注射模中的侧型芯与型腔的组合加工
有些塑件制品由于结构的需要常带有侧孔或侧凹,它们的轴线与注塑机开模方向垂直,不能用通常的方法实现抽芯,一般均需要采用侧向抽芯或侧向分型结构。注塑机推杆一般安装在动模一侧,所以注射模的推出机构大都设计在动模,开模后塑件留在动模。这种模具结构简单,动作稳定可靠。现以某型汽车上的卡口零件注射模设计为例,介绍这副模具的侧抽芯机构的设计,供同行参考。
塑件分析
某型汽车上带的卡口零件,材料为ABS,制件表面要求较高,产品外形较复杂,整体是一个比较大的矩形,上表面是有多个弧度的曲面,且有皮革纹修饰,下面有4个卡钩,采用斜导柱侧向抽芯机构来实现。难点在于侧抽芯机构的设计。
模具结构设计
模具整体结构。模具开模状态。
3.1 确定分型面
本设计分型面选择在塑件断面尺寸最大的部分所在平面,这样选择不影响产品的外观,有利于制品的脱模,排气效果较好,对模具的加工也较为方便。因塑件不对称,成型压力会使型芯与型腔偏移,侧向压力会使导柱导向过早失去对合精度,采用锥面定位,提高了模具的刚性。根据分型面设计原则结合本塑件特点,本模具采用的分型面。
3.2 浇注系统
为使凝料能从其中顺利拔出,主流道通常设计成圆锥形。考虑到所采用的材料ABS的流动性较好,所以取其锥角α=2°。为防止主流道与喷嘴处溢料主流道对接处应紧密对接,所以主流道对接处应加工出半圆形凹坑,其半径R2=R1+(1~2)mm,其小端直径d1=d2+(0.5~1)mm,凹坑深取h=2~5mm,在本次设计中取R2= 20mm,d1=3mm,凹坑深取h=2mm。
在保证塑料良好成型的前提下,主流道L应尽量短,否则将增多流道凝料,且增加压力损失,使塑料降温过多而影响注射成型。通常主流道长度由模板厚度确定,一般取L≤60mm,本设计采用的是L=40mm。
由于主流道与塑料熔体及喷嘴反复接触和碰撞,因此常将主流道加工成可拆卸的主流道衬套(浇口套),便于用优质钢材进行加工和热处理。本设计中采用的衬套材料为T8A钢,淬火50~55HRC。
本次设计采用的是侧浇口,尺寸为b×l×h=3mm×3mm×1mm。而且是一模一腔,所以本设计的分流道位置设在矩形框底部长度方向的中间,易取得浇注系统的平衡,分流道的截面形状为半圆形结构。
3.3 成型零件
模具成型零件由整体式凸模、局部镶嵌式凹模、两组侧抽芯,侧抽芯由斜导柱侧向机构完成。整体式凸模保证了精确的成型圆角;组合式凹模改善加工工艺性,减少热处理变形,节省优质钢材。这种局部镶嵌式凹模,除了便于加工外还使镶件磨损后更换方便。本设计先进行动模型腔的预加工,然后将四个侧型芯与动模型腔拼合,装配定位好后,再进行整体加工,最终获得要求的型腔。凹、凸模的结构。
模具工作过程
(1)动模注塑机开合模系统移动,在分型面处,动模型腔板4与定模型腔板15配合;侧型芯在斜导柱10的驱动下向动模型腔板移动,在与楔紧块17的锥面配合下与型芯精密配合,由导柱34和导套35保证闭合精度。
(2)型腔内的塑件冷却到一定温度后,由注塑机的开合模系统带动动模分型开模,当分型面打开时,由斜导柱10驱动侧型芯滑块33侧向分型抽芯,由限位块5控制侧型芯滑块的位置;与此同时,卡口零件包裹在型芯上,拉料杆27将主流道凝料从主流道衬套13中拉出,随零件和动模一起后移。
(3)当动模退到一定位置时,在注塑机的顶出装置的作用下,由推板28、推板固定板3、推杆26和拉料杆27组成的推出结构将零件及流道凝料从动模型腔板4上推出。
本模具结构方案解决了卡口类零件的成型、合模导向机构、侧抽芯机构、推出机构、排气系统、冷却系统等的设计,满足了生产该产品的质量要求和工艺要求,并针对四个卡钩巧妙地设计了要求和型腔组合加工的侧抽芯机构。本模具设计从经济、效率综合进行考虑,其结构设计简单,采用了标准模架,降低了成本,缩短模具生产制造周期,节省了产品推向市场的时间,提高了经济效益。但在设计过程中,对浇注系统和模温控制还是主要依据经验分析。
声明:本网站所收集的部分公开资料来源于互联网,转载的目的在于传递更多信息及用于网络分享,并不代表本站赞同其观点和对其真实性负责,也不构成任何其他建议。本站部分作品是由网友自主投稿和发布、编辑整理上传,对此类作品本站仅提供交流平台,不为其版权负责。如果您发现网站上所用视频、图片、文字如涉及作品版权问题,请第一时间告知,我们将根据您提供的证明材料确认版权并按国家标准支付稿酬或立即删除内容,以保证您的权益!联系电话:010-58612588 或 Email:editor@mmsonline.com.cn。
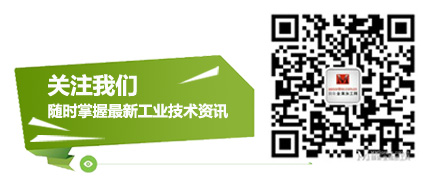
- 暂无反馈