工业机器人 混战中的追赶
“中国制造2025”概念的提出,尤其是智能制造和智能工厂的装备需求,为“进击的工业机器人”们打了一针兴奋剂。
银白色待焊车架随输送带停下,紫色的机械手稳稳将其卡住定位,几台亮黄色的机器人齐拥而上,瞬间火花四溅,各焊点逐一完成,一分钟内被送往下一个工作岛,同时也迎来下一个待焊车架。
这就是发生在上汽通用武汉工厂的焊装车间内的日常一幕,该车间2015年刚刚投产,目前拥有452台机器人,自动化率已高达97%。
在2011年,机器人在中国的销量还仅有2.2万台,到2014年已跃升至5.7万台,中国连续两年稳坐全球机器人市场首位。而机器人从事的工作岗位,也由一开始重体力、重复性以及可能会对人体健康产生影响的工位,慢慢发展成“无人工作岛”、“无人生产线”、“无人车间”。
时至今日,机器人在“中国制造”中的角色,遍布钣金加工、抛光打磨、喷涂、分拣、包装码垛等各个生产工序。“只要你能想到的行业,都可以用到我们的机器人。”上海发那科机器人有限公司(下称上海发那科)一位员工向记者表示。
早在2012年,中国已就机器人产业开始国家级的战略布局,可以说,正是这样的政策催化,以及频频出现的“用工荒”,带动了机器人市场此前三年的爆发性增长。如今“中国制造2025”概念的提出,尤其是智能制造和智能工厂的装备需求,又为“进击的机器人”们打了一针兴奋剂。
政策“馅饼”
对于《中国制造2025》中提及的重点任务——“推进制造过程智能化”一项,东莞力生机械设备有限公司(下称力生公司)董事长张高强可谓烂熟于心。文件中提出:“在重点领域试点建设智能工厂/数字化车间,加快人机智能交互、工业机器人……的应用,促进制造工艺的仿真优化、数字化控制、状态信息实时监测和自适应控制。”这被他视作公司未来的发展方向。
张高强介绍,力生公司已经在5月成立了一个培训中心,主要就是对员工进行机器人应用的培训;此外还计划增设工程中心,针对视觉应用和控制系统进行自主研发。他甚至已经打算将公司名称改为“广东力生智能”。
这家成立于1996年的生产线供应企业,正由原本的机械设备行业,全面向智能制造业转型。
像力生公司这样“半路出家”的企业,在机器人行业比比皆是。东莞机器人技术协会会长蒋仕元向记者证实,他所知的绝大多数机器人相关企业,崛起于2014年东莞“机器换人”政策推出之后。
2014年1月,《工业和信息化部关于推进工业机器人产业发展的指导意见》(下称《指导意见》)首次明确提出了“机器人密度(每万名员工使用机器人台数)达到100以上”的目标。2013年,中国机器人密度仅为30。
在用工密集的长三角、珠三角各地,针对“机器换人”项目的补贴政策纷纷出台。
“从中央到地方乡镇,都有配套的政策支持。据我所知,购买国产的机器人,可以(从东莞市获得)补助15%。镇一级还有配套补贴,比如说拿到市里100万元补贴,不同的镇会拿出0.2、0.3、0.5,甚至是1∶1的配套补贴。”蒋仕元介绍,正是在这样的政策驱使下,“有些企业为了让自己‘高大上’,都是不惜血本。特别是对一些小的企业来说,有补贴当然最好”。
其他如广东广州、中山,浙江嘉兴、杭州,江苏昆山、宿迁等地,也先后推出了“机器换人”的持续政策。
“馅饼”不仅落在机器人应用企业头上,不少企业瞄准了机器人的销售和集成市场。
蒋仕元回忆,在2012年至2013年间,他供职某3C制造企业时,作为首先开始“机器换人”项目的企业之一,公司想要在国内找一家合适的机器人集成商还十分困难。
为了建成首个无人车间,公司耗资上亿元,所有设备均由国外进口,“就连调试的工程师都是国外派过来的,光工资就不得了”。
情况仅在2014年一年间就发生了翻天覆地的变化。2015年1月,东莞市机器人技术协会副会长罗百辉参加某行业研讨会时公开声称:中国从事机器人业务的企业,正在以每周两家的速度不断递增。
价格硝烟
作为机器人产业研究者,罗百辉统计后认为:在4000多家机器人厂商中,至少75%以上是系统集成商——即自己不生产机器人,而是以购买机器人制造企业的本体,为客户提供系统性的解决方案,行内俗称“交钥匙工程”。
在行业的疾速发展中,价格被急剧压缩,现在国内一些企业的报价,几乎只是原来外企的一半。这样的价格战对于应用企业来说求之不得。
蒋仕元在原3C企业时所设的无人化车间,要收回成本耗时十分漫长。对当时的他和同事们来说,投资这条生产线,很大程度上是为了争取客户,“比如说有些苹果的订单,你没有高端设备,它就不给你做”。
在竞争充分的2014年,“通常把三年以内回本当作一个标准。但也要看什么样的企业、生产什么样的产品,有的可能几个月就可以收回成本。比如一条线原本要十几个工人,改造后可能就只需要两个人,它的回报率就很明显了”。
激烈的价格之争中,甚至有企业提出了“不回避价格战,主动发起价格战”的口号,让这个还算新兴的行业,发展初始就已硝烟弥漫。
自2012年开始介入机器人系统集成的张高强坦言,力生公司在这一业务领域的利润率仅有一成。
东莞机器人技术协会有200多家会员企业,其中至少200家都是系统集成商。作为协会会长,蒋仕元看到的更多。“跟原来的LED产业一样,政府一号召,有市场,大家就一窝蜂上,很多跟自动化不相干的企业都转做机器人。但现在已经可以看到有些没有实力的企业搞不下去了。”
他分析,机器人系统集成,是一个对人力资源要求很高的产业,缺乏高端人才,导致不少企业无法承揽大型项目,甚至难以为继。“我们估计在三年以内会有一次大洗牌。”
虽然一些中小型企业倍感压力,但大型企业仍然保持着较高的利润率。上海发那科虽为中日合资企业,公司的经营管理由中国人负责,系统研发和集成亦在中国进行,仅机器人本体购自日本母公司。2014年,这家企业是上海纳税百强之一。
中国最大的本土机器人企业沈阳新松机器人自动化股份有限公司,亦以系统集成业务为主要商业模式,其2014年工业机器人的业务营收将近4.77亿元,毛利率达37.89%。
大型企业和中小型企业出现如此差异,既有系统集成能力的原因,也受其议价能力影响。“像我们这样的企业,一年总购买量100台左右,在‘四大家族’面前,基本是没什么议价能力的。”张高强诉苦道。
所谓“四大家族”,是指机器人生产领域的传统四强企业,包括德国库卡、瑞士ABB,以及日本的发那科和安川电机,这几家企业占据了全球机器人行业一半市场,更是牢牢把握着中国市场。在2014年5.7万台的总销量中,国内企业销售的机器人总量不超过1.7万台,不足三成。
上海发那科总经理钱晖认为,除了性能真正对客户选择造成比较大影响的是故障率。
“大家都是在生产线上用,可能一条生产线用300台-400台机器人。现在发那科的机器人,可以做到125个月才出一次故障,已经很好了。但400台机器串起来的生产线,算下来每月都会有四次故障。实际上无障碍运行能达到8年的企业是很少的。”但他补充称,发那科机器人的故障率远低于均值。
蒋仕元透露,“实际上大家都考虑过,应该用民族产品,但国货的性能是跟四大家族的没得比。
比如说无故障运行时间,国外可以达到10万甚至15万小时,国内某个知名品牌就只能做到5000小时。精密度也有差距,有的调试可以适应生产,但是过了几个月甚至只有几天就偏差很大了,性能不稳定。”
据中国机器人产业联盟统计,中国市场对多关节机器人的需求为3.6万台,供应商仍以外资品牌为主。
相比外资以生产线为单位动辄数百台的大批量订单,国产工业机器人的出货单位,往往只有个位数。
唯一相对较有竞争优势的领域,是较为低端的坐标型机器人。广州数控设备有限公司(下称广州数控)总经理助理蒋米仁判断,“国内做四轴以上机器人的不多,销量最多在三四千台左右。”
但这三四千台的出货量,已经挑动了“四大家族”的神经。曾苦于缺乏议价能力的张高强就发现,公司的几大供应商无论是安川还是ABB和库卡,都推出了不少降价措施,“有些幅度还比较大”。
一位国内机器人企业高管也证实,“有些国外的企业对中国有些比较热销的国产型号,比如说8KG六关节机器人还在逐步进行打压,将同型号价格调低,或者在一些主推领域给一些优惠。”他坦承,外资巨头的上述针对性措施,“对我们这些国内企业还是有一些压力的”。
进击2025
对“中国制造2025”来说,仅有智能制造远远不够,无论是出自“工业强基”的要求,还是从业者对在市场中占据主导地位的需求,具有自主知识产权的国产品牌机器人,才是种种相关政策的重点发展对象。
《指导意见》提出,到2020年,要形成较为完善的工业机器人产业体系,培育3家-5家具有国际竞争力的龙头企业和8个-10个配套产业集群,并将在高端市场的产品占有率目标定为45%。
一项针对汽车、机械加工、电子等主要机器人用户的调查显示,虽然销量排名前十位的机器人品牌全部来自国外,但购买者最感兴趣的十大机器人品牌中,广州数控,沈阳新松、南京埃期顿等国内品牌均有一席之地,分别为第五位、第六位和第九位。
对此,蒋米仁表示,“有些企业主还是有民族产业精神的。”他透露,“(用户)对我们国内的企业,一开始有些小故障不愿意用的情况存在,但是只要服务跟上,不要拖它的生产效率,他们还是愿意用。
毕竟中国的中小企业还是大多数,物美价廉是一方面,服务相对国外也比较及时,国外是觉得服务是一定要额外付费的,国内的很多企业也有买得起用不起的问题存在。”
这种与使用者保持密切接触的做法,是蒋米仁眼中广州数控的成功经验。“不仅是产学研,应该是产学研用一体化。”由企业把终端用户带入整个研发生产体系,“时不时去跟踪,反推产品存在的问题,才能更加贴近市场”。
2014年,广州数控宣布攻克了减速器难关,自此“掌握了被国外垄断的工业机器人本体制造的全套核心技术”。“现在我们被发改委、工信部认定是最有希望首批实现自有技术批量生产的企业。”
蒋米仁透露,广州数控今年有望达到千台出货量,这也是机器人制造企业实现盈利的临界点;未来的计划则与《指导意见》十分相近——将市场占有量做到3万台,占据中国40%的工业机器人市场。
在接受记者采访时,蒋仕元曾经提到,减速器和控制器应用不过关,是限制国产机器人质量水平的最大因素。
除了广州数控这样的整机生产企业,不少企业也正在专注于机器人关键零部件的研发。
以减速器为例,南通振康焊接电机有限公司(下称南通振康)已在2014年实现机器人用减速器的批量生产,包括ABB、库卡、发那科在内的一些大型外资厂商,以及国内企业埃夫特、埃期顿等,都已下单试用。
集成企业同样开始向专业化方向发展。“机器人应用领域非常广,焊接、喷涂、打磨的重力感应,应用性的关键技术,要融合到产品中还是要更完美一点。原来多数是自动化企业或数控企业转型,但在设计和施工过程,特别是设计生产工序时,要跟工艺整合起来,除了自动化生产线的经验,在各个应用领域比如化工、焊接、喷涂方面的经验要求也很高。今后会发展出很多小精专的集成商。”蒋米仁指出。
对于原本就擅长物流分拣的力生公司来说,生产企业的包装码垛工序,特别是带有视觉感应的智能化分拣包装,以及远程系统控制,正是他们未来计划的主攻方向。
比如说视觉,产品的包装可能有2公斤的、5公斤的等不同规格,带有视觉感应的机器人只要一看,就可以知道用什么样的规格进行包装,不用再进行人工操作,这才叫智能化。
尽管视觉感应、远程控制等在国外的工业制造企业中已经应用较为普遍,但受限于价格,在国内还并未普及。蒋仕元介绍称,“最便宜的视觉装置可能是3万元,要求高需要精准抓取的话,就要好几万元了。”但他强调,要真正实现智能化生产,机器人要能够适应更多规格的产品和更多的工种。
钱晖也重点向记者介绍了发那科的视觉感应,“目前全球最先进的我们叫三维视觉。打比方说,没有视觉的上下料,要让工人先一个个取出来,放到一个输送线上面,机器人才可能放到机床上去。我们现在的三维视觉,可以有不同的物料都放在同一个料筐里面,机器人都可以自行抓取,甚至还可以自己判断角度。”
除了视觉,在钱晖看来,要提升机器人控制器的能力,植入大量远程应用程序,是机器人产业未来的另一大发展方向。“实现‘中国制造2025’也好,‘工业4.0’也好,我们的智能化管理,就要由原本的车间级,延升至设备级甚至物料级。系统的智能化程度,决定了未来生产的智能化程度。”
外资企业最重视的这两大发展方向,也正是国内企业大力发展的部分。“像我们也在做一些数字化的车间,通过传感技术、工业以太网技术联动起来,借助总控台来指挥设备运动。
此外,公司还在研制远程故障诊断技术,实现设备远程故障排除等功能。”蒋米仁说。
声明:本网站所收集的部分公开资料来源于互联网,转载的目的在于传递更多信息及用于网络分享,并不代表本站赞同其观点和对其真实性负责,也不构成任何其他建议。本站部分作品是由网友自主投稿和发布、编辑整理上传,对此类作品本站仅提供交流平台,不为其版权负责。如果您发现网站上所用视频、图片、文字如涉及作品版权问题,请第一时间告知,我们将根据您提供的证明材料确认版权并按国家标准支付稿酬或立即删除内容,以保证您的权益!联系电话:010-58612588 或 Email:editor@mmsonline.com.cn。
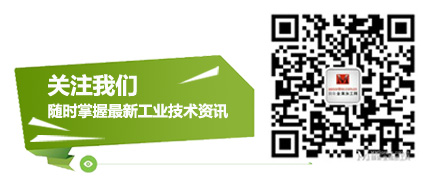
- 暂无反馈