使五轴联动加工变得简捷
对于采用多轴机床的模具制造商来说,开发能充分发挥这些机床能力的CNC程序堪称难题。其目的就是以最有效的方式充分利用机床附加轴的移动(工作台或刀架),同时使模具具有良好的表面光洁度。
近年来,机床的同步移动愈加复杂,也使CAM软件系统在数学和技术方面均面临难题。加工技术的飞速发展,使可用于运行机床的高效NC程序的同步开发变得困难。
另外,为多轴机床而设计的软件产品必须易于使用,并能纠错。由于用于这些先进机床的材料、高精度刀具和附件成本非常昂贵,因此极微小的编程错误也会造成重大损失。
基于这些前提,CAM软件开发商所面临的难题是如何将这些强大的编程功能与容易被用户所理解的编程过程结合在一起。必须明确地阐述这些功能,才能引导用户完成编程过程,从而避免在确定刀具轨迹时产生误差。同时,不会使编程过程变得僵化或具有局限性。
旧式思维
为了能向用户提供多种加工方案,CAM软件开发商总是将四轴、五轴加工分解成各种可用于各种刀具轨迹的专用功能。事实上,一些CAM开发商正是以他们能提供多种专用功能而感到自豪。
开发该类型软件的代价,是使该系统的功能变得令人难以理解。典型的终端用户只能了解并利用有限的功能。业务繁忙的CNC程序员不可能记住CAM系统的众多功能的用途,因此他们通常只根据自己最熟悉的功能进行编程,而忽视了其它功能。
四个经过简化的步骤
关于先进加工功能的新理念均基于一种观点,即任何五轴加工功能(无论多么复杂),都可以用几个简单步骤进行界定。模具制造商采取了屡试不爽的方法设置模具生产程序:
(1)需要加工的区域及加工顺序。这一步骤以部件外形的复杂程度为依据,往往最容易激发技术娴熟的机械师所具有的灵感。
(2)加工区域中刀具轨迹应具有怎样的形状?是否应使刀具根据表面的参数化线条,按前后或上下顺序进行切削,并将表面边界作为引导呢?
(3)如何引导刀具轴,使与刀具轨迹相吻合?这一点对于表面光洁度的质量,以及是否在狭小的空间内采用较短的硬质刀具非常重要。模具制造商需要充分地控制刀具,包括刀具倾斜时产生的前后倾角。此外,必须考虑许多机床的工作台或刀架在旋转时产生的角限位。例如,铣削/车削机床的旋转程度就存在限度。
(4)如何转换刀具的切削路径?如何在刀具轨迹的起始点,控制刀具由于复位或产生的位移以及刀具必须在加工区域之间产生的位移?转换过程产生的位移在模具生产中非常关键,它可以消除证示线以及刀具产生的痕迹(可通过此后的手动抛光将其清除)。
如果机械师能遵循经过严格定义的步骤,为什么不开发一款采用同样步骤的CNC程序呢?
新思路
沿袭机械师在决定对复杂部件进行五轴加工时的想法,是一个更好的开发CAM软件的方法。为什么要将五轴加工功能分解,而不是为程序员开发一种熟悉且易于理解的、单一的编程过程?
这种先进技术将消除强大的功能和易用性之间的矛盾。通过将多轴加工方法简化成一种独特的功能,可使用户很快就能熟练地充分利用产品的所有功能。CAM具有这种新功能后,可使五轴加工具有最大限度的灵活性和紧凑性。
符合您意愿的编程过程
用户可根据专门为多轴加工技术设计的单一功能,并结合现有方案,为自己定制刀具轨迹。换句话说,用户只要从现有的加工模式任意选择一种,并选择一种刀具定位策略,就可以用多种方式加工部件。
例如,如果多轴加工功能可提供用于控制刀具轴的5种不同加工模式、4种不同的策略,则用户就有20种加工部件的方法。如果再加上对主轴和五轴刀具轨迹的锁定能力,这种能力可迅速转化为4+1用途,为用户提供多种方案,从而开发复杂度高,而局限性很小的五轴功能。
为了进一步简化,软件界面只应显示适合当前工况的选项。例如,若用户选定一个参数加工模式,则应立即选择与刀具相符合的驱动面和参数化的流向。如果用户决定修改一种简单的边界抵消模式,则界面可经过更新减少显示的选项数量。
由于用户选择加工方案,因此需要立即更新软件界面,从而引导用户合理选择编程过程。这种分步指导方式可帮助用户在确定刀具轨迹时避免出现错误,且不造成局限性。若用户决定修改以前的方案,该系统可做出响应,并提供一套新选项。
将各个要素联系在一起
为了尽可能得到最光滑的表面,刀具从进料时的第一个刀路的终点向下一个刀路的起点移动时,需要精度和控制。对于进料过程中这些环节,应允许采用多种方案,并采用精度类似艺术家的切削刀具。大多数CAM系统提供多种连接选项,这样程序员就可以在下一个合乎逻辑的步骤中选择最优和次优方案。通过这种方式,若首选的连接方法不能采用(由于检测到刀具发生碰撞及超过角限位的误差等),则该系统可采用由用户选定的第二种连接方法。
例如,用户可以优先考虑某种连接方法,从而自始至终将刀具置于部件表面上。但若此方法不可行,则系统会查看用户的选项清单,从而选择第二种方案。用户在采用次优方案时,如果刀具需要离开加工面,然后又要沿与下一个切口呈切线的方向进行径向移动,从而返回加工面时,就可选择采用径向移动的环节。
通过这种方式,用户可对连接方法设置优先级,从而减少加工操作的失误,或避免由于刀具复位时移动不当产生的刀具重叠。当刀具需要从一个位置迅速移动至另一个位置时,该技术同样适用于退刀运动。模具在生产过程中遇到的障碍,都必须避免。而通过为系统提供连接方法清单,无需采用猜测方式,就可确定刀具到达及与部件分离的最佳方式。
基于要素的五轴铣削
除了紧凑和经过简化的铣削功能外, CAM系统还必须能简化用户选择加工区域的方法。对于用于标准铣削操作的CAM系统来说,凹槽和孔洞等是常见的可加工要素。然而,复杂的铣削过程中却很少存在这些要素。
一种新型的自由曲面特征,使用户可选择并保存单一对象的加工面以及在加工时需要避开的表面。由于各类表面需要采用不同的加工策略,因此可以为单一的零件模型生成任意数量的自由曲面特征。这样,用户就可以选择某个单一要素,对预先确定的区域进行加工。
设计概念的一致性和易用性需要进行扩展,才能使同一个界面用于自由曲面特征和五轴铣削功能。这样,用户无须打开和退出多个对话框,就可在熟悉的环境进行加工。
为未来开辟道路
从软件开发商的角度来看,开发一种单一的铣削功能可满足模具制造商现有的需求。而在今后,对于为多轴加工创建刀具轨迹这一过程的每个步骤,都需要进行深入分析。此外,还需要将车间日常生产中采用的各类多轴机床和机床生产商开发的新技术,与工作中的实践经验结合起来。
通过这种深入分析可以得出如下结论——具有适用性的多轴铣削功能必须由分散的组件构成。这些组件无论单独使用还是组合在一起,均能发挥优异性能。必须对这些组件进行分析和测试,以保证任何组件在任何加工步骤中均具有完全互换性。
这项分析工作本身,可使开发出的软件具有很高的可靠性,这最终使用户受益。由于每个组件只创建一次,因此软件也具有高效率——消除了在将先进功能分解为一系列加工功能时产生的冗余性。
该类功能的优势在于,随着今后多轴机床技术的发展,可随时将新的加工方式和刀具定位策略添加到该软件。这种思维标志着CAM软件开发已脱离了传统思路,从而使CAM系统可轻易地与模具制造领域中迅速发展的技术保持一致。
声明:本网站所收集的部分公开资料来源于互联网,转载的目的在于传递更多信息及用于网络分享,并不代表本站赞同其观点和对其真实性负责,也不构成任何其他建议。本站部分作品是由网友自主投稿和发布、编辑整理上传,对此类作品本站仅提供交流平台,不为其版权负责。如果您发现网站上所用视频、图片、文字如涉及作品版权问题,请第一时间告知,我们将根据您提供的证明材料确认版权并按国家标准支付稿酬或立即删除内容,以保证您的权益!联系电话:010-58612588 或 Email:editor@mmsonline.com.cn。
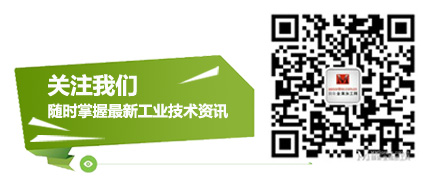
- 暂无反馈