金属3D打印将改变激光器未来设计方式?
近日,美国劳伦斯·利弗莫尔国家实验室(LLNL)的研究人员正在探索使用金属3D打印技术来为先进的激光系统达到高强度、低重量的结构——他们称这将改变激光器未来的设计方式。
在LLNL内部的一个实验室指导研发(LDRD)项目中,物理学家Ibo Matthews和他的团队正在使用一台研究用的金属3D打印机进行实验,据天工社了解,这款金属3D打印机目前全世界只有4台,它使用了一套定制的软件平台,可以实现前所未有的设计控制。
据悉,这款基于粉末床的激光熔融3D打印机是由弗劳恩霍夫激光技术研究所(ILT)和德国初创企业Aconity 3D共同制造的,并于2015年12月安装在LLNL。后来,LLNL的工程师们在机器上又增加了诊断模块和高速摄像机以研究热辐射,并对3D打印中零部件的表面进行拍照。Matthews称,这样的改装可以帮助研究人员确定在3D打印过程中缺陷或者变形是如何出现的。
“这套系统非常灵活,它使我们可以更改任何想要的参数。”他说。“我们正在建立置信度,如果有任何缺陷发生,我们的目标是用户会在构建结束后拥有一个3D“地图”,这个“地图”会告诉用户缺陷发生在哪里和发生了什么。”
目前,Matthews和他的团队已经在美国国家点火设施(NIF)和定向能源项目的支持下获得了关于激光材料处理和相互作用的知识,并正在此基础上进一步开发新的金属3D打印方法。而且他们的这项工作也是扩大NIF&光子科学(NIF & PS)的激光应用范围,以及保持LLNL在激光物质相互作用科学领域竞争力的整体战略的一部分。此外,NIF科学家们也对于金属3D打印平台在激光领域的应用感兴趣——不仅限于NIF,还包括那些需要非常轻量级部件的机载遥感和航空扫描系统方面的应用。
“通过对3D打印进行精密、预测性的控制,你可以将刚度放在需要的地方。”防御技术部的NIF&PS项目主任Mike Carter说:“你可以为光纤激光器及底座创建具有功能梯度的结构,这是用传统制造方式不可能实现的。”
实际上,NIF已经开始将3D打印的金属部件用在其激光器结构中了。但是,为了能够更加常规地在关键系统中使用他们,研究人员必须保证每个部件都是好的。
于是,为了加快这一认证过程,实验室工程师正试图通过采取完全不同的方法缩短开发阶段——这是一种基于计算机模型的“前馈”方法,而不是试错。如果成功,LLNL物理和生命科学局的Wayne King称,这项研究将能够从根本上改变金属部件——包括那些在光学系统中使用的——的设计、制造方式。
“除非你采取基于科学的做法,否则你不会知道为什么A部件与B部件不一样。”King说:“我们正在推动最为前沿的科技,实际上,我们已经看到了该技术的一些应用。”
在从去年开始的LDRD项目中,Matthews和他的团队将会把金属3D打印、高保真光学诊断与高性能计算结合起来,为他们金属3D打印零件创建更高的置信度。这个项目计划要进行三年的时间。
“我们想要做的是在模拟的基础上推动这个过程,并在光学监控的基础上创建一种认证的“数字指纹”,以确保部件在第一次3D打印时就是正确的。”Matthews说。
声明:本网站所收集的部分公开资料来源于互联网,转载的目的在于传递更多信息及用于网络分享,并不代表本站赞同其观点和对其真实性负责,也不构成任何其他建议。本站部分作品是由网友自主投稿和发布、编辑整理上传,对此类作品本站仅提供交流平台,不为其版权负责。如果您发现网站上所用视频、图片、文字如涉及作品版权问题,请第一时间告知,我们将根据您提供的证明材料确认版权并按国家标准支付稿酬或立即删除内容,以保证您的权益!联系电话:010-58612588 或 Email:editor@mmsonline.com.cn。
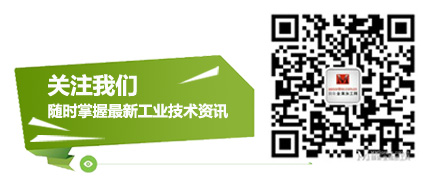
- 暂无反馈