3D打印技术对模具制造技术的影响分析
随着3D打印技术在汽车、航空航天、工业和医疗等领域的悄然兴起,较多业内人士对其发展有不同的见解。本文通过对比3D打印模具与传统模具制造技术的优缺点,客观地分析了3D打印技术对模具制造技术的影响,并提出了3D打印技术与模具制造技术融合互补的思路。
1、引言
3D打印(3Dprinting)技术与传统的模具制造“减材加工”技术相比,它是“增材加工”技术,是以计算机三维设计模型为基础,通过软件分层离散和数控成型系统,利用激光束、热熔喷嘴等方式将金属粉末、陶瓷粉末、塑料、细胞组织等特殊材料进行逐层堆积黏结,最终叠加成型成为实体产品。目前,主要的3D打印技术有热熔堆积成(FusedDepositionModeling,FDM)、光固化成型(StereolithigraphyApparatus,SLA)、三维粉末粘接成型(ThreeDimensionalPrintingandGluing,3DP)、选择性激光烧结成型(SelectingLaserSintering,SLS)等,就现状而言,能适用于金属制造业的也只有3DP和SLS。
2、3D打印技术与模具制造技术在生产过程中的异同分析
3D打印技术和模具制造技术在机械行业应用的目的都是将原材料加工成实体的零件,但在整个生产过程中存在着较多的不同。现以图1所示零件的加工过程为例,对比分析两种加工方式的异同。
图1轴承零件图
2.13D打印技术制造过程
3D打印技术制造模具过程主要通过接单分析、软件设计造型、转换打印3个步骤。主要工作原理如下:首先根据零件图通过计算机三维设计将模型造型出来,如图2所示,再用相应的软件通过断层扫描把零件的三维造型切成无数叠加的片,一片一片的打印,然后叠加在一起成为一个立体物体的过程。以3DP打印为例,其工作原理如图3所示,先撒布一层打印用的粉末材料,然后使用喷嘴将粘合剂喷在需要成型的区域,让材料粉末粘接,形成零件截面,然后不断循环重复铺撒粉末材料、喷涂、粘接的过程,层层叠加,获得最终打印出来的零件。与传统的制造工艺相比,这种数字化制造模式不需要复杂的工艺、不需要庞大的机床、不需要众多的人力,其生产周期短,节省加工材料。
2.2传统模具制造过程
传统模具制造过程在接单后还需对接单项目进行评审,评审过关后制定生产进度表,然后进行3D软件修正、模流分析、分型线及进料点确定,最后反馈给客户定稿,客户满意后才能确定制造用的零件图,才可以准备加工流程,其加工流程如图4所示。从加工流程可见,采用传统的模具制造过程加工出一个合格的模具所需要的人力、物力较多,生产周期较长。
3、3D打印技术的优越性
通过设计、生产过程的比较,3D打印技术作为时下最热火的制造业前沿技术,其优越性显而易见。
(1)3D打印技术在生产过程中能实现生产材料“零”浪费。3D打印技术的生产过程是根据零件的三维设计进行逐层打印,与传统的“减材”加工相比,实现了生产材料的“零”浪费。
(2)3D打印技术可以加快产品的研发进度。3D打印技术改变了设计者的思维方式,他们会根据零件承重、受力部位的不同进行思考。就如我国正在进行起降训练的歼15,其整个前起落架都由3D打印技术打印出来的,有专家分析,3D打印技术将弥补我国歼20发动机的不足,从而加快我国国产战机的尖端技术的研发进度。
(3)3D打印技术可以大大缩短生产周期。3D打印技术从设计到生产,省去了传统加工过程中工艺设计与求证的过程,缩短了生产周期,并能根据市场需求,及时调整生产批量。
(4)3D打印技术可以大量减少设计、生产过程中的人力资源。
4、3D打印技术短期内无法替代传统模具制造技术的原因分析
图2轴承三维造型图
图33DP打印轴承工作原理图
图4传统模具制造过程
3D打印是近几年的热门话题,3D打印在制造业的发展是我院“3D打印在机械制造中的发展与应用”科研小组近几年研究的课题。通过实地考查以及实际操作,3D打印节约原材料、减少人力以及能设计就能加工等优点让人惊叹。促进3D打印技术快速且广泛用于制造业成为研究的主要课题之一。在研究过程中找出了3D打印技术从开始研发至今仍不能完全替代传统模具制造技术原因。
(1)3D打印模具的零件尺寸受限。去年华中科技大学史玉升教授的团队成功研制出1.2×1.2m的3D打印机,这在当时是世界加工面积最大的设备。2013年大连理工大学教授姚山及其团队历经10多年时间,成功研制了工作面尺寸达到1.8×1.8m级的激光3D打印机,其技术刷新了世界最大3D打印机记录,但这些设备仍不能满足工业上大型模具的制造。如何解决3D打印大型模具的技术难题是目前需要解决的问题。
(2)3D打印模具的力学性能难保证。
力学性能是零件的重要参数,为零件的选材、设计、失效及分析、使用和寿命提供了主要依据。据权威部门统计,由于材料失效所造成的经济损失约占发达国家年产总值(GDP)的4%,其中航空工业材料失效又占材料失效的5%,可见零件力学性能的重要性。为此,传统的数控切削加工为了保证零件的力学性能,在生产过程中较多的时间是在对零件进行时效、热处理等相关工作。而3D打印技术却不能完成这些工作,从而打印出的零件的力学性能较难保证。如何找到更好的3D打印原材料、如何改进3D打印技术、如何结合金属热处理等技术提高3D打印模具的强度、韧性、表面硬度,是3D打印急需解决的难题。
(3)3D打印技术可使用的材料种类较少、能提供打印材料的供应商有限。
传统制造业所用材料的种类繁多,同一形状的零件因使用部位不同,考虑到经济及其他因数,所使用的材料大不相同。而目前我国的3D打印材料依赖进口,而掌握最多打印材料的以色列Object公司也只使用14种基本材料,107种混搭材料,这些材料中能用于工业的就更少了。3D打印技术在打印零件时就不能因零件使用要求选材,从而提升了制造成本。
5、3D打印技术与模具制造技术相容互补的前景分析
目前,针对3D打印技术和传统加工技术存在的不足和优势让它们相容互补是目前3D打印技术发展的方向。例如,企业在开发新产品时,可以用3D打印技术制造样品,传统制造技术进行批量生产。因为这样不仅可以去除传统模具制造先做模具,通过模具制造出样品,再进行多次修改,最后制作出满意的样品的步骤,还可以让传统制造的批量生产弥补3D打印速度慢、制作终端产品成本高的劣势,从而加快了产品上市的时间,提高了经济效率。
此外还应着手分析工业材料生产方法并结合传统制造中速熔连接技术,开发出用于工业生产、价廉质优的3D打印材料。
在机床生产上面应思考将3D打印机与数控机床合二为一,设计出高科技、多功能的新型制造机床。
6、结束语
3D打印技术和传统制造技术都存在优势和劣势,目前3D打印技术还不能替代传统制造技术。为此只有通过探索、研究取两技术之长处来推动制造业的高速发展。
声明:本网站所收集的部分公开资料来源于互联网,转载的目的在于传递更多信息及用于网络分享,并不代表本站赞同其观点和对其真实性负责,也不构成任何其他建议。本站部分作品是由网友自主投稿和发布、编辑整理上传,对此类作品本站仅提供交流平台,不为其版权负责。如果您发现网站上所用视频、图片、文字如涉及作品版权问题,请第一时间告知,我们将根据您提供的证明材料确认版权并按国家标准支付稿酬或立即删除内容,以保证您的权益!联系电话:010-58612588 或 Email:editor@mmsonline.com.cn。
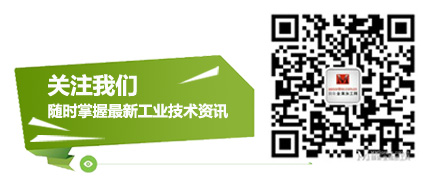
- 暂无反馈