加速导电加热切削技术的实际应用研究
1.引言
导电加热切削是一种加工机理独特的非传统切削加工方法,其刀具磨损有着与传统切削加工方法完全不同的磨损形态和磨损规律。这是由导电加热切削的加工机理和摩擦机理决定的。研究导电加热切削的刀具磨损特性以及刀具的使用性能,对于加速导电加热切削技术的实用化进程具有一定的现实意义。
2.切削试验
试验条件如下:
材料:45钢,调质;38CrNi3MoVA,调质
刀具:YG8、YT5、YT15、YW1、CN25硬质合金机夹可转位式车刀及焊接整体式车刀
电源:大功率IGBT高频逆变开关电源
试验采用常规的标准试验方法,即在车床上作外圆车削试验。切削速度选择在0.3m/s左右,在获得与高速不导电切削相同形态的切屑(带状、兰色)和相近表面粗糙度(Ra1.25~3.20μm)的工件表面的前提下,用各种型号的刀具,在不同的切削条件下进行导电加热切削,并与常规切削进行比较。
3.刀具磨损特性
众所周知,在传统切削加工中,刀具磨损一般是以机械磨损为主,佐之以扩散、氧化磨损等,刀具的磨损形态为“月牙洼”磨损。切削速度是影响刀具耐用度的最主要因素。通常提高切削速度,耐用度就降低,磨损量就增加。
导电加热切削通常是在低速下进行切削加工的,按理应有较小的磨损量。但是,导电加热切削时,必须施加较大的低压电流对切削微区进行加热,以软化工件金属材料。并且,导电加热切削是依靠刀—工紧密接触传导电流的。当电流进入切削微区,尤其是刀—工和刀—屑接触区,犹如进入一“狭窄的瓶颈”,在这里,电荷密度和电流密度都骤增,不仅接触点烧成红热,而且在接触点的气隙空间还可能产生电火花甚至电弧。这就是导电加热切削时影响刀具磨损的最本质的因素。在导电加热切削中,刀具磨损将以热电磨损、电蚀为主,而机械磨损则会因材料的软化而有所削弱。
由于热效应和电腐蚀的共同作用,这就使得刀具的磨损形态亦有所不同。研究结果表明,导电加热切削刀具的典型磨损形态为主切削刃的“刃带磨损”。
4.刀具耐用度分析
开展导电加热切削研究的国内外学者一般都得到如下结论:在一定条件下,导电加热切削能提高刀具耐用度。例如,加工钛合金时可提高1~4倍,加工镍铬合金冷硬铸铁时可提高近14倍。
事实上,只有在加热能明显地降低零件材料强度性能,而较小程度软化刀具材料的情况下,才能显著提高刀具的耐用度。
有学者指出,在保持最佳切削温度不变(用降低切削速度的方法)的条件下,加热热强合金零件既可能提高刀具耐用度,又可能降低刀具耐用度。在加工热强合金零件时,只有用相对低的切削速度加工,且切削温度接近最佳温度时,用加热方法才能达到提高刀具耐用度的目的。以等于和高于最佳速度的切削速度加工时,采用加热方法则会使切削温度偏离最佳温度,因而会降低刀具耐用度。例如,导电加热切削38CrNi3MoVA钢,在较低切削速度下,可以提高刀具耐用度4~5倍,但当切削速度大于1.8m/s时,导电加热切削并无优势,甚至会出现刀具耐用度下降的趋势。因此,导电加热切削的刀具耐用度并不总是比传统切削加工的高。
综合分析有关研究资料可知,只有在切削高强度、耐热合金、淬硬件等难加工材料,刀具—工件材料的硬度比比较小时,在一定条件下,导电加热切削的刀具耐用度才可望大幅度提高。在工件材料可切削加工性较好,刀具—工件硬度比比较大的情况下,或者切削速度较高时,导电加热切削并不产生明显效果,由于电热效应,有时刀具耐用度可能比常规切削加工还要低。
5.刀具材料的选择
只要刀—工材料的强度、硬度比大于1.4~1.5,刀具就能进行切削。但是切削刀具要能不断对加工材料进行切削,就必须保持切削刃的形状不发生改变。这主要与刀具材料和工件材料之间的强度比和硬度比有关。显然,两者比值越大,越有利于切削。
试验表明,刀具材料和工件材料的导热系数对加热切削效果有很大影响。在试验中,发现采用导热性较好的K类硬质合金刀具作导电加热切削效果较好,特别是P 类的改进型YW1刀具,具有较高的刀具耐用度,YW2基涂层刀片CN25也具有相当高的刀具耐用度。工件材料则以导热系数小些为佳,可使加热效率提高,相对刀具耐用度也有所提高(通常金属材料的导热系数的排序为:碳钢>合金结构>工具钢>耐热钢>不锈钢)。
6.刀具结构及几何参数的选择
硬质合金刀片经高温焊接以及刃磨之后,硬度有所下降,多次受热应力的作用还会发生微观裂纹,从而降低了刀具耐用度。试验表明,导电加热切削的刀具结构应采用机夹不重磨刀具为好,切削条件相同时,通常焊接整体式刀具比机夹不重磨刀具磨损量要大。
为了保证在切削过程中刀—工之间紧密接触,电流传导顺畅,避免产生电弧,减轻电蚀,在考虑刀具几何参数时:(1) 应使刀具承受一定的径向分力,主偏角应小于90°,一般以45°~75°为宜;(2) 由于工件材料受热软化,切削力减小,刀具强度已显得不是最突出的了,为了防止因切削振动等引起刀具弹回,应适当增大后角,尽量保持刀刃有一定的锋利程度; (3) 为了保证刀具有足够的强度和足够的传热体积,增大切削刃的耐磨性,提高刀具耐用度,通常应根据进给量的大小,保证切削刃有0.2~0.5mm的棱边。
7.结论
(1)导电加热切削由于刀—工和刀—屑接触区受低压大电流和高温的强烈作用,导电加热切削刀具的磨损形态和磨擦机理独特。
(2)刀具磨损程度不仅与接触应力、切削温度、连续作用时间有关,而且与切削用量和切削条件对加热电流的适应匹配有关。
(3)导电加热切削能提高刀具耐用度,这只有在切削速度较低,刀具—工件材料的强度和硬度比比较小、加热能明显降低零件材料强度性能而较小程度软化刀具材料时,才能产生明显效果。
(4)导电加热切削时,刀具材料的导热系数对刀具的耐用度影响很大。试验表明,YW类刀具较为适合导电加热切削;为了避免产生电弧,选择刀具几何参数时,既要考虑尽量保持切削刃的锋利,又要考虑使刀具在切削过程中承受一定的径向压力。
声明:本网站所收集的部分公开资料来源于互联网,转载的目的在于传递更多信息及用于网络分享,并不代表本站赞同其观点和对其真实性负责,也不构成任何其他建议。本站部分作品是由网友自主投稿和发布、编辑整理上传,对此类作品本站仅提供交流平台,不为其版权负责。如果您发现网站上所用视频、图片、文字如涉及作品版权问题,请第一时间告知,我们将根据您提供的证明材料确认版权并按国家标准支付稿酬或立即删除内容,以保证您的权益!联系电话:010-58612588 或 Email:editor@mmsonline.com.cn。
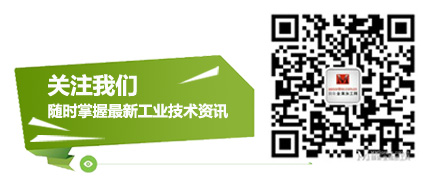
- 暂无反馈