NC-locator点焊机器人的数字化生产线
中国汽车产业的飞速发展,对汽车的产量、质量以及车型换代的时间都提出了越来越高的要求,在淘汰人工作业进行自动化生产线改造的过程中,引入工业机器人技术,将各种先进的数字化工具运用到机器人白车身点焊自动化生产线的设计及制造中,形成高自动化及高适应性的生产线,已成为整个汽车制造业的必然。目前,数字化技术已广泛应用在首钢莫托曼机器人有限公司的机器人白车身点焊项目中。
机器人白车身点焊的特点
白车身焊接工序繁多,工艺复杂。目前,传统的人工焊接方式正逐渐被淘汰,工业机器人在白车身点焊生产线中的应用日益增加。与传统的手工焊接相比,工业机器人具有以下优点:
1. 提高焊接质量
使用手工焊钳人工焊接时,操作者由于疲劳等原因难以保证焊接工作的稳定性,而机器人焊接可以保证焊接位置、焊接角度的一致性,不会出现错焊、漏焊。
2. 提高劳动生产效率,改善人工劳动条件
点焊机器人可以在恶劣的坏境中长时间工作,使操作者远离弧光,飞溅。而且随着机器人技术和焊接技术的发展,焊接速度不断提高。
NC-locator选型
3. 灵活性高
通过简单的机器人程序调整适应于不同的产品。而且,点焊机器人程序可以离线编制,大大缩短在线调试时间,从而缩短产品改型换代的周期。
一个机器人白车身点焊工作站,由6台机器人组成,每台机器人焊接20~30个焊点,生成节拍约为90s,可以24h连续工作。
机器人白车身点焊生产线中的数字化需求
据统计,一辆轿车的白车身在焊装过程中要经历3000~5000个点焊步骤,用到100多个大型夹具,500~800个定位器。从规划到具体实施,白车身点焊生产线是一个庞大而复杂的过程。
以往的白车身工艺规划是串行方法,有时生产加工之后或者调试时才能发现问题,造成人力财力的浪费。需要采用数字化软件对项目各环节进行设计、管理和跟踪,使得各个工作环节有条件并行,有效缩短了项目周期;同时引入底层数据库技术,保证了资料的惟一性,解决了数据冗余的问题,避免了由此产生的设计和管理纰漏。
生产线柔性化成为发展趋势,生产线需要满足多车型混线生产,这就对传统机器人示教方式提出了挑战,车型的增加使示教工作量随之增加,而主机厂对效率的追求又希望在保证程序精度的条件下,尽可能减少现场示教时间。同时,车型不断更新换代,也要求缩短现场调试和试运行的时间,这就对生产过程的数字化仿真提出了需求。
此外,随着点焊生产线自动化程度的增加,一些新设备投入使用,对新设备可行性的验证没有规律可循,利用数字化方法检验既可保证可用性,又能节约成本。安川电机生产的白车身自动定位支撑装置NC-locator装置具有双向3自由度,能够满足自动适应不同平台车型定位支撑的要求。图2为仿真软件中,对适用于不同车型的NC-locater进行选型确认。
数字化在机器人白车身点焊生产线中的应用
以下从4个方面详细介绍数字化技术在机器人白车身点焊生产线中的应用。
1.前期方案阶段
从厂家得到车型和工装夹具三维数模、焊点信息和生产节拍等资料后,将需要的资料导入Siemens PLM Software旗下Tecnomatix数字化工厂中的Process Desinger软件,可以进行工艺流程设计、作业时间分析、生产线、单元平面和立体布局等操作。初步确定机器人数量和型号,是否有行走机构等前期方案。
适合工件形状的焊钳
2.工艺规划和焊钳选型
初步分析工艺文件之后,将焊点分配给各个工作站内的机器人,再根据每个站内机器人对应焊点位置,进行焊钳选型工作。工艺规划和焊钳选型都是复杂而细致的工作,通常需要不断修改和反复。这样的工作特别适合用数字化的方法进行。如对于MOTOMAN机器人,根据焊点和工件的位置关系,使用MotosimEG软件或者ROBCAD软件,在仿真环境中从焊钳数据库中选取一把大致可达的焊钳,然后再针对每一个焊点进行焊钳可行性验证。之后对焊钳提出修改意见,确认焊钳的最终形式。图3为一把适合工件形状的焊钳。对于一些特殊工位,一台机器人还需要有2~3把焊钳,在工作过程中进行换钳,才能完成工艺规划中的焊接任务。
焊钳选型工作也是对工艺规划的一个验证,如果焊钳形状无论怎么修改也不能满足工艺分配的所有焊点,就需要更改工艺文件,进行站内机器人之间,或者是工作站之间的焊点转移。这样在仿真环境中不断验证、通过数字化方法得到工艺文件可以达到全局最优化的目的。
3.离线程序编制和节拍验证
对于MOTOMAN机器人,离线程序的编制可以在MotosimEG软件或者ROBCAD软件中进行。离线编程是数字化技术在点焊生产线中的一种重要应用。在离线的状态下生成机器人程序,可以与现场工作并行进行,而不用占用现场大量的调试时间。离线程序可以直接生成点焊命令和点焊的各个参数,包括:间隙文件序号、伺服焊钳序号、压力条件文件序号、焊接条件序号、焊机启动时序以及焊接条件组输出,节省了现场输入这些参数的时间。
离线编程具有很强的规划性,尤其对一个站内有多台机器人的情况特别适用。可以在离线的环境中安排焊接路线,设置干涉区,检查节拍是否满足要求。如果节拍不满足,再进一步对机器人动作姿态,路径等进行优化,还可以进行不同工作站之间的焊点转移,平衡整个生产线的节拍。这些工作提前在仿真的环境中完成之后,不仅可以提高现场的效率还可以保障示教人员的安全。
4.现场程序误差补偿
完成了前期工作之后,离线程序如何在现场使用,使现场示教时间尽可能缩短,是提高示教效率,缩短项目周期的一个重点。由于现场安装位置和布置图中的理论位置相比总会有误差,离线程序不能直接使用。这就需要对离线程序进行校准。安川公司针对MOTOMAN机器人,专门开发了一款软件MOTOCALV32,可以进行工件安装位置的校准。除此之外,还可以进行机器人、工具尖端点等的校准。
结语
在机器人白车身点焊自动化生产线项目的设计和制造过程中,以数字化规划、设计及仿真等软件为主体,可以有效缩短项目周期、压缩项目成本。从根本上满足汽车生产的多品种、多批量的柔性生产需要,提高白车身点焊作业生产效率和质量,促进汽车产业向自动化方向发展的进程,提高民族产业在国际上的竞争力。
声明:本网站所收集的部分公开资料来源于互联网,转载的目的在于传递更多信息及用于网络分享,并不代表本站赞同其观点和对其真实性负责,也不构成任何其他建议。本站部分作品是由网友自主投稿和发布、编辑整理上传,对此类作品本站仅提供交流平台,不为其版权负责。如果您发现网站上所用视频、图片、文字如涉及作品版权问题,请第一时间告知,我们将根据您提供的证明材料确认版权并按国家标准支付稿酬或立即删除内容,以保证您的权益!联系电话:010-58612588 或 Email:editor@mmsonline.com.cn。
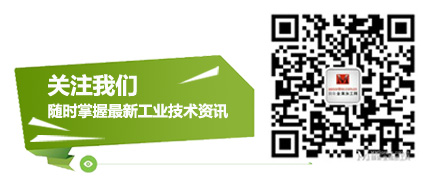
- 暂无反馈