3D打印的汽车车灯
作为工业4.0时代的一大标志,3D打印技术的快速发展必将为汽车制造业的发展提供更好的助力。当前3D打印技术在汽车行业中的应用已经不再局限于简单的概念模型设计,正朝着更多的功能零部件方向发展,渗透到汽车零部件的各个领域。例如汽车格栅、汽车仪表盘、空调管路、进气歧管、发动机罩、装饰件、车灯等都已经采用3D打印技术进行研发生产试制。
汽车零部件的研发往往需要长时间的验证工作。传统的流程是先进行零部件设计,然后开发制作模具,再制造出零部件的实体并对零部件实体进行测试以确定是否能够达到产品设计要求,如不满足要求还需对设计或模具进行修正。这一流程耗时长、成本高。
将3D打印技术应用到汽车零部件研发过程中则可快速对复杂零部件的工作原理和可行性进行验证,不但省去了模具开发的工序,还可减少时间和资金的投入。传统汽车零部件的研发周期通常在45天以上,而3D打印只要1-7天即可完成零部件的开发验证过程,可大大提高新产品的研发效率。而且3D打印开发零部件的流程中不需要模具,可节约大量的成本。
目前汽车应用市场中,采用联泰科技3D打印技术的汽车品牌厂商有大众、丰田、江铃、江淮、比亚迪、奇瑞等,而专门采用联泰科技3D打印技术的车灯厂家有:浙江天翀车灯集团有限公司、吉林市瑞宝车灯有限公司、天津市汽车灯厂等等。今天小编要分享的是汽车领域其中一个细分应用,3D打印汽车车灯。
车灯是车辆的照明工具,按功能可以分为照明灯和信号灯两种,车灯在车辆安全行驶的过程中起了重要的作用。汽车大灯是属于汽车外部照明灯,在汽车制造业中至关重要,对于材料的要求是像大多数导光源一样,必须是高度透明的,并且在道路上让驾驶者在很远的地方就可以清晰可见,其灯罩部件的材料透明度要求较高,联泰科技光固化高透明3D打印材料刚好可以满足汽车车灯的高透明要求,经过后处理抛光,效果可以媲美PMMA材料,适用于外观验证、装配验证。另外,光敏树脂材料的特殊性,还适用于喷涂、电镀工艺,用于汽车大灯内部的组件。
在研发试制过程中采用3D打印技术的优势是,省去了传统汽车研发试制过程中的开模工序,一部到位的实现产品的外观结构和纹路等细节,满足产品外观验证、装配验证,简化制造流程,降低劳动强度,可以说3D打印为汽车车灯的试制提供了最完美的解决方案。
汽车的研发周期较长,但是面对汽车市场的激烈竞争,这么长的时间可能会对汽车制造企业造成巨大的危害。因此,各大车企都在想方设法缩短汽车研发周期。汽车的研发周期长,其根本原因在于汽车零部件的加工制造周期较长,且汽车零部件前期的设计开发成本高昂。这些不足都限制了汽车工业的发展。3D打印技术的优势可以令汽车研发试制摆脱了传统制造对模具的依赖,这些优点在对汽车行业有着十分重要的作用,同时让3D打印技术在汽车制造行业的应用越发的广泛。
声明:本网站所收集的部分公开资料来源于互联网,转载的目的在于传递更多信息及用于网络分享,并不代表本站赞同其观点和对其真实性负责,也不构成任何其他建议。本站部分作品是由网友自主投稿和发布、编辑整理上传,对此类作品本站仅提供交流平台,不为其版权负责。如果您发现网站上所用视频、图片、文字如涉及作品版权问题,请第一时间告知,我们将根据您提供的证明材料确认版权并按国家标准支付稿酬或立即删除内容,以保证您的权益!联系电话:010-58612588 或 Email:editor@mmsonline.com.cn。
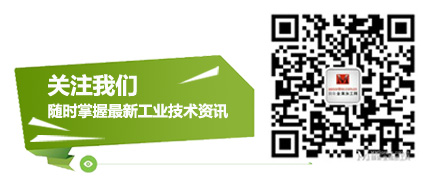
- 暂无反馈