深孔加工振动断屑装置设计
1 、引言
深孔加工在封闭或半封闭的空间内进行,产生大量切屑在一定的空间内易形成堵塞,切削热不易传递出去,其加工难度高、排屑难且工作量大。BTA 深孔钻排屑的主要动力是由高压油提供的压力,如果切屑过长,即使在高压油的作用下仍然难以排出。为解决深孔加工过程中排屑难的问题,通过分析振动切削原理、设计振动断屑装置、给刀具施加轴向周期振动,实现钻头瞬时切削厚度的改变和钻头轴向振动,从而有效控制切屑的形态,使切屑顺利排出,提高高速深孔加工的效率。
2 、振动钻削机理分析
振动钻削的基本原理是通过振动装置施加给刀具或工件一定方向、一定频率和一定振幅的可控振动,使钻头和工件之间产生规律性的接触和分离,从而使普通钻削变成间歇式钻削。针对不同的振动方向将振动钻削分为三类(见图1) ,其中,轴向振动方向与钻头的轴线方向一致,扭转振动方向与钻头的旋转方向一致,复合振动是轴向振动与扭转振动的相互叠加。由于轴向振动比较容易实现且加工效果较好,因此应用最广,其钻削机理见图2。
图1 振动钻削类别
图2 轴向振动钻削机理
振动钻削是间歇性切削,钻削过程中钻头在极短的时间进行切削,其余时间钻头与工件都处于分离状态; 钻头间歇式的切削使之获得极大的瞬时速度和瞬时加速度,对被加工工件形成冲击,使塑性金属脆性化,同时降低摩擦系数和切削力,进而提高钻头的相对刚度。在振动钻削过程中,由于钻头和工件间的接触是间歇式的,因此振动钻削产生的切削热少且散热快; 振动钻削可以使切削力降低,并在一定程度上避免刀瘤的产生,提高加工工件的表面质量。
3、 振动装置建模及分析
在设计机械式振动钻削的振动装置时,一般采用偏心机构、四连杆机构和曲柄滑块机构等,综合分析深孔加工的特点,拟采用偏心凸轮结构来建立模型。偏心式振动机构建模的基本原理见图3。
图3 偏心凸轮机构
根据式( 6) 绘出如图 4 所示的断屑区域图。
图4 切削区域图
4 、振动断屑装置设计
4. 1 振动发生装置设计
振动钻削装置中必不可少的是振动发生器,其结构设计如图 5 所示。由图可知,内凸轮与转轴采用紧配合的方式连接在一起,当转轴转动时,内凸轮随之转动; 为了实现振动振幅的调节,需要使内凸轮和外凸轮之间可以转动,则外凸轮与内凸轮之间的配合方式为可动连接; 螺母可用来控制外凸轮与内凸轮之间何时可相对转动,即当螺母松开时,外凸轮与内凸轮可以相互转动。
图 5 振动发生器简图
图6 相对位置关系简图
4. 2 振动断屑装置整体设计
振动断屑装置整体结构见图 7。由于钻杆的不稳定性,振动发生装置不容易固定,可将振动直接加载到联结器上。为了使联结器沿直线运动,设计安装小导轨,其配合结构见图 8。
图7 振动断削装置原理图
图8 小导轨与联结器配合关系图
为防止联结器与小导轨脱离,设计安装导轨挡于小导轨后端,可避免联轴器掉落; 通过弹簧支柱把弹簧固定在弹簧挡板与联结器之间,且弹簧处于压缩状态,其弹力足以推动联结器移动。振动发生器的两端支撑在拖板上,当凸轮转动时,便会推动联结器与钻杆一起移动。振动断屑装置的特点包括: ①振动发生器可通过电机直接控制,则其振动频率可通过调节电机的转速实现控制; ②通过调节内外偏心轮的相对位置,可连续调节振幅大小,适应性强;③应用小导轨可保证钻杆沿直线运动,从而保证了直线度; ④结构紧凑,易于安装与操作,寿命长,性能稳定。
5 、振动断屑装置实验分析
通过实验探究振动参数与深孔加工中切削参数的关系。实验设备包括: Z8Q16 卧式深孔钻床、冷却系统、振 动 装 置、授 油 器、内 排 屑 深 孔 钻 ( 8 ×500mm) 。实验工件为 EA4T 车轴钢,尺寸 30 ×300mm。实验参数: 振动装置振幅 A = 0. 08mm,机床转速 n = 785r/min,油压 3MPa。5. 1 断屑实验分析通过分析断屑情况可知,振动钻削产生的切屑与普通钻削产生的切屑不同,普通钻削所产生的切屑是厚度一致的带状切屑,而振动切屑所产生的切削的形态是随振动频率变化而变化。不同切削条件下振动断屑的情况见表 1。
表 1 不同条件下切削断屑情况
通过实验分析不同振动参数下的切削形态,可得频转比 f/n 与切削形态关系如图 9 所示。由图可见,振动断屑装置有良好的断屑效果,可以有效控制切屑形态。这种短小的切屑在高压切削液作用下能够顺利排出,从而有效解决 BTA 深孔系统排屑难的问题。其特点为: ①形成瞬时切削厚度的改变有利于断屑。当钻头振动切削时,由于钻头振动的作用,切屑受到随振动变化而变化的切削力,表现出切屑厚度变化的特征。在高压切削液的作用下,厚度不同的切屑在其薄弱处发生折断,达到断屑的目的。②形成钻头轴向的振动有利于断屑。由于钻头在切削时进给量很小,所以轴向振动的振幅 2A 较易大于进给量,此时可实现分离切削,达到断屑的目的。
图9 2A/fr= 5.5时,不同f/ n的切削形状
5. 2 加工精度分析
通过实验分析振动装置对孔加工质量的影响。通过仪器检测可得普通切削和振动切削时的成孔精度(见表2) 。
表 2 普通切削与振动切削成孔精度
通过对表 2 的分析可知,在其他加工参数相同时,振动切削能有效提高成孔质量,通过调节振动参数可以降低孔表面粗糙度,提高孔尺寸精度。分析其原因为:
(1) 在振动钻削时,由于钻头切削扭矩变小,对成孔表面质量有积极作用。在振动切削的过程中,钻头在一瞬间内完成微量切削,使扭矩和切削强度相应降低,从而有利于改善表面加工质量。
(2) 在振动钻削时,由于对切屑形态的控制使排屑更加流畅,对成孔表面质量有积极作用。振动切削可以使切屑变小,小的切屑在高压切削液作用下顺利排出,从而减小切屑对已加工表面的影响,避免打刀,提高刀具寿命。因此,振动切削可提高加工精度。
(3) 在振动钻削时,可以对积屑瘤形成一定的抑制,所以对成孔表面质量有积极作用。普通切削会在切削区域内产生很大的挤压力,在挤压力作用下,随着加工材料塑性变形会产生大量的切削热,使切屑与刀具形成积屑瘤。积屑瘤对加工稳定性和刀具寿命都有不利影响,而且不利于保证成孔质量。振动切削过程中,由于钻头的振动使切削为间歇性切削,所以会使加工材料塑性化,使其塑性变形减小,减少积屑瘤的形成,达到抑制积屑瘤的目的。此外,由于振动切削的间歇性作用,切削时的润滑和冷却都会得到改善,积屑瘤的形成进一步得到抑制。
(4) 在振动钻削时,由于切削液能更好地作用于切削,对孔表面质量有积极作用。在振动切削过程中,切削液在切削间隙能迅速进入切削区域,从而改善切削环境,接触面之间的摩擦随之降低,提高成孔表面的质量。
6、 结语
本文研究了振动钻削原理,设计了振动断屑装置应用于深孔加工。振动断屑装置能有效地控制BTA 深孔钻削加工时对切屑的控制,对深孔加工中切削形态控制和成孔质量具有积极作用。通过理论分析和实验分析探讨了振动钻削断屑装置在深孔加工领域的可行性,为高速高效深孔加工技术的发展提供了一种可行性方案。
声明:本网站所收集的部分公开资料来源于互联网,转载的目的在于传递更多信息及用于网络分享,并不代表本站赞同其观点和对其真实性负责,也不构成任何其他建议。本站部分作品是由网友自主投稿和发布、编辑整理上传,对此类作品本站仅提供交流平台,不为其版权负责。如果您发现网站上所用视频、图片、文字如涉及作品版权问题,请第一时间告知,我们将根据您提供的证明材料确认版权并按国家标准支付稿酬或立即删除内容,以保证您的权益!联系电话:010-58612588 或 Email:editor@mmsonline.com.cn。
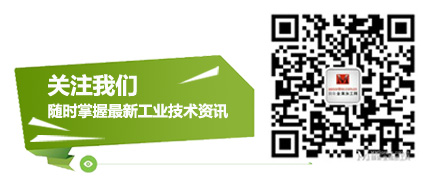
- 暂无反馈