机械手上线:车间还要引入机器人
储料、注射、保压、冷却、开模、顶出取件……这是一台注塑机的工作过程。在注塑机作业员李冬看来,整个注塑成型过程中,难度和劳动强度最大的工序就是顶出取件:因为注塑机每生产出一件产品,他就需要开关舱门取件一次,这样的动作每天要重复数百次。不过,自去年公司引进机械手后,李冬的工作量便大大减轻了。
昨日,记者来到李冬所在的企业——湖南湖大艾盛汽车零部件装备制造有限公司,探访经过智能化改造的生产线。
湖大艾盛是一家主营汽车内外装饰注塑件研发、制造的汽车零部件装备制造企业,于2011年签约入驻浏阳高新区。近年来,该公司投入大量资金对原有的生产车间进行智能化改造,实现技术、产品同步升级。
在湖大艾盛注塑车间里,分布着9台注塑机,一人多高,形似长方形盒子,每台机器都安装了机械手。注塑车间工艺员汪涛告诉记者,整个注塑环节,就在这些封闭的机器里进行:机器里装着模具,机器外面挂着料桶,料桶里的塑料融化后被注入模具,经冷却后变成汽车上使用的一个个零部件。
而由于注塑机上安装的机械手能模仿人手臂的动作,现在无需开关舱门,机械手就可以将产品抓取出来,整个过程耗时仅需60秒。
“以前人工取件,时间紧、工作强度大,工人要打开舱门,进入机器里面取出部件,然后再关上舱门,整个过程需要70—80秒。”汪涛说,除耗时更长外,人工取件存在不确定性,如果取件速度没有跟上生产产品的速度,容易造成产品堆积,导致出错遗漏。同时,注塑机在运转时,人工取件还存在人被烫伤或被崩出来的零件砸伤的风险。
以前一台注塑机一天产量在400—500件,如今有了机械手,注塑机生产的产品不仅质量更稳定,生产效率也大大提高,一台注塑机平均每天可多生产约200件产品。
事实上,为注塑机添置机械手只是第一步,湖大艾盛开展智能化改造不止于此。2017年以来,该公司投入近千万元购置智能化装备,引入了ERP(企业资源管理系统)、MES(生产管理系统),在“机器换人”的智能化道路上又前进一步。
“今年4月份,公司就可以完成MES系统升级改造项目,对车间所有注塑机进行统一编码管理,实现生产过程数据化,实时分析生产过程,进一步提高生产成本的控制能力。”湖大艾盛副总经理熊礼明介绍,公司将继续推进智能化改造,特别是在智能物流仓储环节加大投入,通过引进智能AGV搬运机器人等先进设备,进一步提升生产效率,提高产品质量,节省人工成本。
声明:本网站所收集的部分公开资料来源于互联网,转载的目的在于传递更多信息及用于网络分享,并不代表本站赞同其观点和对其真实性负责,也不构成任何其他建议。本站部分作品是由网友自主投稿和发布、编辑整理上传,对此类作品本站仅提供交流平台,不为其版权负责。如果您发现网站上所用视频、图片、文字如涉及作品版权问题,请第一时间告知,我们将根据您提供的证明材料确认版权并按国家标准支付稿酬或立即删除内容,以保证您的权益!联系电话:010-58612588 或 Email:editor@mmsonline.com.cn。
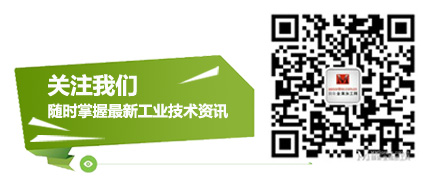
- 暂无反馈