金刚石刀具高速精密切削加工的研究
精密切削加工通常是指加工尺寸精度为0.1~1µm,加工表面粗糙度达Ra0.02~0.1µm 的切削加工。精密切削加工技术是机械制造业最重要的基础技术之一,在某种程度上可代表一个国家制造技术的整体水平。但目前在大多数生产过程中,为获得高的加工精度,精密加工切削速度通常低于常规加工切削速度,如实际生产中精密加工铝合金零件的切削速度多在v=100m/min 左右,大大低于铝件普通加工的切削速度(v=200~300m/min)。这就导致精密零件加工效率较低,生产成本较高,产品开发周期和在制时间较长。随着精密加工的应用范围日趋广泛,现代精密加工技术不仅应达到很高的加工精度,同时要求能以较低加工成本获得较高的生产效率和产品合格率。因此,研究在高速切削条件下实现精密切削加工具有重要的现实意义。为此,我们在高速数控车床上采用金刚石刀具进行了精密切削试验,通过优化切削用量,获得了高精度加工表面,并探讨了刀具状况、切削方式(干切削或湿切削)、切削用量等因素对加工表面粗糙度的影响规律。
高速精密切削试验
试验条件
工件材料:LY12高强度铝合金,工件尺寸Ø140×150mm。
切削刀具:①聚晶金刚石刀具:刃口经研磨后Ra<0.02µm,直线形修光刃be=0.11mm;②天然金刚石刀具:刃口经研磨后Ra<0.02µm,圆弧型刀尖re=0.9mm。
切削用量:ap=0.025~0.1mm,f=0.005~0.02mm/r,v=400~1200m/min。
加工表面粗糙度测量
采用微机辅助轮廓仪测量工件表面粗糙度。轮廓仪对加工表面进行触针扫描,表面微观不平度信息以电模拟量(电压)形式输出,再通过采样和A/D转换得到一组离散型表面微观不平度数据,经计算机专用软件处理后打印输出Ra、Rz、Ry、s、sm测量结果及轮廓曲线图。
切削条件对加工表面粗糙度的影响
刀具材料、刀刃形状及研磨质量的影响
天然单晶金刚石硬度和耐磨性极高,导热性好,摩擦系数低,可刃磨出极为锋锐的刀刃,是高速超精密切削铝合金的理想刀具材料。人造聚晶金刚石无法磨出r≤1µm 的锋锐刃口,因此难以达到超精密镜面切削的要求,但可用于有色金属和非金属材料的高速精密切削,且刀具成本大大低于天然金刚石刀具(本试验所用天然金刚石刀具与人造聚晶金刚石刀具的价格比为7: 1)。为获得高精度加工表面,金刚石刀具的主、副切削刃之间必须修磨成直线或圆弧过渡刃(修光刃)。直线修光刃理论上可获得比圆弧修光刃更低的加工表面粗糙度,但要求刀刃方向与进给方向严格一致,因此对刀较困难;圆弧修光刃对刀容易,使用方便,更适合加工高精度回转曲面,但刀具的制造工艺性较差,成本相对较高。
本切削试验中,两种金刚石刀具在相同的高速切削条件下(v=800m/min,f=0.01mm/r,ap=0.01mm,加乳化切削液)获得的加工表面粗糙度值。
两种刀具获得的加工表面粗糙度值 表面粗糙度参数 聚晶金刚石刀具 天然金刚石刀具
Ra(µm) 0.1068 0.0778
Ry(µm) 0.812 0.496
与采用直线修光刃的人造聚晶金刚石刀具相比,采用圆弧修光刃的天然金刚石刀具的加工表面粗糙度Ra值下降了27%,而Ry值的下降幅度则达40%。在后续切削试验中,Ry值的下降幅度均较大。由此可知,天然金刚石刀具不仅可减小被加工表面轮廓曲线的峰谷均值,而且可显著降低表面轮廓曲线波动的最大高度,其原因在于天然金刚石刀具刃口更锋利,切削变形小,切削刃边界挤压减小。因此,在高速精密加工中,刀具的刃口锋锐性对加工表面粗糙度的影响比刀具过渡刃的几何形状更为重要。
在高速精密切削加工中,无论采用何种金刚石刀具,其刃口及前、后刀面的研磨质量(锋锐性、完整性、光洁度等)对被加工表面粗糙度均有重要影响,这一点与普通切削速度下的加工情况相同。表2 为用刃口区研磨质量不同的聚晶金刚石刀具在三种不同切削速度下进行切削试验时获得的加工表面粗糙度值(切削条件:v=500,800, 1100m/min,f=0.01mm/r,ap=0.05mm,直线修光刃be=0.2mm,加乳化切削液)。由试验结果可知,刀具研磨质量的影响十分显著。
研磨质量不同的聚晶金刚石刀具的加工表面粗糙度 刀具研磨质量 加工表面粗糙度Ra(µm)
v=500m/min v=800m/min v=1100m/min
研磨(▽12) 0.210 0.180 0.235
精研(▽14) 0.109 0.102 0.132
干、湿切削方式的影响
高速切削加工铝合金时,干、湿切削方式对加工表面粗糙度影响较大。干式切削时(尤其当背吃刀量ap<5µm时),切屑呈薄絮状,由于切削速度高,加工表面的切痕和粘结现象十分明显,表明此时积屑瘤较严重。湿式切削时(加特制乳化切削液),加工表面粗糙度显著改善,可达到与普通速度精密切削(加润滑油)相同的效果。
切削用量对加工表面粗糙度的影响
高速精密切削时,切削用量的选择是影响加工质量和加工效率的主要因素。对应于不同的工艺条件,需要通过切削试验来确定合理的切削用量。在本切削试验中,根据高速数控车床的性能特点,并为了进行比较,选用的切削速度范围从常用的 200m/min直至超高速切削的1200m/min;选用进给量范围为0.002~0.02mm/r;采用经精密研磨的人造金刚石刀具切削LY12铝合金(加乳化切削液)。通过优选切削用量,获得了Ra=0.04~0.10µm的高光洁表面,即在比常用切削速度高8 倍的切削条件下获得了相当于▽11 光洁度的加工表面。下面分析各切削用量对加工表面粗糙度的影响。
切削速度的影响
传统的精密、超精密加工大都在较低切削速度下进行,如生产中对LY12铝合金进行高精度加工(Ra≤0.06µm)时,切削速度通常为v=80m/min 左右,而且对操作人员的加工经验具有较高要求。在本切削试验中,切削速度v 对加工表面粗糙度的影响结果。
(f=0.02mm/r,ap=0.03mm)
(v=800m/min,ap=0.03mm)
(v=800m/min,f=0.01mm/min)
从v=400m/min 开始切削,随着切削速度的提高,加工表面粗糙度值不断增大,但两种金刚石刀具的变化规律略有不同。v=400m/min时,加工表面粗糙度值最小,用天然金刚石刀具可加工出Ra=0.04µm 的表面;v=800m/min时,聚晶金刚石刀具的加工表面粗糙度值稍有增大,而天然金刚石刀具加工表面粗糙度值的增加幅度相对较大。当切削速度提高到v =1200m/min时,天然金刚石刀具加工表面的粗糙度值反而比v=800m/min时有所降低。总的来看,在高速切削区域可获得较低的加工表面粗糙度,且随着切削速度的提高,表面粗糙度值变化幅度不大,特别是天然金刚石刀具对切削速度的变化不敏感。
在更宽的切削速度范围内进行切削试验,同时测量了切削力和振动。试验结果表明,当切削速度v=100m/min时,机床和工件的振动较大,加工表面较粗糙(这一点在对45钢的切削试验中也得到了验证);但当切削速度提高到v=400m/min(转速n=910r/min)时,机床和工件的振动明显减小,加工表面变得较为光滑;而在400~1200m/min的切削速度范围内,机床和工件的振动均较小,可获得光滑的加工表面。显然,在满足精密加工要求(Ra≤0.1µm)的前提下,采用800~1200m/min的切削速度进行数控加工,可大大提高精密切削的生产效率和自动化水平。
进给量的影响
切削试验中,进给量对加工表面粗糙度的影响规律如图2所示。人造聚晶金刚石刀具以f=0.015mm/r的进给量切削时,表面粗糙度值有一个跃升;而在f=0.005mm/r和f=0.02mm/r时加工表面粗糙度相差不大;当f>0.02mm/r时,加工表面粗糙度值将迅速增大,说明该进给量不适用于超精密加工。天然金刚石刀具以f<0.02mm/r的进给量进行切削时,加工表面粗糙度值变化很小。为获得高光洁表面,精密切削加工时一般采用极小的进给量。试验表明,用f=0.005mm/r的微小进给量切削时,加工表面十分光洁,刀具上的积屑瘤很小;当f 值增大时,聚晶金刚石刀具的加工表面粗糙度随着积屑瘤高度的变化而变化,而天然金刚石刀具的加工表面粗糙度几乎不发生变化,这是因为天然金刚石刀具刃口锋利,刀面光洁,与工件材料的摩擦系数较小,因此产生的积屑瘤很小。但在切削试验中也发现,采用更小的进给量切削时,工件表面的挤压和粘结痕迹较明显,表面粗糙度值反而增大,加工效率也进一步降低。合理的进给量应选为f=0.02mm/r,此时可获得与f=0.005mm/r时相同的加工表面质量(Ra=0.06µm),而加工效率可提高4倍。
背吃刀量的影响
背吃刀量ap的大小对加工表面质量影响很大。普通精密切削一般采用很小的背吃刀量。在高速切削条件下,背吃刀量对加工表面粗糙度的影响规律如图3所示。由图可见,两种金刚石刀具加工表面粗糙度的变化规律存在差别。随着背吃刀量的增大,聚晶金刚石刀具的加工表面粗糙度值将缓慢增大,在ap=0.025~0.10mm范围内,加工表面粗糙度值Ra≤0.1µm,可满足精密加工要求。观察表明,当背吃刀量ap≤0.025mm时,积屑瘤高度变化不大,即对加工表面粗糙度影响不大;当背吃刀量ap>0.025mm后,积屑瘤将随着ap值的增大而增大,其原因是切削温度和积屑瘤底部粘结面积发生变化造成的。由于天然金刚石刀具刃口锋利,因此可选用较小背吃刀量进行切削。由图可见,当ap由0.01mm提高到0.02mm时,加工表面粗糙度变化很小;当ap=0.03mm时,获得的加工表面粗糙度值最低;而当ap<0.005mm时,虽然切屑极薄,但加工表面并不光洁,经分析,这是因为试验使用的刀具刃口半径r较大,当切削层深度极小时,切削较困难,易发生挤刮,造成加工表面粗糙度加大。为使加工表面光洁,切削过程稳定,加工效率提高,在其它切削试验中均采用ap=0.03mm的背吃刀量。
天然金刚石刀具和聚晶金刚石刀具在v=400~1200m/min的高速切削范围内均能获得Ra<0.1µm的光洁表面;天然金刚石刀具在v=1200m/min时可获得Ra=0.05µm的高光洁表面,而聚晶金刚石刀具则具有价格较低的优势;在满足精密加工质量的前提下,对刀具材料、切削用量和切削条件均有较大选择空间。通过切削试验及分析,可得如下结论:
在高速精密切削中使用特制的乳化切削液,可使加工表面粗糙度大为改善,达到与使用润滑油进行常规精密切削相同的加工效果。
天然金刚石刀具的加工表面质量优于聚晶金刚石刀具,可使表面轮廓曲线波动的最大高度值Ry显著下降,但聚晶金刚石刀具具有成本优势,可以较好的经济效益满足高速精密切削的要求。
切削速度的选择主要受机床和工艺系统振动特性的影响,应在振动较小的转速范围内合理选用切削速度。
在一定的取值范围内(f≤0.02mm/r),进给量变化对天然金刚石刀具加工表面粗糙度的影响很小,可根据加工效益要求尽可能选择较大进给量。
天然金刚石刀具可选用相对较小的背吃刀量,但选用最小的背吃刀量并不能获得光洁度最高的加工表面,可通过切削试验确定最佳背吃刀量值。对于聚晶金刚石刀具,加工表面粗糙度值将随着背吃刀量的增大而缓慢提高,因此应尽量选用较小的背吃刀量。
声明:本网站所收集的部分公开资料来源于互联网,转载的目的在于传递更多信息及用于网络分享,并不代表本站赞同其观点和对其真实性负责,也不构成任何其他建议。本站部分作品是由网友自主投稿和发布、编辑整理上传,对此类作品本站仅提供交流平台,不为其版权负责。如果您发现网站上所用视频、图片、文字如涉及作品版权问题,请第一时间告知,我们将根据您提供的证明材料确认版权并按国家标准支付稿酬或立即删除内容,以保证您的权益!联系电话:010-58612588 或 Email:editor@mmsonline.com.cn。
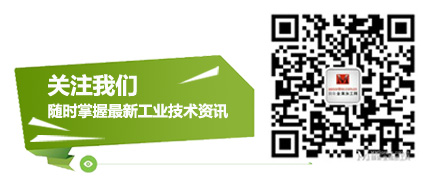
- 暂无反馈