现场刀具试切带来的改变
一场现场的刀具试切能给用户带来什么改变相信太重液压分公司的技术人员最有发言权。
在试切现场,各刀具供应商带来的加工方案为液压分公司加工效率的整体提升贡献颇多,例如:螺纹加工效率提高1倍,加工精度和粗糙度提高2级;阀块组件加工时,平面铣削、钻孔、镗孔、绞丝、倒角等加工工序缩短到1min内,表面光洁度良好,刀具使用寿命变长;主轴加工时的根部退刀槽难题得以解决,新的刀具刃口安全性良好,断屑效果非常理想,加工效率明显提高。
这样的改进案例不胜枚举,这里既有加工现场技术人员辛苦的付出,这里有刀具供应商走进加工现场带来的功劳。现场试切还为技术人员打开了另一扇门,更多的工艺改进得以成型,并通过不断试切变得成熟。以液压油缸缸筒内孔加工为例,太重液压在进行液压油缸缸筒内孔加工时,原使用深孔镗、深孔珩工艺,加工效率低、粗糙度差。通过与刀具制造商的工程师交流,太重液压现场技术人员进行讲加工工艺改为深孔镗、深孔滚压工艺,使加工效率提高2倍,粗糙度提高1级。
原工艺进行粗加工时使用YT15整体焊接刀,需要操作者进行刃磨,刃磨后还要对镗刀调整尺寸,加工过程中容易崩刃,刀具寿命短。精加工采用高速钢镗刀,留珩孔磨量0.3~0.5mm,粗镗和精镗用时都在1h左右。由于珩孔使用的是油石做的刀具,一个油缸筒珩成的总时间将近4h,且表面粗糙度为仅为Ra1.6,表面硬度低。改进后的深孔滚压技术,在粗加工时用的刀具为数控分体式刀具,刀片的各方面加工参数都要比YT15刀具参数高,且不易崩刃。在加工一定数量缸筒需要进行换刀片时,镗刀尺寸不需要调整可以可实现连续加工。精加工使用的浮动镗刀材质为硬质合金,粗镗和精镗时间一般只需30min,在切削效率方面要比高速钢刀具快1倍还多,且刀具使用寿命长。最后余量只需0.03~0.05mm,滚压成形的时间只需8~10min,且缸筒表面粗糙度达到Ra0.8,切缸筒内孔的硬度高,在使用过程中的寿命更长。
原工艺采用螺纹连接方式,装夹不便且花费时间较长,改进后的连接是靠缸筒两端5×30°倒角定位,装夹方便且用时较短,定位精度高。另外,由于原装夹方式要求缸筒尺寸加长80mm,在缸筒成型后再去点,浪费掉的材料成本也会随缸筒内径加大而大幅增长。而改进后的技术只需要在原缸筒长度的基础上加长10~15mm,加工工时也减少将近一半。
工艺改进前,1天只能加工3~5个缸筒,改进工艺后1天可以加工10~12个,加工效率提升幅度尤为明显,且加工质量也得以大大改善。
现场试切让液压分公司在刀具选用和切削工艺水平上都有了长足的进步,正如分公司经理郭英豪所说:“我们希望有更多的刀具供应商来到我们的加工现场,给我们带来更多的更先进的刀具和技术,也为我们加工现场的工艺改进提供更多的建议和方案。”
声明:本网站所收集的部分公开资料来源于互联网,转载的目的在于传递更多信息及用于网络分享,并不代表本站赞同其观点和对其真实性负责,也不构成任何其他建议。本站部分作品是由网友自主投稿和发布、编辑整理上传,对此类作品本站仅提供交流平台,不为其版权负责。如果您发现网站上所用视频、图片、文字如涉及作品版权问题,请第一时间告知,我们将根据您提供的证明材料确认版权并按国家标准支付稿酬或立即删除内容,以保证您的权益!联系电话:010-58612588 或 Email:editor@mmsonline.com.cn。
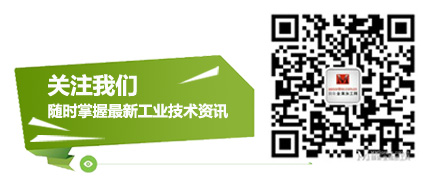
- 暂无反馈