接入毫伏计的另一极。测温时,刀具与工件引出端应处于室温下,且刀具和工件应分别与机床绝缘。切削加工时,刀具与工件接触区产生的高温(热端)与刀具、工件各自引出端的室温(冷端)形成温差电势,该电势值可用接入的毫伏计测出,切削温度越高,该电势值越大。切削温度与热电势毫伏值之间的对应关系可通过切削温度标定得到。根据切削实验中测出的热电势毫伏值,可在标定曲线上查出对应的温度值。
采用自然热电偶法测量切削温度简便可靠,可方便地研究切削条件(如切削速度、进给量等)对切削温度的影响。值得注意的是,用自然热电偶法只能测出切削区的平均温度,无法测得切削区指定点的温度;同时,当刀具材料或(和)工件材料变换后,切削温度—毫伏值曲线也必须重新标定。
(2)人工热电偶法
人工热电偶法(也称热电偶插入法)可用于测量刀具、切屑和工件上指定点的温度,并可测得温度分布场和最高温度的位置。人工热电偶法测温装置是在刀具或工件被测点处钻一个小孔(孔径越小越好,通常φ<0.5mm),孔中插入一对标准热电偶并使其与孔壁之间保持绝缘。切削时,热电偶接点感受出被测点温度,并通过串接在回路中的毫伏计测出电势值,然后参照热电偶标定曲线得出被测点的温度。
人工热电偶法的优点是:对于特定的人工热电偶材料只需标定一次;热电偶材料可灵活选择,以改善热电偶的热电敏感性和动态响应速度,提高热电偶传感质量。但由于将人工热电偶埋入超硬刀具材料(如陶瓷、PCBN、PCD等)内比较困难,因此限制了该方法的推广应用。
(3)半人工热电偶法
将自然热电偶法和人工热电偶法结合起来即组成了半人工热电偶法。半人工热电偶是将一根热电敏感材料金属丝(如康铜)焊在待测温点上作为一极、以工件材料或刀具材料作为另一极而构成的热电偶。采用该方法测量切削温度的工作原理与自然热电偶法和人工热电偶法相同。由于半人工热电偶法测温时采用单根导线连接,不必考虑绝缘问题,因此得到了较广泛的应用。
(4)等效热电偶法
采用自然热电偶法测量切削温度时,由于温升的影响,导线引出点的温度已不是标定时的室温,因此需要进行冷端温度补偿。但冷端温度补偿在原理和具体实现方法上均存在一定问题,如测量PCBN刀具的切削温度时,由于作为热电偶一端的PCBN复合片尺寸小、导热系数大,导线引出点的温升较大,影响测量精度,需要予以消除,但采用接长刀片消除法在PCBN刀具上不易实现,若采用附加电势消除法则因刀片引出点有温升,所测电动势也难以反映真正的切削温度。此时,可采用等效热电偶法测量PCBN焊接车刀外圆车削的切削温度,其工作原理是由刀片与工件组成自然热电偶的两极,热端为刀—屑接触部分A(其平均温度即为需要测量的切削温度θ);冷端分别为工件与刀具的引出端。工件引出点C处的温度为室温θ0,刀具引出点B由于距离刀尖较近而有温升,由于B点温度是测量计算切削温度所必须的,因此需同时测量B点温度θ′。测量时,采用一标准热电偶(NiCr-NiSi)测量B点温度θ′(其中NiCr端也是主测量回路C-AB的引出端)。测量得到两个热电动势:E1为工件—刀具—导线(NiCr)所构成的主测量回路产生的热电动势;E2为标准热电偶(NiCr-NiSi)产生的热电动势。通过标定装置获得各材料间的热电特性曲线,求出其斜率,再由测得的E1、E2计算出切削温度
θ为θ=E1/bWT+(bbw+bWT)E2/bbbWT+θ0
式中:bWT为工件—刀具的热电特性曲线斜率;bbw为导线—工件的热电特性曲线斜率;bb为刀具引出点测量热电偶热电特性曲线斜率。
2.2 光、热辐射法
采用光、热辐射法测量切削温度的原理是刀具、切屑和工件材料受热时都会产生一定强度的光、热辐射,且辐射强度随温度升高而加大,因此可通过测量光、热辐射的能量间接测定切削温度。
(1)辐射高温计法
使用红外辐射高温计可测定刀具或工件表面的温度分布。红外探测器将接收的红外线转换为电信号,经线性化处理后即可获得相应的温度值。但采用红外辐射高温计只限于测量刀具或工件外表面的温度。
(2)红外照相法
采用红外照相法的车削温度测量装置安装于车床横溜板的机座板上,使刀具、照相机相对于工件排成一线;照相机配有专门的红外辐射聚焦调节装置;刀夹可使照相机镜头尽可能接近工件表面;为避免切屑溅射的影响,照相机镜头用有机玻璃罩子罩住,镜头与工件表面之间设计了挡屑板,透过板上的小孔可对刀具和工件表面摄影(采用高温红外胶卷)。测量温度前,首先用热电偶进行定标校准,即热电偶由电加热并在不同温度下照相,所需曝光时间通过预试验确定,显影后的胶卷用显微光密度计读数,得到高温红外胶卷在不同曝光时间下光密度与温度的对应关系。根据此对应关系,可以确定切削过程中工件或刀具的温度。用红外照相法测定的切削温度可用于研究切削温度的分布情况。
(3)红外热像仪法
红外热像仪的基本工作原理是利用了斯蒂芬—波尔兹曼定律,即
E=εσT4
式中:E为物体辐射单元单位面积的辐射能量(W/m2);ε为物体辐射单元表面辐射率(取决于物体表面性质);σ为斯蒂芬—波尔兹曼常数(σ=5.76×10 -8W/m2·K4);T为物体辐射单元的表面温度(K)。
切削时,红外热像仪通过光机扫描机构探测工件(或刀具)表面辐射单元的辐射能量,并将每个辐射单元的辐射能量转换为电子视频信号,通过对信号进行处理,以可见图像的形式进行显示,显示的热像图代表被测表面的二维辐射能量场,若辐射单元的表面辐射率已知,则可通过斯蒂芬—波尔兹曼定律求出辐射单元表面的温度分布场及动态变化。虽然红外热像仪所测温度为相对温度,滞后于实际切削温度,但根据传热反求算法可准确求得切削过程中工件(或刀具)的温度变化规律及动态分布。红外热像仪测温法具有直观、简便、可远距离非接触监测等优点,在恶劣环境下测量物体表面温度时具有较大优越性。
此外,测量切削温度的光、热辐射方法还有红外干板法、红外聚光法、PbS光能电池法、高速切削双色高温计测量法等。
2.3 金相结构法
(1)金相结构法
金相结构法是基于金属材料在高温下会发生相应的金相结构变化这一原理进行测温的。该方法通过观察刀具或工件切削前后金相组织的变化来判定切削温度的变化,主要适用于高速钢刀具,因为当温度超过600℃时,高速钢的红硬性下降,组织结构发生一系列变化,可通过经抛光、腐蚀后的金相磨片来检查其金相组织变化。但这种方法的应用范围局限于金属材料制成的刀具,并且只有在高温下才能观察到材料明显的组织结构变化;此外,观测和分析的工作量也较大。
(2)扫描电镜法
扫描电镜法测量切削温度是用扫描电镜观测刀具预定剖面显微组织的变化,并与标准试样对照,从而确定刀具切削过程中所达到的温度值。应用扫描电镜法首先需要制取样件和对照样件,考虑到在不同温度和不同保温时间条件下材料的显微组织不同,对照样件需要多制取一些;得到对照样件的显微组织照片后即可确定被测刀具某一部位的切削温度。扫描电镜法测定切削温度的分辨率和确定温度分布的准确性均很高。但扫描电镜法也存在以下缺点:①只能测量600℃以上的温度;②样件制作相当繁琐;③属事后破坏性测量,不便于在生产现场推广应用;④所确定的切削温度分布状态属于定量分析;⑤设备复杂,技术难度高,实际应用受到一定限制。
2.4 其它方法
除上述切削温度测量方法外,常见的测温方法还有显微硬度分析法、量热法、涂色法等。
显微硬度分析法是将刀具、工件和切屑在不同温度下呈现不同硬度的基本原理进行逆向应用,根据材料受热后的显微硬度间接测知其切削温度。
量热法是将受热后的刀具、切屑或工件浸入水中并测定水温的升高,根据水的温升计算刀具、切屑或工件的温度。这种方法常用于测定金属切削过程中进入刀具、切屑或工件的热量百分比。
另一方法是将刀具沿切屑流出方向对称剖开,在剖面上涂上可在一定温度下熔解的微细金属粉末,然后将刀具合拢固定进行切削,切削完后再将刀具分离开,通过观察微细粉末熔化区域来确定刀具内部切削温度的分布情况。
此外,还可用涂色法确定切削温度,但该方法测量精度较低。
3.结语
综上所述,各种测量切削温度的方法各有其优缺点和不同的适用范围。因此,在实际应用中应根据具体情况选用最适当的切削温度测试方法。此外,为了在生产现场对切削温度进行更精确、更方便、更及时的测量,还需要对切削温度测量方法作进一步深入研究和改进完善。
声明:本网站所收集的部分公开资料来源于互联网,转载的目的在于传递更多信息及用于网络分享,并不代表本站赞同其观点和对其真实性负责,也不构成任何其他建议。本站部分作品是由网友自主投稿和发布、编辑整理上传,对此类作品本站仅提供交流平台,不为其版权负责。如果您发现网站上所用视频、图片、文字如涉及作品版权问题,请第一时间告知,我们将根据您提供的证明材料确认版权并按国家标准支付稿酬或立即删除内容,以保证您的权益!联系电话:010-58612588 或 Email:editor@mmsonline.com.cn。
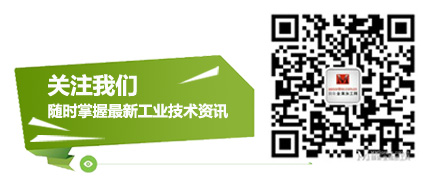
- 暂无反馈