中国数控产业的惟一出路是自主创新
中国数控行业发展大致经历三个阶段:第一阶段是封闭式发展阶段;第二阶段是引进技术,消化吸收,初步建立起产业体系阶段;第三阶段是实施产业化工程,进入市场竞争阶段。
对于数控系统而言,没有创新,就没有出路。惨痛的历史教训说明一个硬道理:数控系统这样的战略高技术,靠花钱引进根本办不到,盲目效仿国外,也只会落后挨打,受制于人。中国数控产业的惟一出路,就是走自主创新之路,用中国人自己的核心技术振兴中国数控产业。
目前国产经济型数控系统基本适应中国市场需求,可靠性得到了提高,功能实用,价格低廉,有很大的竞争优势,得到了广大用户的认同。目前约占到我国整个数控系统市场的60%左右。
2006年,我国经济型数控系统产量达到6万多套,市场占有率高达95%以上。外国公司也推出了几款低价格的经济型数控系统,但价格上、服务上还是没有优势,市场推广竞争不过国产系统。
目前,行业主导企业普及型数控系统已实现批量生产,在数控铣床、加工中心等中档数控机床得到批量配套应用,销售到最终用户后,反映良好,而且,已经具备全数字交流伺服驱动系统和主轴伺服驱动系统等配套能力。
从技术水平上比较,国产普及型数控系统的功能、性能与国外比并不差,价格和服务方面还有较大优势,可靠性与国外系统的差距也已显著缩小。但外国品牌依然占领国内市场。分析成因:
一是用户对国产品牌认同度低,表现为普及型数控系统市场主要被国外占领。2006年国产普及型数控系统在中国已销售约7000套,占市场份额约17%,国外的普及型数控系统在中国销售约35000套,占市场份额约83%。
二是生产工艺管理技术、生产检测手段、可靠性考核手段、质量控制等规模化生产技术比国外落后,影响产品的可靠性、质量的稳定性,表现为前期故障率较高,前期磨合周期较长。
也就是说,国产高档数控系统技术有了突破,但与国外产品相比,差距仍然较大,主要体现在:一是功能差距,功能还不够完善,在实际应用中验证还不全面;二是性能差距,在高速(快速进给速度40米/分以上)、高精(分辨率0.1微米以下)、多通道控制、双轴同步控制方面,国外系统采用运动控制总线技术适应高速高精加工,而国内企业以模拟量或脉冲量接口居多;三是产品的系列化差距,如伺服电机、伺服驱动、主轴及主轴驱动从小到大各种规格不全;四是电主轴、直线电动机、力矩电动机等功能部件方面也有很大差距。
市场方面的差距主要体现在:2006年,国外公司在中国销售高档数控系统约2000台,约占市场份额的99.5%,而国产高档数控系统只销售了十多台,约占市场份额的0.5%。由于受到西方出口许可限制的约束,中国市场销售的绝大部分高档数控系统是西门子的840D产品。
按分析,未来数控系统技术的发展趋势是:运行高速化,加工高精化,功能复合化,控制智能化,体系开放化,驱动并联化,交互网络化。由此来看,国内数控系统发展战略应为:稳住经济型系统市场,努力提升技术;大力推动中档系统实现产业化,努力提升市场占有率;重点开发高档数控系统,实现技术突破和产业化;加强技术路线创新,发展成套中高档数控系统等。
声明:本网站所收集的部分公开资料来源于互联网,转载的目的在于传递更多信息及用于网络分享,并不代表本站赞同其观点和对其真实性负责,也不构成任何其他建议。本站部分作品是由网友自主投稿和发布、编辑整理上传,对此类作品本站仅提供交流平台,不为其版权负责。如果您发现网站上所用视频、图片、文字如涉及作品版权问题,请第一时间告知,我们将根据您提供的证明材料确认版权并按国家标准支付稿酬或立即删除内容,以保证您的权益!联系电话:010-58612588 或 Email:editor@mmsonline.com.cn。
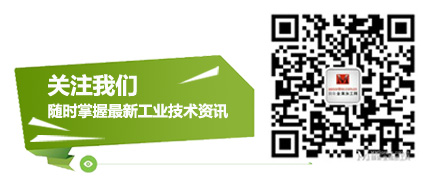
- 暂无反馈