3D打印造7米机身: 我国战略高超音速飞行器曝光, 或反超美国
据南极熊3D打印网6月2日报道,近期中国3D打印又获得重大突破,中国精合集团使用采用激光沉积制造技术、特种连接技术、新型去应力技术、先进扫描技术等高科技手段,成功制造出某超高速飞行器长达7米的复杂机身框梁。制造时间从传统的2年缩短到6个月。同时这也是世界最大的、使用3D打印技术制造的机身框梁。
据介绍,该金属框梁一体化飞行器主体结构总长度7XXXmm,宽度2XXXmm,高度1XXXmm。从外形上看,这一机身框架采用翼身融合体结构,中间似乎能看到大型圆形开口,可以推测这可能是一种单发动机超高速飞行器。而按照结构总长度7XXXmm,宽度2XXXmm来推算,这种飞行器最后实体长度可能会超过十米,翼展将超过4米。
据推测这可能是我方在研的一种速度超过5马赫的高超音速无人战略侦察机,可携带高速机载雷达实现战略监视和侦察。目前军事强国在高超音速领域竞争非常激烈。美国已经在开发速度为6马赫的SR-72无人战略侦察机。而我国研发超高速飞行器机身框梁,明显也是类似装备。而且超长复杂机身框梁,由于成本原因,不会应用于一次性的高超音速弹头或者巡航导弹领域,只能是侦察或者打击平台。
即2012年北京航空航天大学教授为歼-20研制钛合金大型复杂整体构件激光成形技术曝光后,我国先进飞行器采用高效3D打印技术的例子就越来越多,也成为先进制造领域军民融合的典范。王华明的激光3D打印技术已经应用于歼-20等7种飞机、3种导弹、2种卫星、3种航空发动机和1型燃气轮机等型号。而精合集团同样也是这方面的优秀代表。该公司拥有大量的先进的激光金属3D打印设备,其中自主研发了世界最大的TSC-S4510型同轴送粉金属3D打印设备。
从第一张图我们可以看出,这个结构总长度超过7米的超高速飞行器复杂机身框梁,就是通过TSC-S4510设备打印出来大型部件,然后又通过特种连接技术来拼接而成。而据精合集团透露,研制世界最大的TSC-S4510设备,就是为了配合国家战略研发产品,能弥补国内超大锻造设备的制造能力不足。而且更惊人的是,精合集团透露通过7米并不是上限,通过特种连接技术、新型去应力技术,可以实现几十米飞机框梁一体化制造,而变形能控制在0.5毫米以内。这就等于为3D打印从“打部件”到“打整机”奠定了基础。
3D打印等先进制造技术的出现,是航空先进制造领域名副其实的“游戏规则改变者”。这种技术成本低、周期短、敏捷制造、性能优异的特点,成为先进航空航天制造生产率的颠覆性跃升的强大动力。因此我国在这一领域的后发优势,必然给美国造成巨大的压力。精合集团已经透露,这次7米长度钛合金飞行器主承力结构件的成功生产,为制造超大型航空航天复杂结构件打下了坚实的基础。也许我国的高超音速无人侦察机,将比美国的SR-72更早露面!
声明:本网站所收集的部分公开资料来源于互联网,转载的目的在于传递更多信息及用于网络分享,并不代表本站赞同其观点和对其真实性负责,也不构成任何其他建议。本站部分作品是由网友自主投稿和发布、编辑整理上传,对此类作品本站仅提供交流平台,不为其版权负责。如果您发现网站上所用视频、图片、文字如涉及作品版权问题,请第一时间告知,我们将根据您提供的证明材料确认版权并按国家标准支付稿酬或立即删除内容,以保证您的权益!联系电话:010-58612588 或 Email:editor@mmsonline.com.cn。
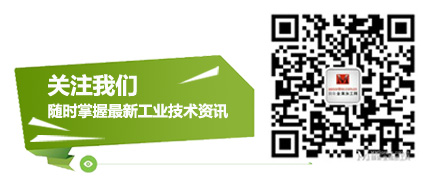
- 暂无反馈