宝马集团正在朝着增材制造的系统集成迈出下一步
宝马集团正在朝着增材制造的系统集成迈出下一步。目的是将增材制造规模扩大到工业水平,并在各个领域(主要是汽车研发和生产)中牢固地建立基础,以产生积极的经济效果。宝马集团充分受益于该技术的优势,该技术提供了快速的组件可用性,灵活的组件设计以及无需复杂工具即可制造零件的能力。
宝马集团生产集成和试点工厂高级副总裁DanielSchfer表示:“增材制造等流程帮助我们加快了开发周期,并使我们的车辆更快地达到系列成熟度。3D打印还能在满足严格的质量要求的同时缩短组件的生产时间。”
小批量生产的3D打印组件
自今年年中以来,宝马集团一直在为劳斯莱斯汽车增材制造金属和聚合物零件。它们是在流程链中的各个点以及全球生产网络中的不同地点制造的。
有关的部件用于车身和乘客舱,并且功能强大且坚固。宝马集团在公司自己的增材制造园区开发并制造了用于汽车生产的工艺,该工厂还通过多喷射熔合和选择性激光烧结生产聚合物零件。
目前,宝马集团工厂的兰茨胡特金属零件是通过激光束熔化制成的。在生产中,金属3D打印的组件几乎以完全自动化的过程安装到车身上。汽车中安装了来自增材制造园区的聚合物组件和装饰板的金属基材。
通过生成设计进行组件开发
在车辆开发的早期阶段就确定了增材制造可用于零件生产的程度。工程师以及生产和材料专家检查了数百个组件,重点关注新技术的经济利益以及与传统制造零件相比的重量和几何形状优势。根据一系列标准和要求选择了用于3D打印的组件,并在数据科学家的帮助下将其定义并翻译为“机器语言”。这标志着新AI系统的开始,使宝马集团能够更快,更早地确定3D打印可以生产哪些零部件。
以前几乎不可能实现的零件是通过生成设计进行工程设计的,该设计使用计算机算法进行快速组件开发。专家和计算机共同创造出可以在生产中充分利用材料的零件。得益于生成设计,许多潜在的应用才有可能实现,而3D打印技术特别适合于创建其复杂的形状和结构,而这些是以前用常规工具无法生产的。
对于宝马集团而言,生成设计产生了拓扑优化的解决方案,其形式和功能得到了显着增强。这些组件比同类的传统组件轻约50%,并且可以充分利用可用空间,例如后盖的阻尼器。
增材制造园区
自六月以来,宝马集团已将其全部技术专长集中在慕尼黑郊外的增材制造园区。新校园还为来自世界各地的员工提供使用新技术的培训,并且是原型零件生产的所在地。目前,卓越中心拥有多达80名员工,并且已经在运营约50个金属和聚合物加工系统。另外有50多个系统正在全球其他生产基地运行。
(白令三维)
声明:本网站所收集的部分公开资料来源于互联网,转载的目的在于传递更多信息及用于网络分享,并不代表本站赞同其观点和对其真实性负责,也不构成任何其他建议。本站部分作品是由网友自主投稿和发布、编辑整理上传,对此类作品本站仅提供交流平台,不为其版权负责。如果您发现网站上所用视频、图片、文字如涉及作品版权问题,请第一时间告知,我们将根据您提供的证明材料确认版权并按国家标准支付稿酬或立即删除内容,以保证您的权益!联系电话:010-58612588 或 Email:editor@mmsonline.com.cn。
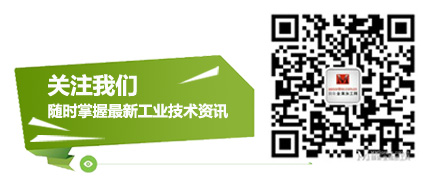
- 暂无反馈