通过金属3D打印可以制造更好的液压零件
液压系统可以作为动力传动方式,也可用作控制方式,在工业领域中的应用非常广泛,例如机床、工程机械、农业机械、汽车、飞机等机械,水利工程用的堤坝装置,发电厂发电厂涡轮机调速装置,以及军事工业中火炮操纵装置等领域都会应用到液压系统。
市场研究机构InfiniumGlobalResearch预测从2017到2023,3D打印市场将保持33%左右的年复合增长率,而在业界人士看来,液压零件的3D打印将成为一个不可忽视的3D打印应用增长领域。
3D打印技术已成为多家液压系统制造商制造复杂液压零部件的选择,例如,工程和制造公司穆格MOOG,在金属3D打印液压零件领域的有着超过16年的探索经验,2017年另一家液压传动和控制领域的著名制造商派克汉尼汾(ParkerHannifin)在总部附近开设了“先进制造学习和开发中心”,工程师可以在该中心探索增材制造/3D打印的应用。2017年,雷尼绍还帮助路虎BAR帆船通过金属3D打印的液压系统零件提升性能,加工出内含光滑圆角的零件,大大提高流体传输的效率。
可以说金属3D打印在液压领域的应用正在像其在随形冷却模具领域的应用一样不断的深化。
3D打印液压件积极的探索者
如果选择金属3D打印技术来制造液压阀块,在进行产品设计时无需考虑交叉钻孔的设计约束,并且可以将锋利的角换成圆形弯曲的设计从而减少湍流现象。这种通过传统液压阀块制造技术无法实现的设计方案,通过金属3D打印是可以实现的,Aidrohydraulics公司也正是通过3D打印技术获得了更高的设计自由度。
AidroHydraulic公司1982年成立,成立以来一直专注于设计和生产液压系统中的零部件,所推出的液压阀体产品包括方向阀、止回阀、流量阀、压力阀和比例阀。2017年,AidroHydraulic在35年液压零部件传统制造经验的基础上正式推出了金属3D打印的液压产品,其中包括3D打印的液压阀体。
完整的液压系统包括动力元件、执行元件、控制元件、辅助元件和工作介质。控制元件(即各种液压阀)在液压系统中起到控制和调节液体的压力、流量和方向的作用。Aidrohydraulics成功开发的首个3D打印液压阀块,制造材料是不锈钢,作用是控制单作用气缸。Aidrohydraulics在设计3D打印阀块时进行了创新,液压阀块的内部管道经过了设计优化,使内部管路中的液流得到改善,整个阀块的体积也比传统设计的阀块更小了,潜在的液体泄漏问题也得以避免。在商业化方面,Aidrohydraulics使用金属3D打印技术为一些有特殊需求的客户定制化生产小批量的液压阀块,作为其现有液压零部件生产能力的一种补充。目前,不锈钢(从AISI304到316L)、铝、钛,以及部分新材料的阀块都能够通过3D打印设备进行小批量生产。
国际上,另外一家公司,DominFluidPower也是3D打印液压领域的积极探索者。DominFluidPower制定了新的流体动力产品“稳定”设计的战略,这个战略建立在以金属3D打印技术作为制造方式的基础上。在此基础上,Domin公司对一些多年来都没有什么明显改变的液压流体动力零部件进行了重新设计与制造,包括直接驱动伺服液压阀。
DominFluidPower重新设计与制造的3D打印直接驱动伺服液压阀,经历了上千小时的设计、分析、测试和评估。DominFluidPower表示重新设计的3D打印阀体在重量、体积上都得以降低,由于液压阀体压力损失的减少,阀体效率也得以提升。
机加工、检测技术一个都不能少
不过金属3D打印在液压零件方面的应用还需要与机加工以及热处理等后处理工艺相结合才能真正达到零件的性能要求。宾夕法尼亚大学的TimothySimpson教授曾制造了一个带复杂内腔结构的液压零件,这个零件是用Inconel718合金制造而成的,在3D打印完成后,多轴CNC加工中心为精加工关键特性提供了高度的精度,这个特殊零件需要精确的外径,以确保跟其他零件能成功安装在一起,为了正常运转,表面光洁度也是另外一个重要的关键质量要求。圆柱体的顶面和底面存在临界平面度和平行度的精度要求,这都需要通过机加工来实现。最后,流体端口必须承受10,000psi的压力,这需要进行精密的螺纹磨削操作。
先进的检测技术也同样不可或缺,拿宾夕法尼亚大学的TimothySimpson教授所完成的这个液压零件来说,为了确保内部结构的正确性,宾夕法尼亚大学和Imperial机床工具公司通过计算机断层扫描系统和其他先进的设备来完成零件内部的检测。最后获得的零件比原来的设计减轻重量超过40%,同时提高了流体流动性能。
此外,很多液压零件需要锻造件的致密度,虽然热处理可能会带来一定的几何变形,但是热处理对于获得更加致密的液压零件是不可或缺的,3D科学谷认为如何将3D打印技术与热处理技术结合起来,这对于液压零件的制造非常重要。
目标:量产
在3D打印液压零件实现量产方面,根据3D科学谷的市场研究空客可谓是个野心勃勃的实践家,2017年3月30日,空客装载了首个3D打印液压件的A380飞机已试飞成功,这让空客看到了通过3D打印提高液压零件性能的机会。不过这个零件的制造过程是充满探索与曲折的,扰流板液压件是一个关系到飞机安全的关键部件,它的作用是控制空气断路或者扰流板。
在七年的研发过程中,这个项目组一直针对金属3D打印这一增材制造技术而进行扰流板液压件的优化设计。3D打印的材料是Ti64钛合金,3D打印液压件的明显优势是轻量化,其重量相比原来液压件减轻35%。在性能方面,3D打印的液压件使液压系统的效率得以优化,产生更少的热量,降低噪音,同时对液压动力的要求更少。而液压系统效率的提升,将为飞行带来附加效益,例如减少空气阻力以及优化飞机的燃油效率。
3D打印液压件的研发和测试过程是漫长的,通常为了保证飞行安全,即使是由传统制造方式制造的液压零部件也需要经过1200万个测试周期,3D打印液压件也同样需要经历这样一段测试周期之后,才能够进行飞行测试。
对于这个3D打印扰流板液压件,空客的最终目标是实现量产。参与项目的成员德国利勃海尔集团是空客的一级供应商,该公司与2016年年底向空客交付了3D打印液压件。利勃海尔的专家曾表示,对于航空3D打印液压件他们还有更多的设计思路,接下来他们将会进行首轮测试。未来,他们将建立一个增材制造工厂,量产这些液压件。
当前的可操作性
当然,实现量产的路或许还很长,意大利AidroHydraulic给出了当前3D打印应用到液压零件的参考因素。
生产数量:传统制造技术适合大规模生产,对于小批量的复杂液压件3D打印技术则更经济。
交期:用CNC机床加工金属棒料,制造周期为30-60天;如果是对液压铸造件进行加工,那么从铸造到完成加工的周期为6-12个月;用金属3D打印技术制造复杂液压件的周期可以缩短至几天之内,如果打印件需要进行机加工,则周期需要增加1-2周。
材料选择:液压零部件的制造材料必须具有足够的强度和耐腐蚀性,才能安全地应对液压系统的高压,传统液压技术中最常用的材料是碳钢,不锈钢和铝。金属3D打印设备可加工的材料包括:不锈钢(AISI316L)、铝、钛(Ti6Al4V)、铬镍铁合金(625或718)、马氏钢…
原型设计:如果客户要制造的液压件是用于设计验证的原型,那么,金属3D打印技术则更具灵活性,它的价值在于可以短时间内同时打印出不同型号的设计原型。
当前3D打印在国内的液压领域的应用还处于空白,在3D科学谷看来,这主要源自于两方面原因。
一是我国不少关键的液压零件制造水平落后于国际水平,长期以来我国在打破关键液压零件依赖进口方面做出了不断的努力,但是追赶这个差距的本身就消耗了大量的精力和财力,这使得企业很难顾及像国外企业这样花费长达十几年的时间探索3D打印技术与液压零件的制造技术的结合。
二是对于成熟的液压产品来说,尤其是航空航天和国防军工领域,不仅仅缺乏对3D打印技术的掌握,国内企业还缺乏整套的思路如何通过3D打印技术来制造出满足复杂且严苛的军标液压产品。根据3D科学谷的市场研究,在这方面,制造型企业呼唤3D打印企业的全套培训与打印服务体系,只有双方携手,才能探索出切实可行的方案。
声明:本网站所收集的部分公开资料来源于互联网,转载的目的在于传递更多信息及用于网络分享,并不代表本站赞同其观点和对其真实性负责,也不构成任何其他建议。本站部分作品是由网友自主投稿和发布、编辑整理上传,对此类作品本站仅提供交流平台,不为其版权负责。如果您发现网站上所用视频、图片、文字如涉及作品版权问题,请第一时间告知,我们将根据您提供的证明材料确认版权并按国家标准支付稿酬或立即删除内容,以保证您的权益!联系电话:010-58612588 或 Email:editor@mmsonline.com.cn。
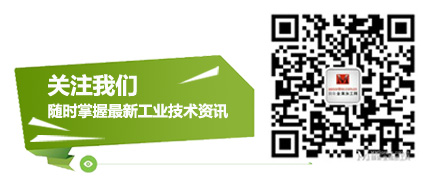
- 暂无反馈