工件直接夹持提升生产效率
工件直接夹持提升生产效率
工具和模具制造通常具有单件生产和小批量生产的特点,因此会涉及到许多非常复杂的工艺。现在,这一切都将发生改变。雄克位于德国曼根(Mengen)的工厂主要负责车床卡盘技术和模块化工件夹持系统,其总经理Markus Kleiner在采访中介绍了一款直接夹持工件的模块化系统的开发过程,以及用户在小批量工业生产中应注意的事项。
Markus Kleiner,Heinz-Dieter SCHUNK GmbH & Co. Spanntechnik KG(雄克曼根工厂)总经理
Kleiner先生,“工件直接夹持”几年前由雄克首先提出,您怎样理解这一概念?
工件直接夹持,就是说用户不再需要诸如多爪卡盘等传统的夹持设备。在准备过程中,首先将模具板、复杂形状的部件和其他工件的底面在同一水平上磨平,然后按规格加工螺纹孔,并安装快换系统的定位销。准备完毕后,在机床内部的快换夹持模块上,可以在几分钟内完成零件更换,并根据要求精准夹持。
工件直接夹入快换夹持模块,模块升高更方便机床主轴操作。
这种夹持原理有何优势?
与传统的夹持解决方案不同,直接夹持不会受到卡爪或夹具轮廓的干扰,能非常方便地对工件进行五面加工,还可以减少机床在生产中的闲置时间,如设置、改装和调整或零点确定等。在汽车行业应用中,外壳冲压模具的生产更换时间可从原来的约两小时缩短到15至20分钟。与此同时,加工中心的有效使用时间比例也提升至80%。一台固定设备原本所需的设置时间越长,实际的加工操作时间越短,则改进夹持方案的投资回报速度就越快。同样,如果工件需要在短时间内反复修正或加工,也能取得类似的效果。利用现有的螺纹孔,工件可以立即在设备上精准更换。
在加工热通道分配器时,将工件位置提高使机床主轴更易触及。
所以最重要的问题是效率?
不仅如此。如果工厂缺少熟练操作员,那么我们必须寻找流程标准化设置的方法,从而尽可能地减少操作错误。工件直接夹持创造了理想的先决条件,因为它的设计已经考虑到减化操作员所需掌握的专业知识,使许多故障从根源得到避免,机床操作员的责任明显减轻。即使落下了一个芯片,整个铣削过程也能准确模拟并提前预知。
直接夹持同样也适用于旋转操作。
工件直接夹持适用于哪些应用?
直接夹持原理在单批或多批次生产中都具有十分明显的成本优势。现在,直接夹持也成功应用于单个零件的工模具制造。在汽车制造中,一般使用两次夹持便可完成大型工件加工。不仅提高了生产力,还改善了精度。然而,很多人尚未了解的一点是,直接夹持还可以在大批量生产中实现合理化效应。这得益于工件可以借助一个定位销执行不同的操作,如机加工、清洗安装、测量和打标等。此外,夹持原理还适用于自动化机床上下料。总而言之,只要定位销能直接拧在工件上,工件直接夹持便会是一个理想的选择。
利用直接夹持的方法,工件可以在几秒钟内完成更换。
既然VERO-S标准模块已经拥有上述功能,那为什么还要开发另外一个模块化系统呢?
过去几年里,许多用户和雄克一直在努力尝试寻找提升工模具制造效率的方法,其中包括很多大型汽车制造商、模具制造商和热通道专家。大多数情况下,都是通过改造雄克VERO-S标准模块或添加单独的定制化部件。在去年的米兰EMO展会上首次推出了用于工件直接夹持的雄克模块化VERO-S系统工具包,通过系统地分析并整合在众多项目中的经验知识,我们最终形成了这样一个标准化的模块。
在夹具塔上直接夹持:图中的封闭框架可被快速夹持并从五面加工。
这个模块化系统包括哪些组成部分?
该系统包括了标准化底板、夹持和叠加模块。无需任何昂贵的特殊解决方案,夹持柱最低80mm,以10mm的精确间距向上调整。更重要的是——模块可以随时快速添加或移除。所有接口都带有一个不限范围的短锥定心机构,它位于单个组件之间,能够确保重复精度低于0.005 mm。如果高度差异依然存在,还可以通过无限可调的液压夹持补偿元件连接。
雄克VERO-S模块化夹持系统的夹持柱高度能够根据具体的工件灵活调整。
能源消耗方面呢?
所有雄克VERO-S模块夹持都通过弹簧力完成,因此为零耗能。系统自动锁定。即使压缩空气系统失效,模块依然能够牢固夹持。
用户如果希望采用直接夹持工艺,他们需要注意什么?
工件直接夹持首先应考虑工程设计。以往的经验表明,工程设计和生产之间的联系越紧密,效果就越好。理想情况下,要先系统地找出单个工件之间的共性特点。在此基础上建立工件分类的集群,然后对其加工进行进一步的统一和标准化。一般而言,60%到80%的部件可以按照这种方式转化为标准化工艺。根据相关要求和具体的设备状况对每个快换夹持解决方案进行相应的调整同样重要。通过适当调整,一般都可以找到适用于其他工件的高效解决方案。雄克拥有全球最广泛的固定式工件夹持模块,能够为此提供最佳先决条件。
只需简单几步的手动操作,便可将雄克模块组合用于直接夹持。
这个整体解决方案会不会非常昂贵?
既是也不是。工件夹持系统的配置不可能一蹴而就。提升生产效率的意愿至关重要,从设计经理到机床操作员在内所有相关人员都必须具备这种共识。而其成效也是十分显著的,在实施的过程中,很多辅助性操作会逐渐取消、多种作业会整合,也会形成很多新的工艺和工具使用惯例。由此可以提高效率,减少操作失误,返工时间也可大幅缩短。由于工件夹持机床外部进行,与生产过程同步,加工时间得以更高效地利用。根据零件范围,有效加工时间最高可提升80%。由于夹持应用实现标准化,进而整体规划并模拟,规划时间也可同样缩短。长期以往将显著节约生产成本。
雄克VERO-S夹持柱的模块化设计让工件易被触及,适应具体的夹持场景。标准化叠加模块精确细分,可灵活调节夹持高度。
微米级精密模块化系统引领工件直接夹持潮流
- 雄克模块化工件直接夹持系统由适用于机床工作台的VERO-S WBD基体、VERO-S WDN夹持模块(直径99毫米)、可自由组合的VERO-S WDS叠加模块(结构高度30毫米至50毫米)以及液压夹持VERO-S WDA补偿元件组成。
- 单个模块之间的夹持连接具有高达25,000 N的极强下拉力,适用于较高的切割参数。
- 所有接口都带有一个不限范围的短锥定心机构,它位于单个组件之间,能够确保重复精度低于0.005 mm。
- 内置的空气通孔,在无需外部媒介通孔的情况下即可驱动夹持模块,并监控工件是否就位。
雄克精密机械贸易(上海)有限公司
上海市闵行区春东路420号1号楼1楼
电话:021-54420007
传真:021-54420067
info@cn.schunk.com
www.cn.schunk.com
声明:本网站所收集的部分公开资料来源于互联网,转载的目的在于传递更多信息及用于网络分享,并不代表本站赞同其观点和对其真实性负责,也不构成任何其他建议。本站部分作品是由网友自主投稿和发布、编辑整理上传,对此类作品本站仅提供交流平台,不为其版权负责。如果您发现网站上所用视频、图片、文字如涉及作品版权问题,请第一时间告知,我们将根据您提供的证明材料确认版权并按国家标准支付稿酬或立即删除内容,以保证您的权益!联系电话:010-58612588 或 Email:editor@mmsonline.com.cn。
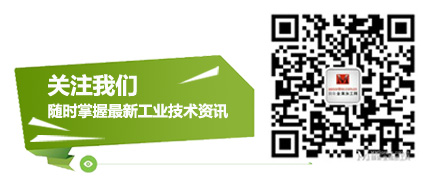
- 暂无反馈