应用案例一汽大众:3D打印风道试制件将成本降至10%
汽车行业是3D打印技术最早的应用领域之一,近年来,许多前沿汽车制造企业已经将3D打印技术应用于汽车研发过程。一汽-大众汽车有限公司(以下简称一汽大众)于1991年2月6日成立,是我国第一个按经济规模起步建设的现代化乘用车企业,已拥有长春、西南、华南、青岛和天津五大基地。
2017年,一汽大众实现了累计生产整车1500万辆、年产整车突破198万辆,全年终端销量实现200万辆,强势引领中国汽车市场。
早在2005年,一汽大众长春开发部便引进3D打印技术,将其应用于所有新车研发中,制作3D打印原型件、展示件、试验零件等,如今每年3D打印汽车零部件达5000件左右。
一汽大众长春开发部高级试制工程师吴宏涛介绍,与传统注塑工艺及其他3D打印技术相比起来,采用PLS技术(Plastic Laser Sintering,选择性激光烧结)制作的样件具有良好的强度和优异的抗冲击性能,并且能够实现快速修改设计方案并反复大量迭代,在确保原型产品设计质量的同时,大大缩短了产品设计和原型开发所需的时间,提高了研发效率。
1降低研发成本,缩短开发周期
2017年,一汽大众在原有FDM、SLA技术的基础上,引进PLS技术——
每周开机频率:4次
每批打印样件:≥40件
样件良品率:≥99%
每年耗费材料:800公斤
一汽大众长春开发部每年耗费华曙高科3300PA材料大约800公斤,且基本没有浪费,极大地节省了使用成本。
图为一汽大众的3D打印样件工作包。
采用3D打印技术在汽车塑料件的开发过程中,极大地缩短了零件的试制周期,使得零件研发周期大大缩短。同时,3D打印在制造汽车改装部件上变得更加快速、灵活和经济,尤其是针对客户的个性化需求来说。
相比之下,传统的注射成型工艺就显得"臃肿"了许多,因为它不但需要开发额外的工具,而且会造成大量的材料浪费和库存堆积。
图为3D打印汽车后排吹脚风道样件
以后排吹脚风道为例,不同制作方式时间对比如下:
后排吹脚风道不同制作方式成本对比如下:
数据来源:一汽大众长春开发部
当小批量样件试制时,采用3D打印技术,相比传统的硅胶模工艺,汽车后排吹脚风道样件加工周期缩短95%,节省成本88%,并且能够实现快速修改设计方案并反复大量迭代,在确保原型产品设计质量的同时,大大缩短了产品设计和原型开发所需的时间,提高了研发效率。
2适合制作受力结构件
"理论上,整车的塑料零部件都可以采用3D打印制作,这取决于样件使用环境和标准。我们会根据具体情况,选择合适的3D打印工艺。"吴宏涛介绍。
以汽车保险杠导向支架为例,在使用PLS技术之前,一汽大众采用传统硅胶模具浇注双组分材料制件,零件耐冲击强度差,在装车的时候经常发生卡扣破碎,这成为了困扰工程师的一个难题,如采用SLA技术,则必须经过硅胶模工艺进行二次转换,才能达到抗冲击强度标准和耐温要求。
图为汽车保险杠导向支架设计图
与传统注塑工艺及其他3D打印技术相比起来,华曙高科PLS解决方案具有不可替代的优势,其成型件对环境(温度、湿度和化学腐蚀)的抵抗能力类似于热塑性材料,具有良好的强度和优异的抗冲击性能,非常适合制作需要装车受力的结构件。
小结
目前,汽车行业由于自身规模大、研发投入多、应用3D打印技术时间长等因素,在3D打印技术应用中占据重要位置,其巨大的市场规模为3D打印技术的应用提供了广阔的市场空间。我们相信,在未来,3D打印将在材料性能、成本方面达到直接制造的要求,向具有更高价值的应用转变。
声明:本网站所收集的部分公开资料来源于互联网,转载的目的在于传递更多信息及用于网络分享,并不代表本站赞同其观点和对其真实性负责,也不构成任何其他建议。本站部分作品是由网友自主投稿和发布、编辑整理上传,对此类作品本站仅提供交流平台,不为其版权负责。如果您发现网站上所用视频、图片、文字如涉及作品版权问题,请第一时间告知,我们将根据您提供的证明材料确认版权并按国家标准支付稿酬或立即删除内容,以保证您的权益!联系电话:010-58612588 或 Email:editor@mmsonline.com.cn。
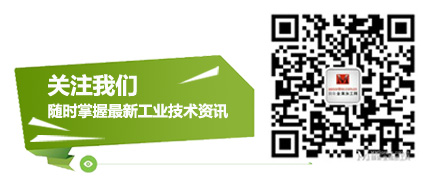
- 暂无反馈