淬硬钢孔加工用钻头
随着立方氮化硼材料和优质现代陶瓷刀片的开发应用,淬硬材料的加工能实现以车代磨、以铣代磨。铣削是断续切削,以铣代磨除用CBN和陶瓷刀片外,强韧性好的超微粒硬质合金再加表面涂覆高红硬性优质涂层的刀具也能胜任加工淬硬钢材。本文介绍了三菱公司开发的MHS型淬硬模具钢孔加工用整体硬质合金钻头。
国际生产工程研究学会(CIRP)曾有研究报告指出:“由于刀具材料的改进,刀具切削速度每隔10年提高1倍。而由于刀具结构和几何参数的改进,刀具寿命每隔10年,几乎平均提高2倍。”在新材料研制的基础上,新的刀具结构能发挥更大的功效。刀具结构设计由于空间曲面形状纷繁,各种截面、尺寸、三维角度等处理难度大,计算和表达非常复杂。近年来由于CAE和CAD技术的不断发展,可以切实找出切削时应力、应变、温度分布场分布,以合理设计结构,但是这样求出的结构形状往往很复杂,难以制作实现。但近年来CAM技术、模具制造技术、粉末冶金技术、五轴联动加工、刃磨技术等进步很快,以前难以实现的,现在实现起来比较容易。
近10年来模具工业迅速发展,作为它的使用材料,对于模具钢一般先进行其上的导柱孔、注射孔、冷却水孔及型腔的初步切削加工,然后再进行热处理,热处理工序往往会使加工面和零件产生变形,变形部位需通过磨削等高成本、低效率的方法进行精加工,以达到图纸要求。如果能用钻淬硬模具钢的钻头,加工己淬硬型腔的立铣刀,则工序可以简化为先热处理,后钻孔、铣型腔,达到最终加工要求。这样可大大缩短工艺流程、提高生产效率。
传统麻花钻的缺点
钻孔一般采用麻花钻,为了能在淬硬钢上钻出孔,首先必须要对传统麻花钻的结构、形状进行改进。传统麻花钻的缺点为:
(1)在实体材料上钻孔会产生大量切屑,为排出切屑,钻头必须有螺旋槽,而螺旋槽会削弱钻头的强度。为保证钻头必要的强度以使钻芯有足够厚度支撑钻头工作,槽不能做得太深、太宽,这样在钻头前端必然出现一定宽度的横刃,旧麻花钻横刃处的前角约为-50°。横刃处不能正常切削,而能刮擦、挤压工件,因而产生很大的轴向力。淬硬钢强度、硬度高,所造成的轴向力更高,极难钻入。
(2)由于螺旋槽面构成了主刀刃的前刀面,故主刀刃各处的前角是不同的。旧麻花钻在钻头外圆处前角约为30°,很锋利但刀刃强度很低,易损伤;而接近横刃处,前角约为-30°,切削性能很差,消耗切削动力大。其间各点除前角外,各处切削速度也不同,生成及排除切屑的条件和状态均不相同。
(3)钻头钻入后,为保证孔的直线度,提高孔的表面粗糙度水平和加工稳定性,除靠自身刚性外,主要依靠2条刃带构成的副刀刃的支托导向。但由于刃带的宽度很小,支托导向作用显得很不足,只有足够坚实的支托和导向,才能保证孔的加工精度,提高生产稳定性和钻头寿命。
MHS系列钻头的改进与创新
三菱研制的MHS系列钻头在结构上的改进与创新有:
(1)对钻头顶部进行X形修磨,使横刃长度为0,并将构成钻头后刀面的顶面磨成三重后刀面,从而使钻入时的定心和磨损后的重磨很方便。短孔可直接钻入;深孔可先用短钻头钻出1D(钻头直径)孔深作为导孔,再用长钻头钻出。
(2)改进主刀刃和螺旋槽面,将主刀刃近钻芯处设计为凹刃,使原来形成负前角处达到正前角,从而提高了该处的切削锋利性和切除切屑的性能;将主刀刃近外圆处设计成凸刃,使正前角减少,从而提高了该处的切刃强度。主刀刃变成凹凸刃后,前刀面(螺旋槽面)构成复杂的波浪型面,提高了排屑性能。
(3)钻头芯厚比一般钻头粗,刚性高。
(4)螺旋角比一般钻头小,螺旋角越小,抗扭转的强度越高。
(5)与2个刃带成90°,两侧制成宽而厚的导向部分。钻削时由不稳定的2窄刃带支撑变成稳定的4面支撑。设置导向结构的优点是:
·可承受径向切削力,使支承稳定,抑制振动;加工孔直线精度高,表面粗糙度值低。
·加工稳定,孔径尺寸波动小,刀具寿命长。
·可进行断续切削。
·可钻深孔。带导向块结构优点很多,早已被各大刀具公司采用,如德国MAPAL的带导块精密镗刀、精密铰刀,MILLER的钻头,BOTEK的深孔钻,三菱以往的超级辊光钻头等。
基于上述结构特点,MHS系列钻头在承受轴向力时,对压杆稳定失效的抵抗能力比以往产品增强37%。
MHS系列钻头加工实例
MHS系列钻头与三菱WSTAR系列所用材料一样,母体为超微粒硬质合金TF15,外表涂层为用先进MIRACLE技术沉积的(Al,Ti)N,材料牌号为VP15TF,如图2所示。最适合钻削硬度为HRC35~55的材料。
1 高品质加工实例
(1) 造成钻孔尺寸差、精度不高的主要原因为:钻头抖动造成孔的扩大,扩大量超过孔允许的最大值,即为不合格品。故应控制扩大量,可控制扩大量越小,钻头加工精度越高。MHS系列钻头通过结构改进,导向性好,刚性高,切削性能好,以图3为例,孔加工扩大量小,达到7级精度。这相当于一般钻孔后再加一道初铰工序。本例加工孔的长径比L/D=70/5=14。
·切削条件。工件材料:DH31S(合金工具钢);硬度:HRC48~50;钻头:MHS0500L090B(φ5mm);加工孔深:70mm;切削速度:20m/min;每转进给量:0.15mm/r(一次进给);进给速度:191mm/min;冷却方式:水溶性切削液;切削液供给压力:2MPa(内部冷却);使用机床:立式加工中心。
·导孔切削条件。钻头:MHS0500L020B(φ5mm);加工孔深:5mm;切削速度:20m/min;每转进给量:0.15mm/r。
(2)钻孔后,表面粗糙度是加工品质评定标准之一。由于结构改进,振动得到抑制,导向结构对加工壁面尚有一定挤压辊光作用。以图4为例,加工后表面粗糙度值为1.743μm,此值一般需钻后再经初铰和精铰才能达到。
· 切削条件。工件材料:SKD11;硬度:HRC48~50;钻头:MHS0500L120B(φ5mm);加工孔深:100mm(通孔);切削速度:20m/min;每转进给量:0.10mm/r(一次进给);进给速度:127mm/min;冷却方式:水溶性切削液;切削液供给压力:2MPa(内部冷却);使用机床:立式加工中心。
·导孔切削条件。钻头:MHS0500L020B(φ5mm);加工孔深:5mm;切削速度:20m/min;每转进给量:0.10mm/r。
2 高速高效加工实例
本例工件材料硬度HRC40,虽较前面2例低,但以前面2例2~4倍的切削速度高效加工,在不同进给量条件下,取得满意的结果。图5为实摄其切屑图。切屑生成形态良好,可稳定高效切削。
· 切削条件。工件材料:CENA1(塑料成型用模具钢);硬度:HRC40;钻头:MHS0600L150B(φ6mm);加工孔深:115mm;切削速度:60m/min;每转进给量:0.15mm/r(一次进给);进给速度:477mm/min;冷却方式:水溶性切削液;切削液供给压力:2MPa(内部冷却);使用机床:立式加工中心。
·导孔切削条件。钻头:MHS0600L030B(φ6mm);加工孔深:6mm;切削速度:60m/min;每转进给量:0.15mm/r。
3 MHS系列钻头加工不同工件材料切削性能实例
这里按硬度由低到高描述各类材料的加工结果。钻头的磨钝标准一般按后刀面VB值来衡量,通常VB值设定为0.2~0.3mm。磨损达到此高度后,不应继续使用,必须重磨。在各示例中,还显示了不同切削速度和进给量条件下切屑形态、动力波形变化和刀刃磨损情况。
(1)铬合金不锈钢STAVX(HRC33)实例
在本例切削条件下,加工到180个孔后,VB值仅达到0.05mm,仅为规定值的1/4,故可加工多个孔后重磨。为此时主后面、前刀面、副后面的磨损状况,由图可知能持续使用。
·切削条件。工件材料:STAVAX(铬合金不锈钢);硬度:HRC33;钻头:MHS0600L150B(φ6mm);加工孔深:115mm(通孔);冷却方式:水溶性切削液;切削液供给压力:2MPa(内部冷却)。
·寿命试验条件。切削速度:40m/min;每转进给量:0.15mm/r(一次进给);进给速度:318mm/min。
·导孔切削条件。钻头:MHS0600L030B(φ6mm);加工孔深: 6mm;切削速度:40m/min;每转进给量:0.15mm/r。
(2)压铸模具钢DAC55(HRC45)实例。
在本例切削条件下,加工到120个孔后,VB值仅达到0.1mm,为规定值的1/2,尚可继续加工。
·切削条件。工件材料:DAC55(压铸模具钢);硬度:HRC45;钻头:MHS0600L150B(φ6mm);加工孔深:115mm;冷却方式:水溶性切削液;切削液供给压力:2MPa(内部冷却)。
·寿命试验条件。切削速度:30m/min;每转进给量:0.10mm/r(一次进给);进给速度:159mm/min。
·导孔切削条件。钻头:MHS0600L030B(φ6mm);加工孔深:6mm;切削速度:30m/min;每转进给量:0.1mm/r。
(3)合金工具钢DH313(HRC50)实例。
本例工件材料硬度较高,达HRC50,故钻头磨损较上2例快。加工100个孔后已达到磨钝标准,重磨后才能继续加工。但这样高的硬度,能加工到100个孔已属不易。另外,加工到100个孔时,右切削刃虽出现较大磨损,但切削动力波形始终稳定。说明切削过程是稳定的。
· 切削条件。工件材料:DH31S(合金工具钢);硬度:HRC50;钻头:MHS0500L090B(φ5mm);加工孔深:70mm;切削速度:20m/min;每转进给量:0.15mm/r(一次进给);进给速度:191mm/min;冷却方式:水溶性切削液;切削液供给压力:2MPa(内部冷却);使用机床:立式加工中心。
·导孔切削条件。钻头:MHS0500L020B(φ5mm);加工孔深:5mm;切削速度:20m/min;进给量:0.15mm/r。
(4) 模具钢SKD11(HRC55)。
本示例工件材料硬度高达HRC55,一般专为加工淬硬钢开发的钻头约可钻5个孔,MHS钻头可加工20个孔。照片显示钻完5个孔后,MHS型钻头磨损很少,可继续加工。
· 切削条件。工件材料:SKD11;硬度:HRC55;钻头:MHS0600L120B(φ6mm);加工孔深:95mm;切削速度:20m/min;每转进给量:0.05mm/r(一次进给);进给速度:53mm/min;冷却方式:水溶性切削液;切削液供给压力:2MPa(内部冷却);使用机床:立式加工中心。
·导孔切削条件。钻头:MHS0600L030B(φ6mm);加工孔深:6mm;切削速度:20m/min;每转进给量:0.05mm/r。
声明:本网站所收集的部分公开资料来源于互联网,转载的目的在于传递更多信息及用于网络分享,并不代表本站赞同其观点和对其真实性负责,也不构成任何其他建议。本站部分作品是由网友自主投稿和发布、编辑整理上传,对此类作品本站仅提供交流平台,不为其版权负责。如果您发现网站上所用视频、图片、文字如涉及作品版权问题,请第一时间告知,我们将根据您提供的证明材料确认版权并按国家标准支付稿酬或立即删除内容,以保证您的权益!联系电话:010-58612588 或 Email:editor@mmsonline.com.cn。
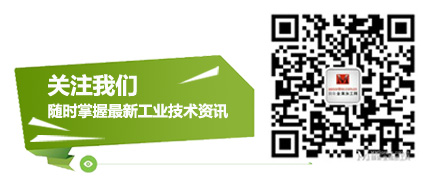
- 暂无反馈