实现超高速铣削途径的探讨
在粗加工时,加工效率以每分钟加工出的体积表征,加工体积与切削速度、进给量和切削深度成正比;在半精加工和精加工时,加工效率以每分钟加工出的面积表征,加工面积与切削速度和进给量成正比。故提高切削速度能成正比地提高加工效率。多年来切削加工专家一直在研究提高切削速度的技术,虽然在各种研究报告中,都曾介绍每分钟达到上千米的切削速度的研究结果,但都是实验室的成果,没有投产。
一、发展超高速切削的道路
1. 从切削理论可知,切削温度q与切削速度v的关系为:q=cv0.4。
目前生产中采用硬质合金刀具加工钢料的速度一般为100~300m/min,采用陶瓷刀具精加工钢料的切削速度为200~500m/min,采用氮化硼精切削加工钢料为300~600m/min。此时的切削温度约为800~1200℃。按此切削规律可以推算出,若切削速度为5 000m/min时,切削温度约为3300℃;若切削速度为10 000m/min时则为4400℃。
因此,遵循上述基本规律,研究发展超高速切削的途径主要集中在发展耐高温的材料,由于高温高硬材料的耐热性研究,近年没有大的进展,故近二三十年超高速切削也没有大的进展。
2. 由切削理论可知,最佳的切削条件位于刀具与工件硬度比最大的区域。当横坐标为温度,纵坐标为硬度时,设曲线1为硬质合金刀具硬度随温度的变化,曲线2为工件硬度随温度的变化,则当切削温度为900~1100℃时,刀具硬度与工件硬度比最大,此时刀具最耐用。它给人们的启迪是,若能设法将刀具温度和工件温度区别开,使刀具温度保持较低,而使工件温度升到较高,就可能开辟出发展超高速切削的新途径。
二、提升工件区温度的途径
1. 正压力变形造成温度的升高,设刀具经淬硬热处理,工件为未淬火钢,当刀具单位压力P超过工件的屈服强度时,工件材料内部产生滑移,并出现大量的内摩擦热及温升。而此时的应力小于刀具的抗压强度,因此,淬硬的刀具无内部滑移及生热。从强度理论可知,最大滑移的应力并不在刀具与工件的接触面上,而在工件接触面以下约0.2mm处。因此,工件内最先在高接触面以下部位出现裂纹,形成低强度面。
2. 超高速切向摩擦造成温度再升高,若再使刀具沿切向V作超高速移动,由于刀具与工件表面凹凸处的咬合和粘结,工件的切向撕裂面一般不在接触面,而多数在已形成微裂纹的,平行于接触面的下面一个平面。另外,由于接触面被刀具带走一部分热量,温度较低;而撕裂面温度相对较高,强度较低,从而造成刀具带去一层工件材料。
若刀具为铣刀,则前一个刀齿利用正压力(进给)和摩擦力(切削速度)将工件加热,造成工件的强度下降几倍。则后一刀齿的任务,就是把这一层刮去了。当然,后一个刀齿(如上)又为再后一个刀齿加热工件。故它的本质是一种加热超高速切削。
3. 利用三维热传导方程:dq/dt=a(¶2q/¶x2+¶2q/¶y2+¶2q/¶z2)以及有限元法,可以找到温控方程,代入有关切削参数(具体参数见第四部分),可算出切削区温度场,最高温度为922℃。此时,由图1工件材料硬度与温度曲线,可得工件材料的硬度将由40HRC降到8HRC左右。
三、保持刀具刃区低温的途径
提高切削速度,减少刀具与工件接触的时间。设铣刀直径为f1800mm,工件切削长度为100mm,则当切削速度为1000m/min时,铣削刀刃与工件接触时间为6ms;当铣削速度为10 000m/min时,接触时间为0.6ms,而热量在钢中的传播速度为0.5mm/s。因此,热量刚传到0.3µm深度时,刀具就切出了,即热量还来不及传到刀具中。
2. 加强铣刀的冷却。设若铣刀直径为f1800mm,其周长为pd≈5.65m。因此,刀齿有5.65m的空行程,受一点热又被冷到常温了。刀具刃区的温度曲线,温度始终在常温到300℃范围徘徊。
设法让刀刃形成保护层。刀齿的金相磨片,由图看出,刀齿在生产中使用24h后,当刀具材料为65Mn时,其金相组织仍为马氏体,刀刃区的显微硬度为564~570HV(53~54HRC),还是原来的淬火硬度50~55HRC。而在刀刃顶部(外圆)有一层白色的吸附层,其显微硬度达974~1094HV(68~70HRC)。这一高硬度层,代替刀刃在进行切削。
四、超高速切削的生产实践
在现代钢厂的钢坯切割中,要求很高的效率,才能跟上连轧机的节拍。它采用锯片的直径为f1800mm,转速为1500r/min,切削速度为8482m/min,进给量为100mm/s。锯片材料为65Mn,硬度为50~55HRC。使用寿命一般达24h,也就是说,已经在生产中实现了超高速切削。笔者从事了上述实践过程,并对其进行了理论分析。
声明:本网站所收集的部分公开资料来源于互联网,转载的目的在于传递更多信息及用于网络分享,并不代表本站赞同其观点和对其真实性负责,也不构成任何其他建议。本站部分作品是由网友自主投稿和发布、编辑整理上传,对此类作品本站仅提供交流平台,不为其版权负责。如果您发现网站上所用视频、图片、文字如涉及作品版权问题,请第一时间告知,我们将根据您提供的证明材料确认版权并按国家标准支付稿酬或立即删除内容,以保证您的权益!联系电话:010-58612588 或 Email:editor@mmsonline.com.cn。
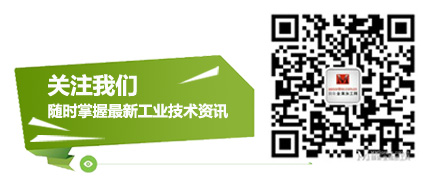
- 暂无反馈