弧焊机器人系统在汽车底盘焊接中的应用
首先介绍机器人焊接系统的常见应用方式及焊接机器人柔性系统,其后探讨多种机器人焊接新技术的应用及发展情况。
弧焊机器人最适合于多品种高质量生产方式,目前已广泛应用在汽车制造业,汽车底盘、座椅骨架、导轨、消声器以及液力变矩器等焊接件均使用了机器人焊接,尤其在汽车底盘焊接生产中得到了广泛的应用。国内生产的桑塔纳、帕萨特、别克、赛欧、波罗等后桥、副车架、摇臂、悬架、减振器等轿车底盘零件大都是以MIG焊接工艺为主的受力安全零件,主要构件采用冲压焊接,板厚平均为1.5~4mm,焊接主要以搭接、角接接头形式为主,焊接质量要求相当高,其质量的好坏直接影响到轿车的安全性能。应用机器人焊接后,大大提高了焊接件的外观和内在质量,并保证了质量的稳定性和降低劳动强度,改善了劳动环境。
机器人焊接系统的常见应用方式
按照焊接机器人系统在汽车底盘零部件焊接的夹具布局的不同特点,及外部轴等外围设施的不同配置,焊接机器人系统可分为以下几种形式。
滑轨+焊接机器人的工作站
(见图1)两套夹具固定在滑动小车上,由气缸驱动使装有工件的两个夹具轮流进入机器人焊接区焊接,操作人员在另一面上、下料。两个工作站交叉进行,使机器人焊接时间与工件上、下料时间同步,这种方式可以节约变位器旋转时间。双夹具滑轨形式的焊接机器人系统利用两副滑轨轮流为焊接机器人送料,可靠性较高,但对被焊工件的外形尺寸有一定限制,通常焊接工件直径小于0.6m。
在桑塔纳后桥焊接生产线、POLO下摇臂焊接生产线上均有应用实例。
单(双)夹具固定式+焊接机器人工作站
(见图2)该结构形式简单,夹具由变位机进行变位,来实现机器人焊枪不同位置的焊接。系统故障率低,但由于在装卸工件过程中机器人处于等待状态,因而机器人的利用效率一般低于80%,所以在新的焊接线上较少利用。
该系统在帕萨特后桥焊接生产线及桑塔纳前悬挂焊接和生产线有成功应用。
带变位机回转工作台+焊接机器人工作站
(见图3)该形式由两副夹具带变位器和一个转台组成,结构紧凑。两副夹具可以进行不同的焊接程序以实现不同的工艺要求。机器人在其中一副夹具上焊接工件时,操作工可以在另一副夹具上装卸工件,机器人的利用率较高,一般大于90%,是目前最广泛使用的一种形式。
该系统在别克副车架焊接线、赛欧后桥焊接线、帕萨特副车架焊接线均有广泛应用。
搬运机器人+焊接机器人工作站
(见图4)两部机器人之间的配合所体现的主要优点是能适应各种不规则焊缝的焊接。但缺点是由于两部机器人配合的不协调所导致的故障率较高。所以此种形式需合理安排机器人运动形式才能最大程度提高生产效率。
协调运动式外轴+焊接机器人工作站
见图5)该形式运用较广泛。在实际焊接中环焊缝是常见的一种,而常见的变位器不能适应360°焊接,在这种情况下,协调式外轴与机器人相配合即可轻松实现360°以上环焊缝的焊接。
在帕萨特后桥稳定杆焊接、波罗后桥总成焊接中均采用了该形式。
机器人中置式工作站
(见图6)该系统由两转台和四套变位器组成,可以方便地实施两种以上产品的焊接。尤其针对生产任务不均匀的情况,可以合理调配,以提高机器人的利用率。但该系统对空间资源占用大,且电器方面故障率高,所以目前并没有广泛采用,仅在派力奥与SIENA后轴焊接项目中试用。
机器人焊接自动线
(见图7)机器人焊接自动线是今后轿车底盘焊接的主要发展方向。该形式由多台机器人焊接系统和悬挂输送链组成,由多台机器人之间的配合来完成一个产品的焊接加工。由于每道所焊的焊缝数较平均,所以对整个产品的焊接变形影响小。
目前桑塔纳前悬挂焊接生产线、帕萨特后桥焊接生产线均采用此形式。
焊接机器人柔性系统
随着市场竞争加剧,汽车行业面临品种多、批量少的改型性的新车型需求,要求焊接机器人系统必须高度柔性化。焊接机器人系统的柔性化,即:适应于不同零件的焊接夹具;能短时间内快速调换气、电信号、配管、配线快速改换;控制程序必须能预置和快速转换,最大程度地发挥机器人特点以使一套机器人系统能根据需要焊接多种零件和适应产品多样化和改进的要求。可快速调换夹具的二、四工位焊接机器人系统能体现系统柔性化。
二工位点焊机器人系统
(见图8)系统由一台标准的点焊机器人、两个采用机器人外部轴伺服驱动的回转工作平台及电极修磨器、冷却系统等周边装置组成。其柔性主要体现在以下几点:
给标准点焊机器人配备了快速交换连接器。通过快速交换连接器,可实现机器人焊钳的快速自动更换,不但可满足复杂产品各个部位的焊点焊接,而且,在更换产品时,只需更换合适的焊钳就可以了。
柔性的系统控制。该系统的主控系统采用PLC为主控单元,配以远程I/O模块,通过机器人的远程I/O模块,实现对机器人、夹具、夹具工作平台及周边装置的控制。PLC程序采用结构化方式编制,各个子程序分别对应于一个功能,对于不同工件,只需调用或修正不同子程序,不需重新编程。不同产品的焊接内容及夹具气缸的动作关系的设计和操作完成后,可以长时间储存,更换产品时可直接调用。操作控制采用触摸屏,减少了大量复杂的连线,同时可以为不同工件专门设计不同的操作及状态显示界面。
采用机器人外部轴伺服驱动的回转工作平台。该平台除可以承受较大的径向和轴向力外,同时采用机器人外部轴伺服驱动和控制转台,从而使转台有极好的启停特性,并与机器人实现协调运动,可实现多工位焊接。在回转平台上装有远程模块,转台中心留有气路和电路出口专用快速接头和多芯插口,以便使夹具可快速装拆。
这套系统已成功的生产了金杯副车架、后桥及派力奥横梁、摆臂等多种产品,且产品更换方便快捷。
四工位的弧焊机器人系统
该系统有两台KR15弧焊机器人、一个四工位旋转式转台、夹具回转变位装置及清枪器、焊机等周边装置组成。其柔性主要体现在机器人工作范围较大,功能较全。夹具回转变位装置安装法兰上装有远程模块,远程模块预留多芯航空插头,在更换夹具时,可方便地与夹具上的相应接口连接。夹具回转变位装置端部有压缩空气快速接头,可方便快速地与夹具的气路连接,在2~3分钟内便可以实现新夹具与变位器的机械连接。
机器人焊接新技术应用
TCP(tool center point工具中心点)自动校零技术
焊接机器人的工具中心点就是焊枪的中心点,TCP的零位精度直接影响着焊接质量的稳定性。但在实际生产中不可避免会发生焊枪与夹具之间的碰撞等不可预见性因素导致TCP位置偏离。通常的做法是利用手动进行机器人TCP校零,但一般全过程需要30分钟才能完成,影响生产效率。TCP自动校零是用在机器人焊接中的一项新技术,它的硬件设施是由一梯形固定支座和一组激光传感器组成。当焊枪以不同姿态经过TCP支座时,激光传感器都将记录下的数据传递到CPU与最初设定值进行比较与计算。当TCP发生偏离时,机器人会自动运行校零程序,自动对每根轴的角度进行调整,并在最少的时间内恢复TCP零位。
目前在波罗后桥及帕萨特副车架的机器人焊接生产线上均采用了该技术,大大方便了设备调整,节约了调整时间,提高了产品的质量。
双丝高速焊接技术
双丝高速焊不仅焊接效率比传统焊接方式高,而且热影响区小,产品的疲劳强度有所提高。目前双丝焊主要有两种方式:一种是Twin arc法,另一种为Tandem法。焊接设备的基本组成类似,都是由两个焊接电源、两个送丝机和一个共用的送双丝的电缆。为了防止同相位的两个电弧的相互干扰,常采用脉冲MIG/脉冲MAG焊法,并保持两个电弧轮流交替燃烧。这样一来,就要求一个协同控制器保证两个电源的输出电流波形相位相差180°(如图9)。当焊接参数设置到最佳时,脉冲电弧能得到无短路、几乎无飞溅的过渡过程,真正做到“一个脉冲过渡一个熔滴”,每个熔滴的大小几乎完全相同,其大小是由电弧功率来决定。
目前在波罗下摇臂焊接中采用了Tandem方式,主枪与次枪均采用脉冲式,其焊接速度可达30mm/s, 不但提高了焊接效率,而且产品疲劳强度远远高于类似的单丝焊。
机器人等离子切割技术
对机器人焊接质量提出高要求,势必对冲制件的匹配性提出了更高要求。尤其是针对管状件的相贯线形焊缝,对冲制件的匹配轮廓度要求小于0.5mm,传统的冲压工艺很难直接保证达到此要求,于是,机器人等离子切割走进了汽车底盘零部件焊接生产线。机器人等离子切割是由普通的抓举机器人持等离子割炬按机器人编程轨迹进行匀速切割,氧气作为切割气体,氮气起保护作用,所切割工件边缘平滑,轮廓度小于0.3mm,保证焊接的质量稳定。当产品尺寸需要改进时,无需对冲压模具进行改进,只需对机器人切割轨迹进行简单的调整即可满足生产,可节约大量生产成本。
模块式夹紧机构的应用
在传统的底盘焊接机器人系统中夹具通常采用的是四连杆机构,该机构有夹紧和自锁的功能,但结构体积较大,影响了机器人
声明:本网站所收集的部分公开资料来源于互联网,转载的目的在于传递更多信息及用于网络分享,并不代表本站赞同其观点和对其真实性负责,也不构成任何其他建议。本站部分作品是由网友自主投稿和发布、编辑整理上传,对此类作品本站仅提供交流平台,不为其版权负责。如果您发现网站上所用视频、图片、文字如涉及作品版权问题,请第一时间告知,我们将根据您提供的证明材料确认版权并按国家标准支付稿酬或立即删除内容,以保证您的权益!联系电话:010-58612588 或 Email:editor@mmsonline.com.cn。
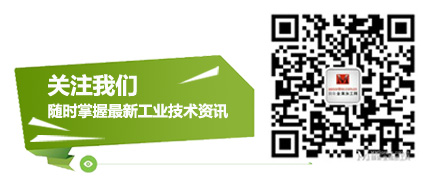
- 暂无反馈