分析:钻削奥氏体不锈钢效果及刀具涂层优化
钻削奥氏体不锈钢的效果,除了与切削刃几何形状有关外,还与刀具涂层有关。
钻头的微观几何形状显著影响钻削效果
带有各种标准横刃修磨几何形状的麻花钻即将过时,取而代之的将是具有各种不同切削刃微观几何形状的钻头。在本研究中,试验钻头的刃口倒圆半径大致在7-14μm之间,其中有3支钻头在前刀面上增加了0.1mm的倒棱。钻头刃口的倒圆采用毛刷工艺,用带有GFMMikroCAD的三维光学测量仪测量刃口的倒圆半径。试验用的钻头直径为8.5mm,带有内冷却孔。钻削速度为60m/min,进给量为每转0.1-0.25mm。在全部试验中,都使用5%乳化液作为冷却润滑液,供液压力为40bar。钻削通孔,孔长25mm,孔的长径比接近3。试件材料为最常用的奥氏体不锈钢1.4301(X5CrNi18-10)。
进给力试验结果显示,在试验的进给量范围内,最佳的切削刃刃口倒圆半径为14μm。不仅更大的刃口倒圆半径会产生更大的进给力,即使是小于14μm的刃口倒圆半径,其进给力也大于倒圆半径为14μm的钻头。此外,当刃口倒圆半径值较大时,前刀面倒棱也会导致进给力明显提高。试验还发现,切削刃微观几何形状对钻削扭矩的影响与对进给力的影响具有相似的关系,所不同的是,它对扭矩的影响要小一些。
钻削所产生的切屑形状也与切削刃微观几何形状有明显的关系,但在刚开始钻入试件阶段,所产生的切屑形状还是很相似的。当钻孔较深时,对于刃口倒圆半径较大和预先对前刀面进行了倒棱的钻头,长的和缠在一起的切屑增多了,并且这种情况在进给量较小时更为明显。具有较小的刃口倒圆半径值但未倒棱的钻头,在进给量为0.1mm时,可产生短的和不会缠在一起的切屑,从而提高了加工可靠性,因为短切屑不易堵塞钻头的容屑槽。
在加工韧性好的工件材料时,在钻孔出口处产生毛剌的情形十分常见,毛剌的大小与进给量有关。减小进给量能够在一定程度上减小毛剌高度,但是,减小进给量会导致加工时间较长和加工成本较高。试验显示,切削刃微观几何形状对毛剌高度具有显著影响。在试验的进给量范围内(0.1-0.25mm),刃口倒圆半径接近0.14μm的钻头所产生的毛剌高度最小。
涂层可显著延长钻头寿命
与未涂层的硬质合金钻头相比,采用硬质涂层能够显著提高钻头寿命。然而,在相当长的一段时期内,硬质涂层的品种曾保持相对稳定。只是到了最近几年,才开发出很多新的涂层系统。除了涂层材料不同外,涂层的结构也由单层到多层,再到纳米结构涂层,变得越来越复杂。因此,虽然预选了适合试验条件的涂层系统,但在试验中还是比较了很多涂层品种。
进行了采用各种涂层和未涂层的整体硬质合金钻头的寿命试验。试验钻头采用了相同的硬质合金基体、相同的宏观和微观几何形状,以及相同的刃口倒圆半径(14μm)。相对于未涂层钻头,两种TiN涂层钻头在耐磨性上只有较小优势。切削效果较好的是TiAlN、TiAlN+WC/C、TiCN、TiB和AlTiSiN涂层钻头,而AlCrN涂层的刀具寿命明显优于其它涂层钻头。与TiN涂层相比,在相同的切削条件和磨损带宽度(100μm)规定下,AlCrN涂层钻头的切削路程是TiN涂层钻头的3倍。此外,AlCrN涂层钻头在钻削长度达到65m后,仍可继续使用,表明该钻头应在更高切削速度下使用,从而可获得更好的经济效果,并能节约刀具和机床成本,降低加工成本。
结论
研究结果显示:①钻头切削刃的微观几何形状和涂层对加工过程及结果都有明显影响;②钻削奥氏体不锈钢时,最合适的刃口倒圆半径为14μm;③在前刀面增加倒棱的做法应该放弃;④采用AlCrN涂层可显著地提高刀具的加工效率。
声明:本网站所收集的部分公开资料来源于互联网,转载的目的在于传递更多信息及用于网络分享,并不代表本站赞同其观点和对其真实性负责,也不构成任何其他建议。本站部分作品是由网友自主投稿和发布、编辑整理上传,对此类作品本站仅提供交流平台,不为其版权负责。如果您发现网站上所用视频、图片、文字如涉及作品版权问题,请第一时间告知,我们将根据您提供的证明材料确认版权并按国家标准支付稿酬或立即删除内容,以保证您的权益!联系电话:010-58612588 或 Email:editor@mmsonline.com.cn。
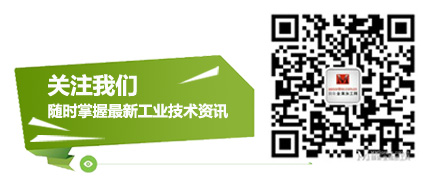
- 暂无反馈