国外新型工具系统研究状况介绍
HSK工具系统
HSK(德文Hohl Shaft Kegel缩写)刀柄是由德国阿亨工业大学机床实验室研制的一种双面夹紧刀柄,为1:10(2°51'78")锥度,采用锥面(径向)和法兰端面(轴向)双面定位和夹紧。工作时空心短锥柄与主轴锥孔能完全接触,起到定心作用,保证主轴的连接刚性。在拉紧机构作用下拉杆向右移动,此时刀柄前端锥面的弹性夹爪会径向扩张,同时夹爪的外锥面与空心短锥柄内孔的30°锥面开始接触配合。此时空心短锥柄出现弹性变形,其端面与主轴端面靠紧,消除HSK刀柄法兰盘与主轴端面问问隙(约0.1mm)。
HSK工具系统突出特征是采用端面和锥面同步接触双重定位,保证配合可靠性。类似BT锥柄,HSK的径向精度取决于锥面接触特性(二者的径向精度最高可达0.2µm)。HSK接口的轴向精度取决于接触端面,与轴向夹紧力无关,仅由结构决定,这与BT锥柄显著不同。HSK刀柄的另一个特征是为空心锥柄,以较小夹紧力产生足够弹性变形,空心薄壁的径向膨胀量保持与主轴内锥孔变形对应。空心柄部还为夹紧拉钉提供了安装位置,实现由内向外夹紧,空心柄部还可内置切削液。采用内夹紧方式可使离心力化为夹紧力,保证高速旋转的刀柄夹紧可靠性。HSK刀柄特征之三是采用1:10的小锥度叮减小锥面部分的夹紧力,提高HSK接口的承载能力,同时又能够保证锥部良好的定位作用。HSK刀柄与主轴连接结构与原理。
KM工具系统
KM刀柄是美国肯纳(Kennametal)公司在1987年开发,为1:10锥度。在夹紧机构拉杆上设有两个对称的圆弧凹槽,该槽底为两段弧形斜面。夹紧刀柄时,拉杆向右移动,钢球沿凹槽的斜面被推出,卡在刀柄上的锁紧孔斜面上。刀柄向主轴孔内拉紧后,薄肇锥柄产生弹性变形,使刀柄端面与主轴端面贴紧,实现锥面和端丽同时接触双面定位。
KM系统也是1:10中空短锥柄,采用三点接触和双钢珠锁定的方式连接,使KM系统具有刚度高、精度高、装夹快捷和维护简单等优点。
研究表明:与BT刀柄相比,HSK刀柄和KM刀柄具有更好的静刚度和动刚度。KM刀柄的拉紧力、锁紧力和动刚度值明显大于HSK刀柄,整体性能最佳,三者结构及性能比较(表略)知,KM刀柄也存在—些不足如有较大过盈量,所需的夹紧力至少是HSK的3倍。
Big-plus工具系统
Big-plus刀柄由日本大昭和精机公司(Big-Daishowa Seiki)研制,并且成功申请了专利进行技术保护,与7:24刀柄可兼容互换。Big-plus工具系统结构利用主轴内孔的弹性膨胀锁紧后补偿问隙,缩小刀柄装入主轴后与端面的间隙,保证刀柄与主轴端面配合。工作时,刀柄装入主轴后在主轴端面与刀柄法兰之间留有约0.02mm的间隙,当刀柄被拉紧后,主轴端口弹性扩张,实现锥面与端面的同时接触,避免因主轴的扩张造成刀柄的轴向移动。Big-plus系统的主轴和刀柄制造精度非常高,保证系统的整体性能,被日本高速机床厂商普遍采用。
与BT锥柄相比,Big-plus锥柄的弯矩承载能力因有一支撑直径而提高,增强了装夹稳定性。Big-plus工具系统刚性高,有衰减振动功能,在高速切削时可减少刀柄跳动,提高重复换刀精度,延长刀具的寿命,在高速加工领域可获得较高加工精度。
Showa D-F-C工具系统
Showa D-F-C刀柄是由日本圣和精机株式会社开发的,其柄部为7:24锥度圆柱形,圆柱面上配有带外锥面的锥套,锥套大端与刀柄本体的法兰端面之间设有碟形弹簧,具有缓冲吸振和双面定位效果。
刀柄采用锥套碟形弹簧的组合式结构,通过移动锥套,可以补偿锥部基准圆的微鼍轴向位置误差,能可靠的实现双向约束。当锥孔因离心力作用扩张时,在碟形弹簧的作用下,锥套产生轴向位移,补偿径向间隙,确保径向精度。碟形弹簧还能衰减切削时的微量振动,有利于提高刀具的耐用度、改善加工表面质量;该结构设计还解决了HSK、KM、Big-Plus等双面定位型结构在刀柄和主轴锥孔磨损后,锥面定位性能下降的问题。但是刀柄上锥套孔因离心力发生扩张,使Showa D-F-C柄部圆柱体出现间隙,径向刚度和径向位置精度有所下降。
Lock工具系统
Lock刀柄是日本株式会社日研工作所开发出的7:24锥度双面定位型结构。其柄部为圆柱体和圆锥体的组合,在该复合体上附带锥套,锥套大端与刀柄本体的法兰端面之间安置碟形弹簧,锥套小端通过细牙锁母定位和锁紧,Lock刀柄和BT刀柄结构区别。
Lock最大特点是用端面、锥面和锥套内孔三处锁紧,不同与两面接触高速刀柄仅端面与锥面接触,三处锁紧保证高速旋转时系统可靠性。三面定位避免因离心力导致锥套孔与柄部体产生间隙,提高系统径向刚度和径向位置精度。但3-Lock刀柄锥套有开口缝,对动平衡精度有一定影响。
工具系统动平衡精度
高速切削条件下,工具系统微小的不平衡,都可能产生很大的离心力,引起机床和工具系统的急剧振动,导致加工工件表面质量恶化甚至损坏机床主轴等部件,故需要研究制定更高的动平衡标准。
可以考虑开发在线自动动平衡装置,使工具系统具有在线自动动平衡功能,保证装配后的工具系统动平衡。研制在线故障预警功能的工具系统,使其在安装或使用中出现故障时可报警,提高安全陛。刀柄结构设计尽量采用回旋对杨睦吉构,为动平衡提供理论条件。
刀柄和主轴锥孔的配合精度
高速情况下,由于锥面存在着过盈应力,导致锥面变形严重,使工具系统的可靠性下降。刀具与主轴的联结问题影响高速切削的可靠性及机床主轴的动平衡,已成为高速切削的薄弱环节之一。
传统刀柄和主轴锥孔的配合精度比较低,无法保证工具系统定位夹持精度和换刀重复定位精度。要加强对刀柄锥孔配合精度的研究,提高工具系统的可靠性。高速切削加工(HSM)不但要求刀具本身具有良好的刚性、柔性和动平衡性,同时对其与机床主轴连接的刚性和连接精度,及保持刀具的把持力和把持精度及其各方面都提出了严格的要求。较好的刀具与机床的连接性能不仅提高加工效率,而且能提高定位精度,从而提高加工质量。
工具系统刚度和刀柄的制造精度
工具系统刚度不足会导致刀具系统振动,常规工具系统刚度和精度无法满足高速加工的要求,从而降低加工精度,并加剧刀具的磨损,降低刀具的使用寿命。高速加工的工具系统都采用过定位的接触装配方式,因此对接触配合工作表面加工精度要求很高。选用合适的材料,合理的制造工艺以及生产过程的质量监控,提高刀柄制造品质是高速加工工具系统研究中要解决的实际问题。
采用适合高速切削的刀柄,改变刀具和主轴锥孔的配合方式,在高速主轴设计中,目前对刀/轴联结研究较成功的设计主要有两种策略:—是改变7:24锥度标准采用替代型结构,如德国的HSK系列刀柄、美国的KM系列刀柄等。另一种是为降低成本,仍采用现有的7:24锥度而进行改进的刀柄结构。如美国的WSU系列刀柄,日本BIG-PLUS刀柄,3LOCK刀柄等,这种刀柄结构可改进现有结构主轴向高速化的过渡。
声明:本网站所收集的部分公开资料来源于互联网,转载的目的在于传递更多信息及用于网络分享,并不代表本站赞同其观点和对其真实性负责,也不构成任何其他建议。本站部分作品是由网友自主投稿和发布、编辑整理上传,对此类作品本站仅提供交流平台,不为其版权负责。如果您发现网站上所用视频、图片、文字如涉及作品版权问题,请第一时间告知,我们将根据您提供的证明材料确认版权并按国家标准支付稿酬或立即删除内容,以保证您的权益!联系电话:010-58612588 或 Email:editor@mmsonline.com.cn。
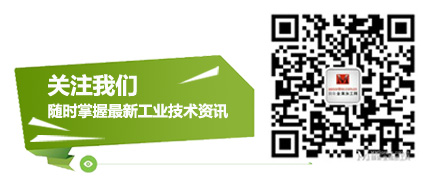
- 暂无反馈