如切如磋,如琢如磨—航空发动机零部件切削技术分析
航空发动机典型零件大多采用钛合金、高温合金等难加工材料。切削难度体现在切削力大、切削温度高、切屑不易折断、刀具寿命低、表面质量不易保证等方面。航空零部件是在高温、高压、高转速的恶劣环境下工作,航空新产品的开发意味着零件功能、结构、材料的重大变更,同时也对切削技术提出更高的要求。
航空发动机切削技术需求
(1)航空发动机的关键零部件如机匣壳体、叶片、轮盘、鼓筒、整体叶盘、叶轮等主要结构件,大量采用新型超高强耐高温合金、单晶合金、金属间化合物及轻质高强复合材料,对切削技术提出了更高的要求。
(2)刀具作为切削加工的主体之一,在解决航空材料的加工难题中起着至关重要的作用。先进的航空发动机要求航空零件具有更优异的性能、更低的成本和更高的环保性,而加工工艺要求刀具具有更快的加工速度、更高的可靠性、高重复精度和可再现性。硬质合金刀具、涂层刀具、陶瓷刀具、立方氮化硼刀具和聚晶金刚石刀具应用的比例大幅提高。
(3)零件表面完整性程度直接影响到先进航空发动机的可靠性与使用寿命。高推重比航空发动机在可靠性设计方面,对关键零件的表面完整性要求更高。
航空发动机切削关键技术
新型刀具材料和结构、新型切削工艺方法以及围绕航空发动机的典型材料建立的切削数据系统等正逐渐成为航空难加工材料切削加工领域的关键应用技术。在高速、高效切削技术方面,钛合金叶片型面、高温合金整体机匣铣削方面进行了工程化应用。切削数据库系统技术方面,建成典型发动机难加工材料优化切削数据库,对航空发动机各生产单元提供了切削数据参考。对于发动机零件工艺特征及刀具结构对于切削数据的影响规律以及优化计算、智能分析方面还有待开展进一步的研究。新型特种切削技术研究方面,低频振动切削、数控磨抛均已应用于零件加工。对于其他新型特种切削工艺在航空发动机零件加工中的适用性仍需开展研究。
切削表面完整性技术方面,对于部分发动机关重零件开展切削表面完整性研究,取得一定的研究结论。但对于切削过程对于表面完整性的影响规律还需系统的研究和应用。
切削仿真技术、切削变形预测技术方面,通过对部分典型零件切削过程进行物理仿真分析,掌握了进行切削物理仿真的基本技术。但对于仿真结果的切削验证、切削变形规律等方面还需要开展深入的研究与探索,尚不具备在工艺准备阶段进行切削变形预测的能力。
1 新型高效刀具应用技术
金属切削一直都是机械制造工艺中的基础加工方法,合理的金属切削加工工艺取决于刀具和切削参数的正确选择。航空发动机切削加工对刀具的合理选择提出了更高要求,包括精度高、强度大、刚性好、耐用度高,刀具尺寸必须稳定,安装方便。新型材料、新型结构刀具大量应用于发动机零件切削加工。新型结构刀具应能使切削轻快、减少由切削力引起的振动,实现低应力切削。陶瓷刀具高速切削高温合金已应用于多种零部件生产。对超硬刀具材料加工粉末高温合金进行了系统的试验研究。插铣技术、层铣技术、螺纹铣削技术、复合刀具技术得到推广。飞碟铣刀、模块化刀具以及低切削力,低振动新型刀具得到应用。该项技术难点在于新型高效刀具优选应用方案的制定、优选试验方法以及相关标准的制定。
2 航空发动机难加工材料高效切削技术
难加工材料高效切削加工技术是航空发动机制造中最为重要的一项先进制造技术。它是集高效、优质、低成本于一身的先进制造技术。在刀具的选择方面,应当合理选择与被加工零件在机械性能、化学性能、物理性能相匹配的新型高效刀具。不断优化刀具几何参数,优化切削用量。既要提高金属去除率,实现高效切削,又要保证合理的刀具耐用度,提高零件加工质量。
相对于传统的切削加工,其切削速度、进给速度有了很大的提高,而且切削机理也不相同。到目前为止,高效加工是在保证加工质量的同时采用高的主轴转速、大的进给量、大切深进行高效率的加工。高效切削技术还涵盖了刀具选配及运用技术、加工过程的智能化控制技术。在实际切削加工中,通过选择小切深、大进给等手段,减少工艺性应力集中,降低加工表面非均匀、非稳定残余应力,以提高零件的抗疲劳强度。
高效切削是一项系统工程。通过选择有良好技术状态,而且有足够功率和刚性的机床及工艺装备,提高整个切削系统的刚度,改善切削加工条件,避免或减少零件变形。通过合理分配各加工阶段加工余量,对被切削材料进行适当的热处理,改善了材料切削加工性。通过合理选择刀具几何角度,采用有效的冷却措施,做到既发挥刀具材料的切削性能,又保证一定的刀具耐用度,使切削顺畅。同时,获得较高的加工效率和加工质量。
切削加工性综合评价方面,从刀具角度评价其切削性能,从零件加工角度评价工件的可切削加工性,实现工件与刀具的合理匹配[4]。目前,基本掌握了常用航空发动机难加工材料的切削加工特性。同时对机匣、叶片、盘轴、整体叶盘等典型零件的一些关键工序,根据实际刀具磨损预测模型,建立了由诸多成本约束条件限制的数学模型。结合优化理论和加工实际,进行优化求解,得到了部分经济效益最大化的高效切削加工参数,并在典型件的加工工艺中获得了验证。
高效切削加工技术由于受诸多约束条件的限制,实践中的优化过程往往非常复杂,只能在满足约束条件要求的前提下,尽可能使切削状态接近于最佳状态。目前,切削参数的选择没有通过科学量化的角度去研究掌握这种高效切削工艺参数选择方式,容易导致切削用量保守、切削加工效率低、加工质量不稳定的现象。因此,必须以先进航空发动机对关键件、重要件研制需求为牵引,形成难加工材料典型零件高效切削基础技术研究能力。掌握有效提高加工精度、加工效率和加工表面质量的高效切削成熟工艺,向生产进行应用转化,实现稳定产品质量、缩短产品制造周期、降低制造成本等主要目标。
3 基于可持续发展的绿色切削技术
绿色切削加工技术得到各个国家的重视,绿色切削作为绿色制造的关键技术之一,主要指在生态大环境和加工现场小环境均无负作用(或负作用很小)的情况下,在加工过程中产生的少量“三废”(废气、废液和废渣)在链条末端可回收或自然降解,达到无公害的环保要求,对人和环境没有危害的切削技术。各国学者做了大量的试验研究工作,切削冷却润滑技术,如微量润滑技术、雾化冷却润滑技术、液体射流冷却润滑技术、低温冷风冷却技术、液态冷却干式切削技术及干式静电冷却技术等。其目的是为实现切削冷却润滑技术的少或无污染。由于微量润滑中润滑油是以10~50μm的雾滴形式存在,而且在高速气流的带动下进入切削区域,相比于传统的切削液具有更好的渗透性,更易在刀具与切屑之间形成润滑膜,降低切削温度、提高刀具寿命和改善加工表面质量。
在德国、美国和日本等工业发达国家非常重视干式切削的研究,该技术已成功地应用到生产领域,取得了良好的社会效益和经济效益,该项技术难点:
(1) 绿色切削技术的适应性分析。
(2) 绿色切削技术的技术特点研究。
(3) 绿色切削技术的技术适用范围。
(4) 绿色切削技术的应用。
4 切削过程监控技术
切削过程监控技术具有以下几个特点:
(1) 刀具在切削中所处状态的监测,即是否安装刀具、刀具所在坐标、刀具是否完好。
(2) 对刀具状态进行监测可以及时发现刀具破损情况,对数控设备和工件起到保护作用。
(3) 减少停车检查和换刀时间,减轻劳动强度,提高生产安全。
开展切削过程刀具监控技术研究工作,需要探索解决两方面的技术问题,一是因为刀具磨损量低于磨钝标准,造成没有充分利用刀具的实际寿命而带来浪费,增加制造成本的问题;二是因为刀具磨损量高于磨钝标准,刀具己经磨钝或破损,影响工件的加工表面质量和尺寸精度,甚至损坏机床的问题。该项主要技术难点:
(1) 切削过程信息包含有机床信息、工件信息在内的非切削过程信息互相混叠,形成同频干扰。解决切削过程监控的关键是得到监控所需要的目标信息。
(2) 监测的可靠性和准确性。刀具磨损的渐变性和刀具破损的突发性增加了信号分析的难度。不同的磨损形态对信号也会带来一定的影响,这些错综复杂的变化都将影响刀具磨损监测的可靠性和准确性。
(3) 多磨损状态下建模技术。
(4) 适合航空发动机切削加工的刀具寿命评估体系的建立方法。
刀具状态监控系统不但提高刀具本身的利用率,而且可避免工件报废和机床故障,节约成本。因此对刀具实际的磨损状态进行识别在解决航空材料的切削难题中起着至关重要的作用。
目前,生产现场利用数控设备提供的切削功率负载波动率对切削过程的稳定性进行切削过程在线监控在实际生产中具有一定实践意义。
5 振动切削技术
振动切削按照其振动源频率分为高频振动和低频振动。特别是在难加工材料切削加工中,采用超声或高频振动切削改变了传统常规的金属切削方法。振动切削不但使难切削变成能切削和易切削,零件表面精度和质量得到提高,而且提高了刀具的使用寿命。
该项技术的难点在于:为了达到振动切削效果,需要解决振动频率、振幅与不同被加工材料切削参数的合理匹配问题。
6 切削加工表面完整性控制技术
零件切削加工表面完整性包含两方面的内容:一是与表面形貌或表面纹理组织有关的部分,研究零件最外层表面与周围环境间界面的几何形状,包括表面微观几何形状与表面缺陷等表面特征,属于外部加工效应,通常用表面粗糙度等来衡量;二是与加工表面层物理力学性能状态有关的部分,研究表面层内的特性,属于内部加工效应,包括表面内的残余应力、变形强化、加工硬化、金相组织变化、裂纹等技术指标。
高推重比发动机使用了多种高性能的新合金材料和新结构。这给零件加工和表面完整性控制带来新的困难和要求,需要预先进行系统的试验研究。国内切削加工表面完整性技术还在探索阶段,加工参数对加工表面完整性的影响、加工表面完整性的检测与评价技术还有待开发研究。
切削加工表面完整性技术是抗疲劳制造技术体系中最为重要的组成部分。从航空发动机的使用过程和故障分析得知,各种形式的疲劳破坏几乎都集中在零件的表面或接近表面的地方。当零件处于腐蚀介质和交变载荷的共同作用下,较差的表面完整性将会加快零件的疲劳破坏,降低零件的使用寿命。
随着航空发动机抗疲劳制造技术的发展需求,对航空发动机关键零件的已加工表面的质量和状态提出更高的要求。航空发动机零件对于切削表面完整性及可靠性要求极为苛刻。少于预期寿命的切削刃失效和破损将对零件表面完整性造成致命的损害,进而影响零部件乃至整个航空产品的可靠性。因此对于刀具寿命的准确预估成为航空产品加工中一个无法回避的问题。
已加工零件表面完整性涉及到工件材料、刀具材料、刀具几何参数、切削参数、机床设备性能及装夹系统性能等多因素的综合影响。即使工件相同,但不同的切削方式,不同的加工刀具,不同的切削参数,加工后产生的表面完整性也大不一样。切削加工表面完整性控制技术是要通过试验探索得出上述综合影响因素对零件表面粗糙度、加工硬化,残余应力等的影响规律。利用这些规律完善切削工艺,使零件具有更好的表面质量和高的抗疲劳强度。
7 全程序无干预切削加工技术
“全程序无人干预”加工,是指被加工工件安装在数控机床后,在没有人工干预的状态下,一次程序启动完成加工、检测过程。它将过去产品质量和加工效率依赖于人员技能水平的传统加工形式,转变为由全程序不干预加工控制和设备功能进行保证的新形式。实现航空发动机零件自动化、智能化切削加工。全程序无人干预加工的主要特点:
(1)零件数控加工程序优化后,切削参数能满足无干预(或减少干预)加工的需要,加工过程按100%倍率进行,操作者无需调整进给倍率。
(2)增加或调整进退刀位置,方便加工过程中的刀片更换和尺寸测量,操作者无需手动调整停刀位置。
(3)零件加工工序完成刀具寿命统计,实现切削加工过程完全自动换刀,操作者无需过多监控加工过程。
(4)通过固化加工刀柄、刀具、装夹,控制过程输入值的正确性,保证零件加工的主要尺寸及配合尺寸质量可控,靠近尺寸中差
(5) 能充分利用M00(暂停)MSG (信息提示),等机床功能,提升无人干预加工过程的适应性。
“全程序无人干预”技术不仅预置防错纠错功能,消除切削加工过程中的随机误差,增强操作系统的可靠性,同时还需进一步挖掘潜在的设备功能,逐步融合自动对刀、在线测量和自动补偿技术,减少加工中间环节,实现单人多机操作,提升生产效率,保证产品质量,降低制造成本和操作人员劳动强度。全程序无干预切削加工涉及自动换刀、刀具切削时间统计、刀具寿命监控、在线测量技术:数控仿真加工技术。
航空发动机切削技术发展策略建议
1 运用新型高性能刀具,完善硬件、软件配置
航空发动机零件结构复杂,大量的薄壁件,加工变形严重,对刀具的刚性、精度要求高。高性能刀具是提高航空发动机切削技术水平的强劲动力。因此应用高性能刀具解决切削加工问题是必然趋势。同时要配备先进的刀柄等硬件和加工仿真所必须的软件。要针对涡轮机匣、风扇机匣、涡轮盘、风扇盘、长轴、叶片、叶轮等典型关键零部件,提供完整的刀具配套和解决方案。以先进航空发动机对关键件、重要件研制需求为牵引,形成难加工材料典型零件高效切削基础技术研究能力。掌握有效提高加工精度、加工效率和加工表面质量的高效切削成熟工艺,向生产进行应用转化,实现稳定产品质量、缩短产品制造周期、降低制造成本等主要目标。
2 突出重点,以点带面,解决关键
切削难切削材料时由于切削力大,应选择有良好技术状态,而且有足够功率和刚性的机床及工艺装备,合理分配各加工阶段加工余量,避免零件产生变形。对被加工材料进行适当的热处理,通过热处理来改变被加工材料的性能和金相组织,达到改善材料切削加工性的目的。在对零件材料进行分级归类的基础上选择合适的刀具材料,确定合理的刀具几何参数。合理选择选择并优化切削用量。
研究编程技术和针对各种机床的后置处理技术。解决大型整体结构件和弱刚性零件的加工变形问题。研究各种工艺条件对变形的影响,以及减小加工变形的工艺措施。突出重点,以点带面。例如:整体叶盘、叶片和机匣这三类零件可以集中80%以上的关键技术,一旦突破,其他零件均可采用。着重对零件的关键加工工序进行研究,测定相应的已加工表面层状态(表面粗糙度、冷作硬化、残余应力及表面金相组织变化等),经疲劳试验后,确定控制零件表面完整性的技术条件,完善切削工艺。
研究高性能切削加工的刀具技术和高效切削的有效途径。对零件材料进行分级归类;选择合适的刀具材料;确定合理的刀具几何参数;根据切削用量的选择原则,合理选择切削用量。
3 建立并开发智能切削数据库系统
通过对加工特征进行分析和分类,结合对刀具结构的研究,确定基于切削加工特征的刀具选择原则和方法。建立基于切削加工特征的刀具选择数据库系统,实现刀具及其切削参数的智能选取。航空发动机零件典型工艺特征的提取必须建立在多次仿真和试验的基础之上。通过航空发动机零件典型工艺特征提取、切削仿真分析及典型试件验证试验,提供典型工艺设计及数控加工之中关于刀具选用、切削参数选择、切削工艺优化方面的解决方案。
结束语
航空发动机制造企业应结合自身的特点确定切削技术发展重点,研发关键技术,突破典型零件切削综合优化试验及验证技术、基于工艺特征的切削数据库系统技术、切削物理仿真、高速高效切削、精度与表面质量控制、工件变形预测与补偿等技术。以切削效率、切削加工质量、切削经济性为切削优化目标,开展典型工艺特征切削数据库、切削物理仿真、切削表面完整性研究。建立综合优化试验设计体系和切削仿真试验验证体系。大力加强航空发动机切削加工过程控制技术、工艺研究和建设。强化培训,促进产、学、研、用有效结合,实现航空发动机制造技术水平不断提升。
声明:本网站所收集的部分公开资料来源于互联网,转载的目的在于传递更多信息及用于网络分享,并不代表本站赞同其观点和对其真实性负责,也不构成任何其他建议。本站部分作品是由网友自主投稿和发布、编辑整理上传,对此类作品本站仅提供交流平台,不为其版权负责。如果您发现网站上所用视频、图片、文字如涉及作品版权问题,请第一时间告知,我们将根据您提供的证明材料确认版权并按国家标准支付稿酬或立即删除内容,以保证您的权益!联系电话:010-58612588 或 Email:editor@mmsonline.com.cn。
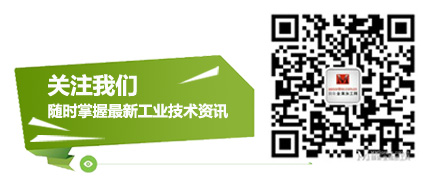
- 暂无反馈