达诺巴特研发白皮书 | 第三部:磨削,还是硬车削?
磨削还是硬车削
选择并不像您认为的那么简单
决定使用磨削还是硬车削来完成工件加工可能很困难,通常不能靠直觉。这两种工艺都能达到极高的公差和表面粗糙度。最高效的选择取决于工件特征、材料、批量大小、设备产能以及其他几个因素。
磨削,还是硬车削
在决定使用车削还是磨削来完成工件加工时,旧的计算法则是,硬车削性价比更高,但如果对尺寸公差和表面粗糙度要求很高,则只能选择磨削。
在当今的车削和磨削技术面前,这些假设都是错误的。使用合适的机床,硬车削可以为70HRC的材料(包括硬质合金)提供极高的公差和表面粗糙度。但在许多情况下,磨削可能仍然是性价比更高的选择。这完全取决于工件配置、材料、设备产能、批量大小以及其他几个因素。
旗下拥有达诺巴特、OVERBECK和汉布雷格公司,达诺巴特在制造精密磨床和精密硬车床领域拥有超过70年的经验。设计者对这两种技术并无偏见,他们表示,在所有给定的应用中,没有硬性规定来快速确定哪种工艺更可靠、性价比更高。但是一些通用观点可以帮助应用程序工程师开始朝着正确的方向思考。下面将概述这两种工艺。
基本信息
首先,我们应该对硬车床进行区分。硬车削可以在各种标准车床上完成,但与磨削相比,它们通常只能进行粗加工。然而,达诺巴特汉布雷格公司生产的精密硬车床精度更高,精度范围在亚微米级,表面粗糙度为0.1-0.4微米Ra,对55-70 HRC的材料进行单点车削加工。这是一种简单可靠的工艺,具有许多优点,特别是对复杂形状和内外径相结合的工件进行多表面加工时。
内径和外径磨削、无心磨削以及具备车削和磨削功能的复合机床仍然占有重要地位。达诺巴特制造所有这些机床,能够很好地判断哪种工艺能够为哪种特定应用提供最高效的选择。
一般而言,下列情况下,硬车削最具优势
圆形工件具有复杂的几何形状,和/或需要内径/外径组合加工
高混合/低容量环境需要频繁的机床设置
可能进行空转
磨削仍然是加工以下工件的最佳选择
薄壁和/或高长径比
强干涉表面
长时间运行的工件要求工艺高度一致
工件形状不能转动
硬车削的固有优势在于它是一个更简单、更灵活的工艺。从设置和工艺管理的角度来看,它与传统车床几乎没什么不同—易于编程和方便更换单点刀具。成本大幅降低,特别是对以前需要车削和精磨的工件。
磨削的主要优势在于它是一个更稳定的工艺。砂轮性能在其整个生命周期内保持不变,在线测量可以确保在生产加工过程中达到很高的Cpk值。虽然单点车削刀具可能容易更换,但加工硬质材料时磨损速度更快,而且整体刀具的成本通常会随着磨削加工而降低。圆柱磨削可能是非平衡或非圆工件的唯一选择。
下面将对每个工艺进行更多介绍:
硬车削
为什么几乎所有的机床都不能进行精密硬车削?材料越硬,切割工件所需的力度就越大,更大的切削力会对导轨施加更大的反推力。
传统数控车床根本无法承受这种更大的切屑力,从而导致形状精度不够,表面粗糙度差,刀具磨损增加。真正的精密硬车床将提供持续的高工件精度(亚微米)和更长的刀具寿命。
汉布雷格通过几个关键的机床部件解决了这些需求。硬车床的底座由天然花岗岩制成,在硬度、热稳定性和减振能力方面优于铸铁。机床配备静压导轨,各轴浮在加压油膜上。无需表面与表面接触,导轨可以无摩擦、无磨损地运行,对硬车削极为重要,能够进一步增强机床的抗振能力。这使得汉布雷格机床能够达到0.5-1微米的形状精度、0.15微米Ra的表面粗糙度和≤ 1微米的尺寸精度。
这些功能使得机床能够对精密部件进行精密硬车削,例如:
滚珠丝杠螺母
轴承环和滚柱轴承
液压部件
驱动轴和齿轮
各种模具&冲模组件
工件通常采用硬车削的方式加工以下材料,如淬硬轴承钢、高速钢、模具钢、渗碳钢、碳化合金和舶来航空航天材料,如铬镍铁合金。
磨削
对于各种形式的圆柱磨削,一个明显的争论是使用超精密工件。极其精确的磨削工艺可达到0.5-1微米的形状精度,≤1微米的尺寸精度,0.1微米Ra的表面粗糙度。但磨削只适用于高端工件的观念是完全错误的,磨削很可能是各种应用中的低成本选择。
部分原因是,磨床通过配置能够生产几乎所有特征的工件,包括一些不能在车床上生产的工件。磨床为圆形工件的配置包括:
万能磨床(内径/外径)
无论您想要一台仅加工外径、内径或内外径都加工的机床,都有多种磨床可供选择。内径/外径磨床提供极大的柔性,可生产各种圆形或其他形状的工件。在某些应用中,剥皮式磨削(使用窄砂轮磨削工件)在某些应用中能够与单点硬车削的效率相媲美。
无心磨床
虽然无心磨床已经存在了大约一百年,它仍然是各种轴磨削应用的最高效选择。许多人倾向于认为无心磨削主要是为了加工简单的圆柱形状,如磨棒料。无心磨床确实擅长这个,但也可以定制为精磨多特征工件的磨床。
令人惊讶的是,尽管金刚石和CBN砂轮可能非常昂贵,磨削加工的刀具成本通常都比较低。在一些常见的情况下,一个砂轮在需要更换之前能够加工的工件多达20万甚至50万个。即使砂轮成本很高,平均到每个工件才不到一美分。而且不只是刀具成本,耐磨性更好的砂轮减少了工艺的可变性和更换刀具的需求,提高了机床的利用率和产量。
选择哪种工艺加工工件?
如果有一套明确的标准来确定工件应该是精密车削还是磨削是非常理想的。不过事情从来都没有那么简单,在得出最终解决方案之前需要考虑很多变量,而且往往会得出与直觉相反的结论。对这两种工艺都有丰富经验的供应商能够提供公正的建议,与他们合作很有帮助。下面几个应用就能说明这一点。
此锥形轴承内圈(图1)由硬度为60 HRC的100Cr6钢制成。基于之前的工艺,制造商希望减少工艺步骤,减少节拍时间,提高产品质量。新工艺中,外径为330 mm(约13英寸),对轴承内圈的外径和内径都进行车削和表面处理。精密硬车削工艺能够将内径同心度和锥度保持在<3微米,壁厚<3微米,锥形角度为±20弧秒。12分钟内完成加工。
此锥形轴承内圈(图2)由磨床加工。有着相似的降低成本和改善质量的目标,该内圈材料是硬度为62HRC的100Cr6钢。72.72 mm(2.863英寸)的外径和法兰经过粗磨和精磨,圆度< 2微米,Ra < 0.4微米。节拍时间只有90秒。
这两个案例,工艺设计良好,但对加工的最佳技术却得出了不同的结论。决定工件需要哪种技术进行加工时,与具备相关知识的专家合作,让其帮助指明方向是非常有用的。如开头所说,决策取决于多种因素,即使对经验丰富的制造工程师而言,也可能无法轻易地给出解决方案。达诺巴特的独特优势能够提供帮助,既制造精密磨床,又制造世界上最精确的精密硬车床,能够毫无偏向地处理应用问题。
更多信息,请访问Danobat.com
长按上方二维码下载白皮书
达诺巴特DANOBAT专门为汽车、航空航天、铁路和能源等高要求行业制造机床、提供高附加值零部件制造解决方案、交钥匙生产系统和先进的服务。
隶属于达诺巴特集团,达诺巴特在西班牙、德国、荷兰、意大利、英国和美国设有生产工厂和服务中心,以及一个覆盖40个国家的重要销售和服务网络。
(达诺巴特集团)
声明:本网站所收集的部分公开资料来源于互联网,转载的目的在于传递更多信息及用于网络分享,并不代表本站赞同其观点和对其真实性负责,也不构成任何其他建议。本站部分作品是由网友自主投稿和发布、编辑整理上传,对此类作品本站仅提供交流平台,不为其版权负责。如果您发现网站上所用视频、图片、文字如涉及作品版权问题,请第一时间告知,我们将根据您提供的证明材料确认版权并按国家标准支付稿酬或立即删除内容,以保证您的权益!联系电话:010-58612588 或 Email:editor@mmsonline.com.cn。
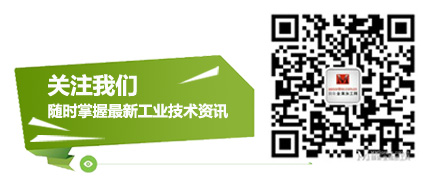
- 暂无反馈