如何确保设计无误差?全彩打印机助力通用汽车打印关键部件
Vauxhall Motors公司是英国通用汽车的分公司,在生产过程中,他们需要不断地改善汽车的质量和提升生产能力来缩减生产时间和降低成本。
在2014年5月,公司开始引入改良的工程架,革新型的变异模型需要被加工,所以一个新的部件将要被用来在整个生产过程中支撑车体,使得装卸更加容易。这是一个关键的部件,它必须完美适配机械来产生正确的间隙也要避免生产过程中的对车体的伤害。
汉姆•库柏是车间输送系统的高级规划工程师,他知道这些部件是多么的关键,并且为了生产的顺利,这些部件必须非常精准。由于最后的部件是铸钢材质的,成本高昂,需要花费很长时间来制作。他知道如果出现一个小错误也会导致新设备的引入延误6个月甚至更多。
这个团队联系了蒂姆•沃里克,他是InfusionTech公司的总经理,这个公司专门进行部件的后期处理以使部件更加坚固,耐热和拥有其他在原件上没有的功能。蒂姆建议利用ProJet 660全彩色打印机和他们的注液机来制作出可以在测试时,精确且坚固的支撑起整个车体的部件。
“3D打印平台使用的石膏材料在原始状态是不太坚固的”,蒂姆提到,“但加入我们使用我们的工具材料,我们可以制作出满足严苛需求的非常坚固耐用的部件。”
在收到3D打印部件后,汉姆和Vauxhall的团队把他们安装在工程架上并开始测试。汉姆说部件表现的非常完美,能够使整个团队达到目的
•3D打印使我们在下铸钢块的订单前可以先检查车体部件的位置是否到位,是否符合 CAD设计的精确性
•打印出来的块状物让我们可以成功修改支撑车体的自动装载站,防止出现车体在工程架上打滑。
•由于打印的块状物的使用,当自动装载其中一个变体模型时,我们发现了一个前定位销的高度有问题。因此我们降低了定位销的高度并调节了自动装载站的一些方面。
•打印出来的块状物让我们可以修改支撑车体的自动装载站,防止出现车体在工程架上打滑。
•这个块状物让我们的加工部门可以为每个变异模型在车身底部的密封机器人编制程序。
当在测试时,发现设计需要被修改来降低定位销的高度,汉姆和他的团队认为已经是时候来下订单来制作铸钢块了。这些部件会花费数以万计的美元,并且需要花将近6个月来制作。他们不得不需要让一切的设计数据都是最完美的。
“这个过程进行的很顺利”,他这样评论道。“我们需要测试部件,通过3D打印我们得到了完美的解决方案。”
Vauxhall的团队评估认为这个过程非常节约成本,减少了设计时间和在工程架上应用这些变更的时间,并且减少了极大的风险。
“如果我们没测试这些部件,并且用错误的设计下了订单制作,就会造成6个月的延误和10000英镑的损失。但因为我们使用了3D打印的部件,我们可以确保这些更改的设计是可以完美运行的,这样一来我们就可以去下单订购铸钢块了。”
另外,他还说到,“能够在流程中给机器人尽早编程也给我们带来了巨大的优势,这不像以前那样直到钢块拿到才发现是不合格的,使我们耽误了更多时间。”
“我们会继续使用3D打印,并且把3D打印应用到我们的设计和工程工艺上.”
声明:本网站所收集的部分公开资料来源于互联网,转载的目的在于传递更多信息及用于网络分享,并不代表本站赞同其观点和对其真实性负责,也不构成任何其他建议。本站部分作品是由网友自主投稿和发布、编辑整理上传,对此类作品本站仅提供交流平台,不为其版权负责。如果您发现网站上所用视频、图片、文字如涉及作品版权问题,请第一时间告知,我们将根据您提供的证明材料确认版权并按国家标准支付稿酬或立即删除内容,以保证您的权益!联系电话:010-58612588 或 Email:editor@mmsonline.com.cn。
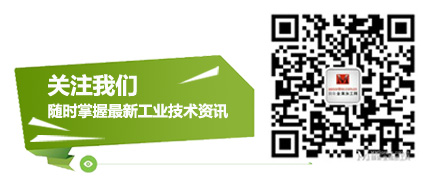
- 暂无反馈