增材和减材过程组合用于混合加工
过去几个月里,我一直在关注增材制造(AM)行业的定向能量沉积技术(DED),对这项技术增材制造分层部件所展示出来的速度相当满意。不足的是尺寸精确度,无论是采用粉末进料还是电线进料,经过定向能量沉积技术(DED)过程所生产出来的形状并没有达到很完美的水平,仍然需要进行额外的精整和后处理,才能满足规定公差。粉末床熔融工艺(PBF)制造出来的部件也是如此。但是,采用粉末床熔融工艺(PBF)制造出来的增材制造部件形状与定向能量沉积技术(DED)相比更接近完美水平,后期精整和处理工作量更小。尽管如此,鲜少能够做到一步到位。
大多数情况下,增材制造部件的精整和后处理都是在另外一台设备上完成的。通过定向能量沉积技术(或粉末床熔融工艺)系统生产出来的部件转移到计算机数控系统(铣床或机床)上,进行后续加工和精整。可以想象一下,确定部件方向和位置的基准点、参考点以及定义部件在计算机数控机器上的刀具路径难度有多大,尤其是部件与制造盘分开的情况。设计师和工程师可以在部件上标注出定位特征和参考点,帮助确定部件方向和加工的基准点。
同时,制造业也正在向增材和减材工艺与单一系统集成的方向发展,比如混合制造。此外,市场上也推出了几款商业系统。例如,DMG MORI将定向能量沉积技术(DED)(粉末进给和激光)与五轴计算机数控机床的能力集成到了混合制造系统中。此外,Matsuura和Sodick也正在通过不同的途径,将粉末床熔融工艺和计算机数控能力集成到公司的混合制造系统中。DMG MORI正式向公众介绍了他们的粉末床熔融工艺和计算机数控混合制造系统。当然,如果客户也可以选择Hybrid Manufacturing Technologies公司推出的Ambit粉末进料激光沉积头对现有的计算机数控加工中心进行改造,或使用3D混合技术,将粉末和电线进料能力与贵公司的计算机数控机器组合在一起。通过以上方式,可以以相对更低的成本和精力,将普通的减材系统改造为混合制造系统。
幸运的是,在Penn State的金属增材制造实验室CIMP-3D中安装了DMG MORI的Lastertec 65混合制造系统。这套系统优于实验室的所有设备,以激光为基础的粉末进料系统产生的光斑大小为1.5mm或3mm,1h内便可完成10~15lb材料的沉积处理。同时,用户可以利用五轴计算机数控系统的能力对沉积的材料进行加工,或者在沉积过程中,促使材料朝向不同方向。通过这种方式,省去了支撑结构,在最大移动和旋转幅度范围内实现了更复杂的几何形状。通过喷嘴,客户可以看到部件制造期间的材料增减过程(如图)。系统搭配了双粉末进料器,确保客户在材料沉积期间,通过更改材料组分对部件进行功能性定级。
图中所示喷嘴显示了混合制造系统如何通过增材和材料加工来满足规范要求
除了混合制造系统中增材和减材制造的强大组合外,大家还需要进一步学习这项技术。举个例子,怎样才是最理想的材料增加和减少顺序?刀具路径规划软件会否在增加部件特征后进行减材特征冲突检测?此外,应当如何在增加新材料,加热部件促使部件发生形变时保持机加工表面的尺寸完整性?减材期间,当使同用切割液不断冲洗部件,应选择哪种切割液来确保新增加的特征可以迅速冷却;加热/冷却循环会对部件的微结构和机械特性造成什么影响?最后,各个方向上的粉末捕获率为多少?是否会随着部件围绕五轴中的一根轴旋转时发生改变?粉末捕获和重新利用的程度如何?显然,使用冷却液冲洗工件外表面后是不会再回收粉末的。
目前,有很多专业人士和对增材制造感兴趣的人们正在学习增材制造在金属加工领域的细节之处,但是如何将增材和减材,以优化混合制造过程。二者结合后产生的效果远远超过任何一项技术,但是我们却从未探索过这个混合制造业的新领域。
声明:本网站所收集的部分公开资料来源于互联网,转载的目的在于传递更多信息及用于网络分享,并不代表本站赞同其观点和对其真实性负责,也不构成任何其他建议。本站部分作品是由网友自主投稿和发布、编辑整理上传,对此类作品本站仅提供交流平台,不为其版权负责。如果您发现网站上所用视频、图片、文字如涉及作品版权问题,请第一时间告知,我们将根据您提供的证明材料确认版权并按国家标准支付稿酬或立即删除内容,以保证您的权益!联系电话:010-58612588 或 Email:editor@mmsonline.com.cn。
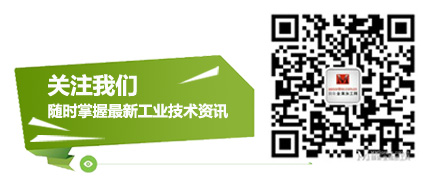
- 暂无反馈