高效加工助力曲轴制造
高效加工是发动机制造技术的鲜明特征,曲轴加工的技术进步是最好的证实之一。车-车拉、高速随动外铣、内铣和数控随动CBN磨削等高效加工技术的相继应用,使曲轴的生产效率得到了很大的进步。
进入21世纪以来,高效加工技术与设备在曲轴制造中得到了迅速的推广应用,曲轴生产效率得到了很大的进步。车-车拉、高速随动外铣、内铣和数控随动CBN磨削等高效加工技术和设备相继应用,不仅效率高,而且加工精度非常高。由于这些技术和设备的高效和柔性,曲轴生产线的生产设备数目比以往少了很多,总体生产本钱相应降低。笔者曾考察过上海大众、通用等企业的轿车发动机曲轴生产线,全线仅有15~20台先进的高效设备,并分为几个模块单元,产品周转线短,加工效率非常高,且易于质量治理。
与此同时,新型硬质合金刀具已经被广泛使用,CBN(立方晶氮化硼)、PCD(聚晶金刚石)刀具和陶瓷刀具等代表当今技术发展水平的超硬刀具在发动机制造中的应用也越来越多,组合式刀具和复合刀具也正大展效能,为高效加工和降低制造本钱提供了更多选择。
车-车拉技术
车-车拉技术在国外被大量用于曲轴主轴颈和连杆轴颈的半精加工,其加工可分为三种形式:直线车拉、内环刀具旋转车拉和外环刀具旋转车拉。车拉工艺在1983年左右被开发出来,到1988年短短5年中,车拉工艺从直线式发展成回转式,到1988年发展到车-车拉工艺,目前,其拉削方法又逐步发展为梳刀工艺。
车-车拉工艺通过一次设定能够完成所有同心圆的车削,具有高效率、通过使用特殊卡盘和刀具系统实现柔性加工、机床保养简便且维护本钱低等优点,特别适用于平衡块侧面不需加工、轴颈有沉割槽的曲轴加工。其中拉削工艺可用高效的梳刀工艺代替,梳刀加工通常在该工序的最后工步,通过微量的径向进给和纵向车削实现高速精加工。采用梳刀工艺的优点在于精度高、效率高、切屑易清理且轴向进刀量小。
高速外铣技术
高速外铣技术产生于20世纪90年代中期,对于平衡块侧面需要加工的曲轴,高速外铣技术比车削、内铣和车-车拉的生产效率还要高。以四拐曲轴为例,车-车拉工艺加工连杆轴颈要两道工序,而高速外铣工艺一道工序就能完成。高速外铣具有以下优点:应用工件回转和铣刀进给伺服连动控制技术,可以一次装夹不改变曲轴回转中心随动跟踪铣削曲轴的连杆轴颈,切削速度高(可达350m/min)、切削时间和工序循环时间较短、切削力较小、工件温升较低、刀具寿命高、换刀次数少、加工精度更高以及柔性更好,所以高速外铣技术将是曲轴主轴颈和连杆轴颈粗加工的发展方向。
声明:本网站所收集的部分公开资料来源于互联网,转载的目的在于传递更多信息及用于网络分享,并不代表本站赞同其观点和对其真实性负责,也不构成任何其他建议。本站部分作品是由网友自主投稿和发布、编辑整理上传,对此类作品本站仅提供交流平台,不为其版权负责。如果您发现网站上所用视频、图片、文字如涉及作品版权问题,请第一时间告知,我们将根据您提供的证明材料确认版权并按国家标准支付稿酬或立即删除内容,以保证您的权益!联系电话:010-58612588 或 Email:editor@mmsonline.com.cn。
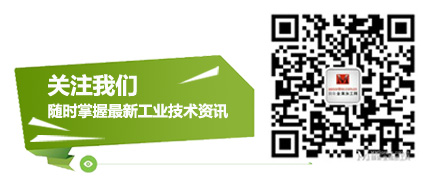
- 暂无反馈