刀具选择的效率原则和精度原则分析
在金属切削加工中,刀具选择几乎是每一个工艺工程师必须面临的问题。刀具选择要考虑许多问题,相应地就有许多原则,如效率原则、加工精度原则、稳定性原则、经济性原则等等。
首先谈一下效率原则。效率原则其实与其他原则不可分割,尤其是经济性原则。要求效率的主要目的就是保证整个加工的经济性。但效率特别重要,所以把它独立出来,单独讨论一下。
效率原则首先是在保证可接受的加工精度和可接受的稳定性前提下的效率。没有这个基本条件,效率无从谈起。就像我们希望我们的交通工具(譬如汽车)能够给我们带来更快的速度,但安全是第一位的。一旦有飞机失事后,许多人会慎重考虑是否真的继续选择飞机出行,航空公司也会重新审视已有的安全策略。没有安全,飞机就不会成为首选的交通工具。刀具的选择同样如此。
其次,我们也不会在所有的条件下都强调效率,追求效率有一些约束条件。一个零件加工效率的提高需要与其他零件的效率相适应,一个工序的效率提高更需要与其他工序的效率相适应。如果忽视这些约束条件,一味追求效率,会吃力不讨好。就像上海到北京的火车,现在晚上8点左右发车,第二天早上10点到达。如果能够提前到8点到达,也许最受欢迎;但如果提前到6点,也许受欢迎程度反而下降。因为列车员会在到站前提前一个小时甚至两个小时整理旅客床铺,早上4点或5点起床大部分旅客不会太乐意的。工厂也是如此,尤其在流水线生产条件下更是如此。我们需要解决的是整个流水线中的“瓶颈”工序。只要提高了这个工序的生产能力,就能够提高整条生产线的生产能力,提高整个产品的生产能力,缩短制造周期,这是许多企业所期望的。而单机或柔性制造系统的需求又不一样。他们所受的约束较少,即与其他工序的相关度较小。由于柔性化,某个零件或某个工序制造周期的缩短常常意味着能够使该设备投入其他零部件或其他工序的生产,从而创造更多的效益。
我认为在市场竞争日益激烈的今天,企业对工艺工程师的期望已经不是解决简单的工艺问题,而是期望工艺工程师们能对企业有更大的贡献度。如果我们的工艺工程师能从企业全局出发,为企业改进制造流程作出贡献,一定会获得企业主的首肯和赞许。
就国外现代金属加工企业调查的数据,刀具本身在制造成本中所占比例并不是很高,通常在2%~4%之间,高的会到7%左右。但刀具对加工效率的影响却非常巨大。20多年前我参加机械部组织的“2000年机械产品振兴目标研究”时接触的一个观点给我留下了极其深刻的影响,10年外企的工作经历,使我对这个观点有了更深刻、更具体的感受。那就是所谓一台几十万美元的设备能否发挥应有的作用,常常取决于一把几美元的刀具。我曾经得到过的一个成本分析实例表明,减少30%的采购价格(指刀具性能没有任何改变)或延长50%的刀具寿命(通常需要依赖刀具制造者的技术进步)都只能降低制造成本1%左右——因为刀具成本只占到制造总成本的4%。但如果加工参数能提高20%,大约可以降低15%的制造成本——虽然如果切削速度提高20%,刀具成本会提高50%,但因为加工周期缩短,总成本还是有大幅度的下降。
我曾经拜访过一家上海的模具企业。这是一家技术曾经非常领先的企业,我们家保存的一块机械部质量信得过奖章的模具就是他们做的。
但当我成为一家国外公司的刀具销售工程师前去拜访的时候,他们已经日薄西山,没有什么竞争能力了。我走进他们的车间,眼前的一幕使我震惊。他们进口了价值几百万人民币的德国马豪公司的5轴联动加工中心,却在这些加工中心上使用价格极低、效率同样极低的高速钢铣刀进行加工。我仿佛看到了他们衰落的问题所在,当然可能这不是惟一的原因。加工理念和管理理念的落后,导致他们的生产效率低下;高昂的设备折旧,又使他们的制造成本完全没有竞争能力。因此,从这点上说,如何选择刀具,是否重视加工效率,也许就关系着企业的生死存亡。
除了加工效率原则之外,刀具对加工精度的影响也是需要考虑的,尤其是在精加工等加工精度、表面质量要求比较高的应用场合。
在粗加工的条件下,我们一般都会采用效率优先原则。在这一阶段,快速去除工件毛坯上的加工余量,快速接近工件完工尺寸的“净尺寸”状态,是我们考虑刀具选择及加工参数的第一要素。
但在精加工的条件下,情况会有很大差别。精加工时我们应该采用精度优先原则,即首先保证加工的尺寸精度、表面粗糙度和表面质量。
现在一种典型的优先考虑保证精度的刀具被国外许多刀具厂商所青睐,这就是接近完美90°主偏角的立铣刀。从数学上可以得出,如果用一个平面(对刀具而言是前刀面)去截一个圆柱面(理想的切削刃绕刀具轴线所形成的表面),只有在该平面包含圆柱面轴线(即刀具轴向前角为零)时,其截交线才会是一段直线。但这时刀刃受力通常不理想,常常需要用一个正的轴向前角来改善刀具的切削性能。但这样一来就产生了回转面的形状精度问题:一根交错的直线(切削刃)绕刀具轴线回转所产生的不是圆柱面,而是双曲面。只有切削刃成为椭圆的一部分时,它绕刀具轴线回转的结果才会形成圆柱面。
于是国外一些刀具公司先后开发了这样的刀具:肯纳金属的称为Mill1,山特维克可乐满的称为R390,而瓦尔特的则称为F4042。这些刀具的本质都是一样的,它们用一段曲线形的切削刃来构成接近完美的圆柱面。虽说不同直径的铣刀应该有不同的曲线,而刀片生产的经济性要求又不允许这样做,各厂用在不同直径上选用不同轴向前角的方法来改善其中的差异。这种产品开发的思路值得国内厂家好好学习。研究用户的需要,分析目前存在的问题,进而想方设法去为客户解决这些问题,是企业不断创新、不断进步、不断满足客户增长的需求的有效手段。
还有一些刀具是经过改进,能够一次加工达到最终质量要求的。也就是在原本用于粗加工的刀具上引入精度改进方案,从而使一次加工获得更好的精度和表面质量。车削用的Wiper刀片和铝合金钻孔用的三刃钻(如肯纳的TF钻)都是这样的例子。如果采用相同的进给量(如0.05mm),传统刀片加工的表面粗糙度比Wiper刀片的可高出5倍。这样加工精度得到了保证,许多时候甚至可以以车代磨。
等轴曲线的特点是任何对边的尺寸是相等的。这样就使钻头钻出的孔(尤其是钻入部分)丧失精度。一些廉价的钻头和廉价的刃磨设备导致或助长了这种现象。最终用户可能不得不增加一道扩孔的工序来纠正这种形状精度的误差。因此,重视刀片选择的精度原则同样可以帮助我们提高竞争能力
声明:本网站所收集的部分公开资料来源于互联网,转载的目的在于传递更多信息及用于网络分享,并不代表本站赞同其观点和对其真实性负责,也不构成任何其他建议。本站部分作品是由网友自主投稿和发布、编辑整理上传,对此类作品本站仅提供交流平台,不为其版权负责。如果您发现网站上所用视频、图片、文字如涉及作品版权问题,请第一时间告知,我们将根据您提供的证明材料确认版权并按国家标准支付稿酬或立即删除内容,以保证您的权益!联系电话:010-58612588 或 Email:editor@mmsonline.com.cn。
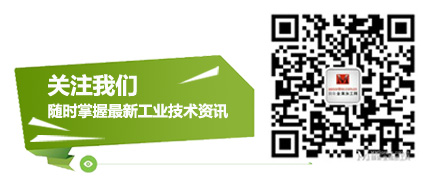
- 暂无反馈