关于3D打印和它在汽车制造业中的应用
【编者按】3D打印技术离我们的生活越来越近,不仅应用在医疗、汽车领域,就连航空航天核心零部件制造都需要3D打技术来帮忙。如今的3D打印,已经成为了汽车制造业重点发展的技术。
由于近年来开始下放到民用领域,3D打印技术一度成为了我们身边的“网红热词”,不过你可能不知道的是,这项技术已经有30年的发展史了。并且,如今的3D打印,已经成为了汽车制造业重点发展的技术,帮车企省下高额的成本。下面,我们就具体聊聊3D打印和它在汽车制造业中的应用。
● 3D打印已经有30年历史了
印象中,3D技术似乎是近几年才逐渐进入我们视野的。但事实上,在变成“网络热词”之前,这项听起来就高大上的制造技术其实已经闷声发展30年了。
这位伟大的父亲叫Scott Crump,今天3D打印行业巨头之一——Stratasys公司的创始人。小姑娘是幸福的,因为她或许没想到,当初面对那只坑坑洼洼的塑料青蛙时勉强挤出的笑容使她成为了富二代。
在后来的30年间,随着材料迭代和技术革新,3D打印逐渐从商用走向民用,适用范围也逐步扩大到电子、医疗、航天和汽车制造等领域。而经过多年的商战、收购、破产、被收购这类俗套故事之后,目前比较大的3D打印技术公司有3DSYSTEMS(美国)、Stratasys(美国)、EOS(德国)、ARcamAB(瑞士)等几家。
● 3D打印和传统裁切技术比怎么样?
◆ 3D打印的优势
先说优势,就汽车制造业来说,“轻”有着不一般的价值。
此外,对于那些只需要制造几个或是几十个的部件来说,单独开模肯定是不划算的,手工制造当然是一个选择,而如果用3D打印技术,就只需要在3D打印机中输入设计文件,省去了开模的高昂费用,产品一致性也优于手工制造,且同一台打印机可以读取不同的设计文件,反复使用。
◆ 3D打印的劣势
3D打印目前的误差还比较大,精度远不如传统开模制造的工艺,这也是3D打印行业待攻克的一个难题。另外,单一部件的制作工时长也是一大缺点,3D打印的生产节拍要远低于传统流水线,不利于规模化生产。
● 汽车制造业用3D打印做原型
◆ 原型测试
原型测试即在产品开发阶段,利用3D打印做出原型件,模拟还未量产的实际零部件,并利用它进行测试和改良。目前,许多车企已经在开发阶段使用3D技术进行原型测试了。原型测试本身也分成:概念原型、设计原型、功能原型,三者对设计参数的模拟精度要求依次提高。
到了零部件的设计原型上,就需要3D打印原型的机械性能也与设计相符,对于材料的使用和工艺的要求大大提高。最后的功能原型与设计原型类似,但因为要放到整车上进行测试,对精度要求更高。
和仿真软件类似,3D打印技术在开发中的应用使得车企和零部件供应商不再需要每修改一版设计,就重新进行一次开模,节省了研发成本。
◆ 生产工具制造
除了用于开发测试之外,由于在少量生产上的优势,3D打印还被用在制造生产工具上,例如贴标机,很多人可能不知道这个东西,这里解释一下:产线工人在装配车牌架的时候并非用手装配,而是需要把车牌架放在如下图所示的贴标机上,然后推着贴标机将车牌架固定到车身上。
由于每个工厂贴标机只需要十几个,开模制造的均摊成本太高,如果集中制造,还需要库存和物流成本。相比之下,目前很多车企选择在工厂内使用3D打印机,随用随打,免去了开模、库存和物流成本,且一台3D打印机可以制作多种类似贴标机这类的生产工具。此前宝马也利用Stratasys的3D打印机制作了400多个工装夹具,降低了72%的重量以及58%的成本,而这个量级也是最合适使用3D打印技术的,如果再多3D打印就难以胜任了,生产效率和精度都没法和传统制造工艺相比。
◆ 整车和零部件制造
至于零部件,在目前的汽车制造业还极少有量产化的应用。不过,业内“玩家”的新奇尝试可一点不少。
不过,尽管叫做全3D打印汽车(75%使用率),电机、传动机构等核心部件仍然是采购的,这些过于复杂的和对物理性质要求过高的部件,显然3D打印还难以胜任。
当然,除了这些“概念产品”,兰博基尼也曾使用3D打印制造发动机的进气歧管,证明了其应用于核心零部件制造的可行性。实际上,定制化的3D打印件目前就可以达到极高的机械性能,且基于独特的制作形式,我们甚至可以认为利用3D打印制造进气歧管的设计空间还要更高于传统裁切。不过现阶段,这样高度定制化的3D打印产品背后也一定代表着不菲的成本,怕是只能符合兰博基尼这种超跑制造商的定位了。
● 结语
正如上文所说的,3D打印和传统开模制造各自有着明显擅长的地方,3D打印技术适用于分布式生产,在开发阶段和小批量制造上有着得天独厚的优势,但由于其精度等劣势,3D打印技术短时间内还不具备取代流水线生产的能力。然而随着技术的迭代,可以预见的是,未来3D打印一定会越来越多地应用于汽车制造领域,跑马圈地,随着应用的普及以及参与竞争的3D打印技术供应商的增多,其使用成本也会随之下降,形成一个良性循环。未来,在3D打印和传统裁切两种生产模式相互配合之下,进一步缩短开发周期并降低生产成本还是可以期待的。
声明:本网站所收集的部分公开资料来源于互联网,转载的目的在于传递更多信息及用于网络分享,并不代表本站赞同其观点和对其真实性负责,也不构成任何其他建议。本站部分作品是由网友自主投稿和发布、编辑整理上传,对此类作品本站仅提供交流平台,不为其版权负责。如果您发现网站上所用视频、图片、文字如涉及作品版权问题,请第一时间告知,我们将根据您提供的证明材料确认版权并按国家标准支付稿酬或立即删除内容,以保证您的权益!联系电话:010-58612588 或 Email:editor@mmsonline.com.cn。
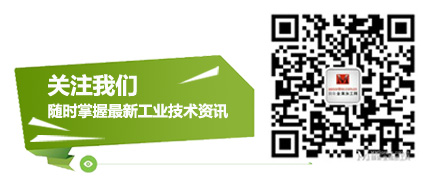
- 暂无反馈