用3D打印制造直升机叶片模具成本被削减70%
【编者按】3D打印通常是采用数字技术材料打印机来实现的。常在模具制造、工业设计等领域被用于制造模型,后逐渐用于一些产品的直接制造,已经有使用这种技术打印而成的零部件。
工业化、规模制造高度发达的今天,制造环节哪怕5%-10%的节约,都会被认为是重大进步,成本缩减超过30%?那简直是颠覆性的。
而知名的复合材料机械制造商Automated Dynamics,最近通过3D打印技术的应用,成功地将直升机叶片原型制造过程中的模具成本削减了60%-70%。
Automated Dynamics总部位于纽约的Schenectady。该公司自1984年成立以来,就专注于为高科技、高精密的航空航天、汽车、国防和石油工业提供可靠的复合材料结构。近日,航空航天领域的一位客户带着一份紧急订单找到了Automated Dynamics,要求制造出一个4英尺长的直升机叶片。
使用FDM技术3D打印的可溶性芯(后面棕色)开发一个4英尺长的直升机叶片,可降低60-70%模具成本。
Automated Dynamics公司销售与市场营销副总裁Ralph Marcario指出,该公司的工程团队已经发现,使用传统的陶瓷或金属牺牲模板(sacrificialcores)法来制造这类产品,导致模具成本非常之高。于是,工程师们转向使用FDM(熔融沉积成型)3D打印技术打造可溶性内核,以完成这次直升机叶片的订单,寻求在降低模具成本的同时,也能制造出适度高品质的原型。
“当选择金属模具时,往往需要进行大量的工程设计,但是,在选择使用FDM技术制造的模具时,工程师们的设计工作量就变得少了。”Automated Dynamics公司机械设计工程师兼项目经理John Michasiow说。“在某些情况下,金属模具甚至都不用考虑,我们估计在模具方面的成本节约最少都能达到60%-70%的水平。”
为了制造直升机叶片的模具,Automated Dynamics的团队找到了Stratasys公司的经销商CADimensions,由后者在Fortus400mc 3D制造系统中,使用可耐高温的SR-100可溶性支撑材料3D打印出所需的可溶性芯。在24小时内,该复合成分被Stratasys Direct Manufacturing完全溶解。如果使用金属模具的话,这些部件的生产周期大约需要六个星期,但是通过使用FDM可溶性芯,整个过程被缩短到大约1周的时间。
将Stratasys公司的FDM技术应用在可溶性芯模制造中,导致了更快的生产时间和成本的削减,避免了可以说是相当困难的去除过程。这一技术可以说逆转了支撑材料在一般3D打印过程中的作用。在这里,热塑性材料被用于制作支撑模型,而可溶性的支撑材料却被用来制作芯模。在制造过程中,只需简单地除去热塑性支撑后暴露出芯模,并用选定的复合材料将其缠绕起来,然后使覆盖在可溶性芯上的复合材料固化,最后将其浸入水中,使芯模溶解。
通过FDM技术的使用,而不是翻盖模具(clam shell tooling)和粘接,最终制造出了强度更高的部件,并可以实现更多的几何形状,所有这些都在更短的时间里,以一个低得多的成本完成。
声明:本网站所收集的部分公开资料来源于互联网,转载的目的在于传递更多信息及用于网络分享,并不代表本站赞同其观点和对其真实性负责,也不构成任何其他建议。本站部分作品是由网友自主投稿和发布、编辑整理上传,对此类作品本站仅提供交流平台,不为其版权负责。如果您发现网站上所用视频、图片、文字如涉及作品版权问题,请第一时间告知,我们将根据您提供的证明材料确认版权并按国家标准支付稿酬或立即删除内容,以保证您的权益!联系电话:010-58612588 或 Email:editor@mmsonline.com.cn。
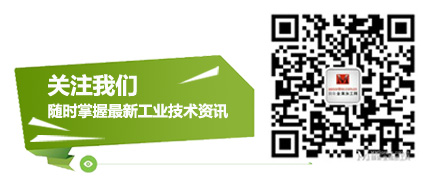
- 暂无反馈