3D打印技术在大型铸锻件领域应用
目前,3D打印技术的应用及研究主要集中在航空航天、电子、医疗等精密零件的加工和修复领域,而在以铁基金属为主的大型铸锻件领域上的应用还很少。大型铸锻件产品,如火电主轴、核电封头、水轮机叶片等的重量动辄几十上百吨,而以目前的金属3D打印技术平均1kg/h的加工速度以及每公斤上千元的材料成本计算,采用大型铸锻件整体3D打印技术完成大型铸锻件的制造无法实现。但是,这并不是说3D打印技术不能在大型铸锻件领域得到广泛的应用。
只要应用得当,3D打印技术也可以像铸造、锻造以及焊接一样,成为大型铸锻件制造中不可缺少的重要生产工艺,并且在大型铸锻件行业的技术创新、降本增效、质量提升过程中发挥重要作用。本文通过参考当前金属及非金属3D打印技术在其他领域取得的研究成果,对未来3D打印技术在以铁基金属为主的大型铸锻件领域的应用方向进行了分析,从而为大型铸锻件行业的发展提供借鉴。
1.金属材料3D打印技术
3D打印钛合金大型整体主承力结构件等大型零件的金属材料的性能可以达到或接近锻件水平。3D打印技术修复涡扇发动机叶片技术实现了3D打印与零件基体结合区域的性能达到了零件的要求。与传统的焊接相比,金属3D打印修复具有以下特点:
(1)热影响区小,不影响基体组织应力分布;
(2)无需加热及后续热处理;
(3)3D打印组织与基体冶金结合致密,性能接近零件原组织;
(4)3D打印区域组织性能达到锻件水平;
(5)自动化控制,加工余量少。
1.1 大型锻件局部3D打印成形
以AP1000核电主管道为例,设计要求采用超低碳控氮不锈钢整体锻造,锻件生产的主要难点是两个管嘴的成形,锻件材料利用率在15%以下。受3D打印技术修复涡扇发动机叶片的启发,核电主管道的成形可以简化为锻造或挤压不锈钢管+3D打印管嘴成形,该方法能够极大的降低核电主管道的生产难度及成本。
类似核电主管道及多管嘴封头等具有局部难成形特征的大型锻件都可以采用锻件主体+3D打印局部的方式成形,该方法将在保证锻件整体质量的情况下大大降低锻件的生产难度、成本和周期。另外,还可将大型锻件局部3D打印成形的思路拓展到大型零件3D打印拼焊技术。如果3D打印区域以及3D打印区域与基体结合区域的金属材料性能都能达到锻件要求,这就预示着未来完全可以采用3D打印拼焊锻件代替整体大锻件。
1.2 大型锻件缺陷修复
大型锻件表面及内部的超标缺陷、由于缺料造成的锻件加工余量不足等质量问题,都可能导致锻件的整体报废,造成巨大的经济损失和能源浪费。由于焊接组织的性能低于锻件组织,因此锻件一般不容许补焊,而金属3D打印技术的出现却能改变这一现状。目前,金属3D打印的某些材料性能已经能够达到锻件水平,如果3D打印组织与锻件基体的结合能达到锻件要求,就可以采用3D打印技术局部修补大型锻件的缺陷区域,从而提高锻件合格率。未来,随着3D打印技术的提高,类似大型铸件容许补焊一样,大型锻件也容许3D打印修复,这对于大型锻件生产工艺将是革命性的突破。
1.3 大型零件在线修复
发电机转子、水轮机叶片、船用曲轴等大型零件在使用过程中会出现局部裂纹、磨损及变形等失效问题,传统的补焊方法需要通过机加工→预热→焊接→机加工→热处理等流程才能修复。修复工作需要在大型专业设备上进行,但是修复区域性能低于零件原组织,增加了维修成本、维修周期,维修效果也不理想。而采用机器人与3D打印技术相结合构成的便携式可移动金属3D打印设备能改变这一现状,实现大型零件的现场修复,甚至在线修复。机器人金属3D打印技术修复大型零件的具体操作步骤是:
(1)确定修复方案,对修复区域进行预处理;
(2)采用三维成像技术对修复区域进行三维反求建模;
(3)将修复区域三维模型转化为机械手移动路径;
(4)确定3D打印参数,机械手定位,进行修复;
(5)修复区域表面处理及检测。
1.4 大型零件表面处理
金属3D打印技术的一个重要发展方向就是多材料以及渐变材料的3D打印成形,该领域的研究成果可以在大型零件,特别是在结构复杂或功能复杂零件的表面处理上得到应用。相比于电镀、热喷涂以及化学气相沉积等传统的金属表面处理方式,金属3D打印技术被看作是激光涂覆工艺的延伸,具有结合层牢固、涂层厚度大且可控、数字化控制、材料范围广等优势,特别是在大型零件的局部改性和强化方面优势明显。
1.5 金属材料3D打印技术的研究重点
根据目前金属3D打印技术的发展情况,以上研究方向在技术上都有很大的可行性,而且许多技术已在小型零件上得到应用。为了使金属3D打印技术在大型铸锻件领域早日得到应用,当前应在以下几个方面进行重点研究:
(1)材料方面。相对于钛合金及高温合金,大型铸锻件使用的铁基合金较为简单,关键是材料成本的控制。
(2)设备方面。目前3D打印设备的工作台面尺寸及承重有限,无法满足大型铸锻件局部加工要求,未来需要开发更加灵活便捷的加工设备。
(3)系统方面。3D打印制造及修复需要三维反求、建模、二维路径转化等操作,而大型铸锻件多为单件小批量生产,缺陷出现随机性大,因此未来需要对相应软件及操作进行集成,从而提高生产效率。
(4)工艺方面。不断优化金属3D打印工艺参数,使其更好适应大型铸锻件的特殊要求,预防开裂、变形以及脱落等缺陷的产生。
(5)性能方面。为了使3D打印技术在核电、火电以及大型压力容器等大型零件上得到持久应用,类似持久蠕变、低周疲劳等材料基础实验数据需要长期积累。
(6)标准问题。不同于小型零件,安全生产是大型铸锻件修复及制造的重点,而各种生产和质量标准的缺失是3D打印技术在该领域发展的重要瓶颈,标准的制定也需要较长的时间。
2.非金属材料3D打印技术
以蜡模快速成形和砂型快速成形为主的3D打印技术在小型精密铸件以及铸件快速成形领域已得到广泛的应用,并且有向大型化发展的趋势,目前已经可以制作2m以上的模型。重量在(20~500)t之间的汽轮机缸体、水电机组的叶片以及冶金设备机架等大型铸件一般采用木模+砂型铸造生产,目前还未使用3D打印技术进行生产制造。
2.1 大型铸件模型3D打印
非金属材料3D打印技术可以实现复杂模型的快速建立,对于生产批量大、形状复杂、表面要求高的大型铸件,可以整体或局部替代木模,从而有效缩短大型铸件生产周期,提高铸件生产质量。针对3D打印技术在大型模型建立过程中出现的成形速度慢、变形严重以及成本较高等问题,目前的解决方法有几种:
(1)增大3D打印线材直径以提高加工速度;
(2)采用多喷头设计以提高加工速度;
(3)多个小设备并行工作,拼粘成大型模型以提高加工速度;
(4)在3D打印设备上增加热保温装置,减少零件变形翘曲;
(5)优化3D打印参数,从而减少模型变形及开裂等问题;
(6)优化3D打印材料,在保证模型质量的同时降低材料成本及使用量;
(7)采用木模基体拼粘3D打印局部方案,降低生产成本,缩短制造周期。
2.2 大型铸件砂型3D打印
砂型材料3D打印技术的原理是通过低功率激光器对树脂砂进行逐层烧结最终形成复杂砂型,目前主要用于中小型复杂铸件的快速制造。采用3D打印技术生产大型铸件砂型有以下优点:
(1)大型铸件目前使用的反箱制模型方法对拔模角度有很高要求,而3D打印砂型对拔模角度无要求,甚至可以实现负拔模角度;
(2)3D打印砂型无需制模、反模等过程,就可以制作非常复杂的铸件,摆脱了工艺方法对铸件形状的约束;
(3)3D打印砂型使单件小批量生产的大型铸件的生产周期缩短,成本降低。
3.3D打印砂型在大型铸件中使用的主要难点有:
(1)性能问题。大型铸件几何尺寸很大,3D打印砂型的强度需要提高。3D打印的砂型致密性较高,发气量较大,在大型铸件生产过程中可能出现很多缺陷,因此,需要通过实验方式分析具体工艺措施或原材料配比来解决缺陷。
(2)速度问题。目前的3D打印速度较慢,提高加工速度的方法基本与模型3D打印一致。
(3)设备问题。大型砂型强度较低,应尽量减少运输过程,其生产设备最好设置在铸造车间内。目前,还不能使用3D打印技术直接生产大型铸件的整体砂型,但是可以将3D打印砂型作为大型铸件砂型的镶件或砂芯,用于成形铸件局部复杂区域。
未来,最经济有效的大型铸件生产方式将会是非金属材料3D打印技术、铸件传统生产工艺以及数值模拟技术三者的结合,具体的工艺步骤是:
(1)生产单位收到零件图纸及模型,开始铸件及浇铸系统初步设计;
(2)综合考虑铸件变形、开裂等因素,采用有限元软件对铸件结构和浇铸系统设计进行优化;
(3)将优化后的模型进行分解,模型基体部分采用传统木模成形,复杂几何尺寸部分采用模型3D打印成形,二者通过粘接形成铸件最终模型;
(4)将铸件中形状复杂、负拔模角度部分采用砂型3D打印成形;
(5)将3D打印砂型镶嵌在大型铸件砂型中,结合模型生成最终的大型铸件砂型。
由于采用3D打印技术生产的模型及砂型是由数模直接转化成实体模型,无需人工操作,因此可以提高模型表面质量,缩短铸件生产周期,摆脱传统工艺方法对铸件结构的限制,从而提高铸件的材料利用率、减少铸件缺陷、降低铸件成本。
3D打印技术作为一种通用的零件加工手段,极大的摆脱了传统工艺方法对产品设计、生产周期、生产成本等生产要素的束缚,为传统制造业的转型升级开辟了一种新的思路。3D打印技术在大型铸锻件生产领域有很大的发展空间,金属3D打印技术在大型铸锻件的制造及修复领域发挥了重要作用,非金属3D打印技术改进了大型铸件生产工艺,实现了降本增效、缩短生产周期、提高铸件质量。从目前3D打印技术的发展情况来看,3D打印技术在大型铸锻件领域的应用还需要经历一个由小型到大型,由非关键部位到关键部位,由普通零件到重要零件的发展过程。
目前,我国大型铸锻件行业处于产能严重过剩、低端产品恶性竞争,高端产品受制于人的不利局面。采用传统的方法对大型铸锻件生产工艺进行改进已不能有效降低生产成本、提高零件质量、缩短生产周期、拓展市场空间。因此必须引进新的技术和方法才能大幅提高我国大型铸锻件行业的竞争力。3D打印技术又称增材制造技术,是以数字模型为基础,将材料逐层堆积制造出实体物品的新兴制造技术,是新一轮科技革命和产业变革的重大机遇。
声明:本网站所收集的部分公开资料来源于互联网,转载的目的在于传递更多信息及用于网络分享,并不代表本站赞同其观点和对其真实性负责,也不构成任何其他建议。本站部分作品是由网友自主投稿和发布、编辑整理上传,对此类作品本站仅提供交流平台,不为其版权负责。如果您发现网站上所用视频、图片、文字如涉及作品版权问题,请第一时间告知,我们将根据您提供的证明材料确认版权并按国家标准支付稿酬或立即删除内容,以保证您的权益!联系电话:010-58612588 或 Email:editor@mmsonline.com.cn。
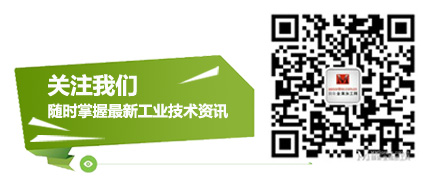
- 暂无反馈