扁钻的改进
电站工矿备件的深孔加工是重机行业中常见的也是较复杂的工艺过程。目前发展比较成熟的深孔加工刀具有扁钻、BTA套料钻、M型钻、喷吸钻、枪钻和错齿内排屑钻等。扁钻在电机转子深孔加工中占有重要地位,多用于钻削直径大于75mm、长径比大于35的深孔。与其它深孔刀具相比,扁钻具有结构简单、制造成本低、使用方便等优点。但在进行深孔加工时,扁钻的工作环境封闭、恶劣;同时,由于操作者无法观察扁钻的工作状态,加工时易出现切削热过于集中而烧刀的现象。因此,对传统扁钻的结构进行改进势在必行。
1.存在的问题
传统扁钻的材质为高速钢,切削速度较低。因受整体式结构的限制,扁钻的工作前角为负前角,轴向力和扭矩较大;其导向主要依赖于扁钻夹头上的定位导向键(后导结构),导向不稳,容易走偏;扁钻的切削刃采用对称结构,不能有效分割切削层厚度。钻削实心件时,若扁钻刀尖磨钝,则有可能在工件表面形成挤压,使钻削力和扭矩突然增大,导致崩刃现象的发生,使扁钻整体报废。
2. 结构的改进
由上述分析可知,传统扁钻结构不合理是造成扁钻加工效果差、易报废的主要原因。为此,可从以下几个方面进行改进:
·将整体式结构改为装配式结构,选用硬质合金刀片并将刀片的工作前角选为正前角(0°~6°),以改善受力状况;
·将切削刃的对称结构改为不对称结构,可有效分割切削层厚度;
·在扁钻中心增加一只麻花钻,用以分担部分切削力。
采用装配式结构,上、下刀体对刀片起夹持和定位作用;麻花钻位于刀体的中心,不仅可承受部分切削力,还可提高定位精度;硬质合金刀片嵌装在上下刀体之间、麻花钻的两侧,刀片安装呈不对称结构,两侧锥角也不相等(θ1=25°,θ1=20°)。当硬质合金刀片磨损后,可通过顶丝和楔块调整刀片的伸出量,使刀片重复使用。
3.改进后的效果
采用改进后的扁钻进行深孔加工时,由于刀体中心的麻花钻先开始切削,因而承受了比硬质合金刀片更大的轴向载荷,改善了离刀具中心较远的刀片的工作条件。由于左右两侧的刀片交错排列,使切屑分为长度相等的小段,易于排屑,提高了刀具耐用度。两侧锥角q1和q2不等,使切削层的厚度得到有效分割,在进给量和切削面积一定的情况下,切削力可分布在各个刀片上。采用装配式硬质合金扁钻进行深孔加工,相当于将钻孔—镗孔两道工序合在一起,减少了加工和辅助时间,提高了生产率。
使用改进后的扁钻加工电机转子深孔(Ø150×1000mm),加工后的中心孔弯曲度为0. 75mm/ 全长,加工用工时13.5h/1000mm,光洁度达到Ra3.2。生产实践证明,用改进后的扁钻加工深孔,导向性能好,轴向力和扭矩小,加工精度高,刀具耐用度高,生产效率比使用传统扁钻提高三倍多,是一种比较理想的深孔加工刀具。
声明:本网站所收集的部分公开资料来源于互联网,转载的目的在于传递更多信息及用于网络分享,并不代表本站赞同其观点和对其真实性负责,也不构成任何其他建议。本站部分作品是由网友自主投稿和发布、编辑整理上传,对此类作品本站仅提供交流平台,不为其版权负责。如果您发现网站上所用视频、图片、文字如涉及作品版权问题,请第一时间告知,我们将根据您提供的证明材料确认版权并按国家标准支付稿酬或立即删除内容,以保证您的权益!联系电话:010-58612588 或 Email:editor@mmsonline.com.cn。
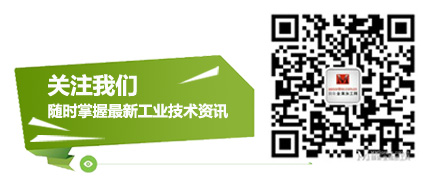
- 暂无反馈