山特维克可乐满: 最高效的硬零件车削
对材料硬度达到或超过HRC45的零件进行加工需要采用专用的磨削设备和工艺。而今天随着机床和切削刀具技术的稳步发展,为零件制造商提供了更多的新工艺方法,越来越多的制造商都在探索适合他们的新加工方案。
对于很多应用而言,相对于磨削加工,硬零件车削具有几方面的优点:一般来说,车削中心的成本低于精密磨床,并可在同一机床中加工零件的多部位,大大提高了操作的灵活性;降低了刀具库存,并且车削中心比磨床更容易与自动化系统集成。此外,车削过程产生的切屑是可以被再利用的,而磨削产生的细切屑必须被处理。磨削虽然可加工出公差在±0.005mm以内的尺寸,但硬零件车削被证明是适用于大多数其他应用的卓越工艺技术。当制造商决定从硬零件车削中获益时,应重视以下几个关键方面。
机床设计
要想成功进行硬零件的车削,机床至关重要。目前,大多数机床制造商都提供了为实现最佳加工性能而专门设计的机床模块。无论考虑新的投资机床还是改造机床,需要考虑以下几个因素:
机床底座会大大影响加工刚性,铸铁或者铸铁加强型底座可以提供最佳的稳定性。
机床的转塔结构也会影响硬零件车削。理想来说,制造商会关注转塔的刚性和集成模块化刀柄系统,这有助于通过缩短刀具悬伸来减少振动。为了优化其性能,集成模块化刀柄系统应该是圆周各向夹紧,而不是紧靠两个螺钉来夹紧。
最后,根据加工零件的规格,需要慎重考虑投资带尾座的机床。因为零件悬伸超过四倍直径(从卡盘处算起),一般必须使用尾座,以获得一致性和稳定性。
“软状态”准备
在考虑硬零件车削应用时,零件的“软状态准备”对总体加工的成功有着巨大影响。要想获得一致的“输出”需要使用一致的“输入”。在淬硬前,零件余量要均匀。各加工厂往往只注重最终成品的质量,而忽视了这一关键因素。结果由于切削深度的变化使刀具受到不同切削条件的影响,从而直接影响到切削质量、刀具寿命和生产效率。在硬零件车削中,去除0.0008英寸或0.0012英寸的材料都会对刀具施加很大的外力,从而损害整体的加工稳定性。这同样适用于材料的硬度,硬度为58HRC的零件与硬度为62HRC零件的加工要求是不同的。虽然对于成品零件这些变量是可以接受的,但是出于对加工效率和效用的考虑,还是应尽量避免这些情况。
除了确保各零件的材料和尺寸的一致性外,制造商还应寻找更好的设计方法来准备要硬化的零件。如果可能的话,任何孔、键槽和沟槽都应做倒角加工。这样就可以在断续切削时通过平稳的进入和退出刀具来减少刀具和加工过程中的冲击应力。
刀片的选择
刀片选择是硬零件车削配刀时首先考虑的因素之一。硬质合金刀片可以加工硬度为40HRC-50HRC的材料并具有很好的性能,是低硬度范围材料的不错选择。
常见的硬度范围在50HRC-55HRC的材料包括含碳量低的低碳钢。这类材料一般都是表面淬硬,因此,要求刀具具有很高的抗月牙洼磨损性。陶瓷刀片是这类应用的出色选择。
硬度超过55HRC包括表面硬化钢和大多数整体淬火钢在内的材料,都需要特别的抗后刀面磨损性。CBN(立方氮化硼)在这类型材料的粗加工和精加工方面表现突出。人类已知的第二大最硬材料——立方氮化硼具有优异的耐磨损性,并且能够应对高切削温度所产生的不利影响。
对于硬度高于HRC55的材料,确定采用含多少碳含量的CBN非常重要。含碳量高的材料磨蚀性就很强,那么刀片的材料成分应该是立方氮化硼含量更高,陶瓷粘合料含量较低——这可以最大限度地减少刀片的后刀面磨损,但需要采用较低的切削速度,约400英尺/分钟,以避免产生月牙洼磨损。相反,对碳含量低的材料而言,后刀面磨损不是大问题,可以考虑使用陶瓷粘结剂高抗月牙洼磨损更好的CBN刀片,其速度范围通常在600英尺/分钟。
除了材料的碳含量外,零件设计也会影响到CBN刀片的选择。对于长时间连续切削的零件加工场合,通常使用CBN含量约40%左右的刀片。对于断续切削不严重的加工场合,如已经做了倒角的孔或键槽,50%-60%的CBN含量可以将韧性提高到所需的水平,同时仍具有很好的耐磨性。对于断续切削很严重的加工场合,须采用70%-75%CBN含量的刀片,以达到所需刃线的韧性要求,从而满足加工应用的需要。
刃口处理也会影响到硬零件车削的加工工艺。不同工况下,刀片需要的刃口处理的角度就不同。不同的角度和刃带宽度带来不同的刃口处理。T-形刃口是最常见的,使用圆角来分散刃口处集中切削力。S-形刃口与T-形刃口相似,但刀刃经过磨削,在此处刃带角和刀片表面可以接触,从而提高了耐磨性。使用E-land槽型,无需进行磨削,但刀片是有15?m–20?m研磨刃带,保护刀片不会崩刃。
最后,采用Wiper(修光刃)槽形的刀片可大大提高加工质量和生产效率。一般而言,Wiper(修光刃)槽形和标准的刀尖半径相比,Wiper可以在两倍进给率下获得同样的表面光洁度。相反,使用Wiper修光刃槽形并保持相同的进给率可达到更高的表面光洁度。这是因为Wiper(修光刃)槽形作用在刀片上的切削力分布比较大。
编程考虑因素
外圆车削时(O.D.),中心高至关重要,尤其是较小的零件。保持中心高在0.002英寸以内,再大就会极大地影响加工质量。内圆镗削时,其定位取决于刀具悬伸量。镗杆设置略高于其中心会有利于加工,这样切削力靠近中心,而不是将其推离最佳位置。
如果可能的话,最好将刀具正面朝上固定在机床上。这将使切削压力回到机床上,从而在加工过程中减少振动和增加刚性,实现更好的加工质量。
编程员必须考虑:硬零件车削是采取1次切削还是2次切削策略。在高品质的机床和正确的配刀情况下,通常1次切削即可完成合格的加工形状和表面质量。当发生最常见的异常情况时,不管是硬度还是形状,热处理过程都会使零件变形。在此情况下,很可能需要采取2次切削策略,以确保高质量的加工结果。
监控刀具磨损
所有刀片最终都会出现磨损形式,因此,注意观察这些磨损形式可以了解如何优化切削过程。当采用陶瓷或CBN刀片进行硬零件车削时,容易发生月牙洼磨损,如果磨损过快,就可能需要降低切削速度,或换成CBN含量较低更耐磨的刀片。在硬零件车削中,后刀面磨损也是常见的问题,通常表明需要降低切削速度。如果刀片出现沟槽磨损,通常会发生在切深处,改变主偏角可以减少影响,而且能使切屑更薄。
使用瑞士纵切机床进行硬零件切削
虽然迄今为止硬零件车削已广泛应用于汽车业和通用机械的零件加工,但越来越多的工厂使用瑞士纵切机床来加工医疗产品零件。制造商面对前述所有因素挑战时应做更多的考虑。虽然CBN刀片在这类应用中具有良好的精加工表现,但刀具寿命在很大程度上取决于所用的切削液的类型。大多数瑞士纵切机床配有油基的冷却液系统,致使大量热量被滞留在切削区。由于硬零件车削中会产生高温,水溶性冷却液系统具有更优异的冷却效果,并提高了刀具寿命和生产效率。
专家知识的价值
硬零件车削为今天的制造商提供了非常明显的优势,无需安装专业化的机器设备,大大提高了加工灵活性并实现了最大的生产效率。文中前述的各种问题是涉足该领域的制造商们都要面对的最常见的问题。但是,卓越的专家知识是无可取代的。机床制造商和刀具供应商都拥有庞大的工程师团队,针对各种零件的加工工艺进行优化攻关。不管是第一次进行硬零件车削还是仅仅希望从现有工艺中获得更多改进,向专家们咨询总会让您获益颇丰。
声明:本网站所收集的部分公开资料来源于互联网,转载的目的在于传递更多信息及用于网络分享,并不代表本站赞同其观点和对其真实性负责,也不构成任何其他建议。本站部分作品是由网友自主投稿和发布、编辑整理上传,对此类作品本站仅提供交流平台,不为其版权负责。如果您发现网站上所用视频、图片、文字如涉及作品版权问题,请第一时间告知,我们将根据您提供的证明材料确认版权并按国家标准支付稿酬或立即删除内容,以保证您的权益!联系电话:010-58612588 或 Email:editor@mmsonline.com.cn。
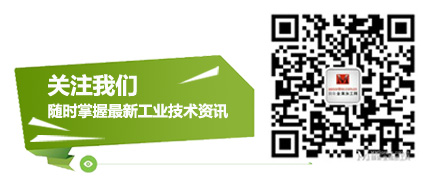
- 暂无反馈